PVD (Physical Vapor Deposition) plating is a highly durable and wear-resistant coating method used in various industries, including automotive, aerospace, and consumer goods. Unlike traditional plating methods, PVD creates a strong bond with the substrate, making it less likely to wear off under normal conditions. However, like any coating, its longevity depends on factors such as the quality of the application, the environment it is exposed to, and the type of substrate. While PVD plating is known for its durability, it is not completely immune to wear and tear, especially under extreme conditions or improper handling.
Key Points Explained:
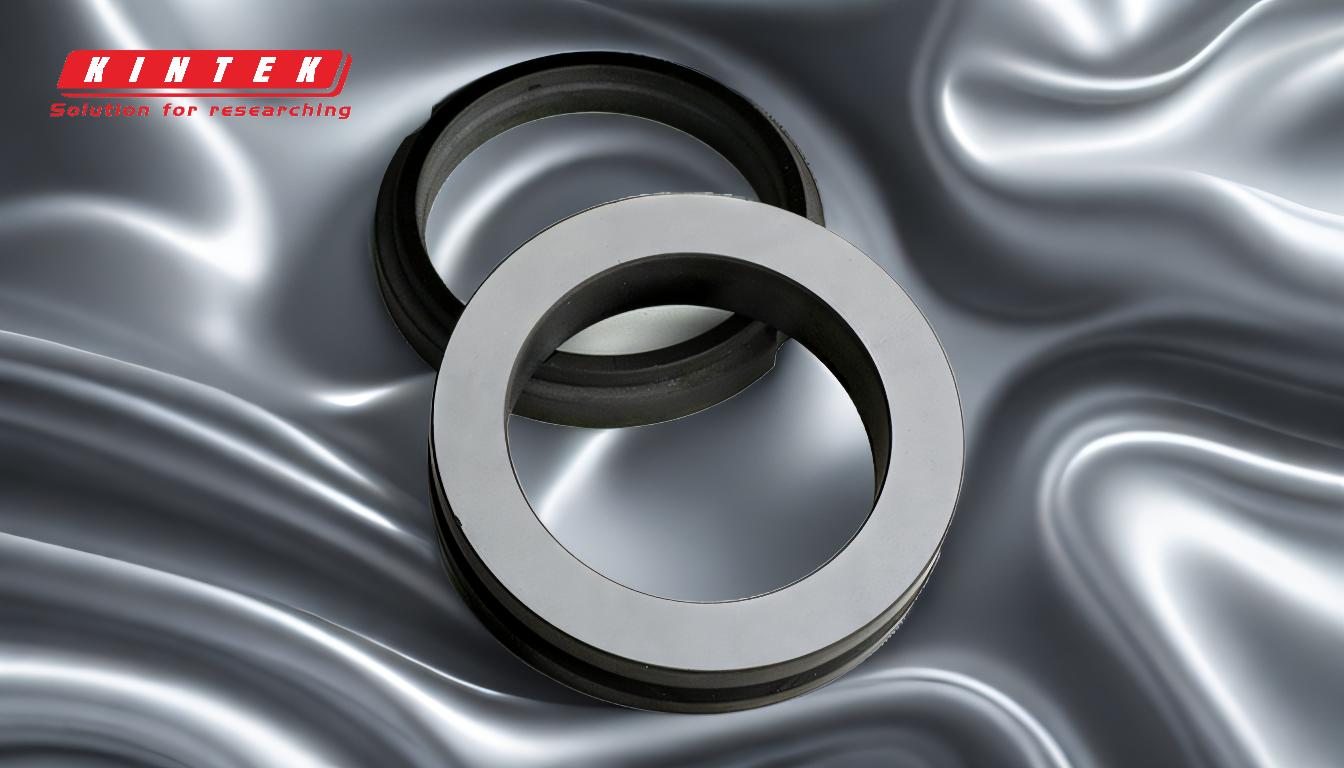
-
What is PVD Plating?
- PVD plating is a vacuum coating process where a thin layer of material is deposited onto a substrate. This process involves vaporizing a solid material in a vacuum and then condensing it onto the substrate. The result is a highly durable and corrosion-resistant coating that adheres strongly to the surface.
-
Durability of PVD Plating
- PVD coatings are known for their exceptional hardness and wear resistance. They are often used in applications where durability is critical, such as cutting tools, watch components, and automotive parts. The strong bond formed between the coating and the substrate makes PVD plating less likely to wear off compared to traditional electroplating methods.
-
Factors Affecting Wear and Tear
- Quality of Application: The durability of PVD plating depends on the quality of the application process. Proper surface preparation, precise control of the deposition process, and the use of high-quality materials are essential for achieving a long-lasting coating.
- Environmental Conditions: Exposure to harsh environments, such as high humidity, extreme temperatures, or corrosive chemicals, can accelerate the wear of PVD coatings. However, PVD plating is generally more resistant to these conditions than other types of coatings.
- Substrate Material: The type of substrate material also plays a role in the longevity of PVD plating. Some materials may not bond as well with the PVD coating, leading to potential wear over time.
-
Maintenance and Care
- While PVD plating is highly durable, proper maintenance can extend its lifespan. Regular cleaning with mild detergents and avoiding abrasive materials can help preserve the coating. Additionally, avoiding exposure to harsh chemicals or extreme conditions can prevent premature wear.
-
Limitations of PVD Plating
- Despite its durability, PVD plating is not indestructible. In extreme conditions, such as high-impact environments or continuous exposure to abrasive materials, the coating may eventually wear off. However, this is typically after prolonged use and is less common in everyday applications.
-
Comparison with Other Coating Methods
- PVD plating is often compared to other coating methods, such as electroplating or powder coating. While electroplating can provide a similar appearance, it generally lacks the durability and wear resistance of PVD coatings. Powder coating, on the other hand, is thicker and more suitable for larger surfaces but may not offer the same level of precision or hardness as PVD plating.
In conclusion, PVD plating is a highly durable and wear-resistant coating method that is less likely to wear off under normal conditions. However, its longevity depends on factors such as the quality of the application, environmental conditions, and substrate material. With proper care and maintenance, PVD plating can provide long-lasting protection and aesthetic appeal for a wide range of applications.
Summary Table:
Key Aspect | Details |
---|---|
Durability | Highly durable and wear-resistant, with a strong bond to the substrate. |
Factors Affecting Wear | Quality of application, environmental conditions, and substrate material. |
Maintenance Tips | Clean with mild detergents, avoid abrasives, and protect from harsh conditions. |
Limitations | May wear off under extreme conditions or improper handling. |
Comparison with Others | More durable than electroplating; offers better precision than powder coating. |
Interested in PVD plating for your applications? Contact us today to learn more!