Carbon crucibles, particularly those made from silicon carbide or other advanced materials, are manufactured using specialized techniques to ensure high performance and durability. The process typically involves advanced molding methods, high-quality raw materials, and stringent quality control measures. Below is a detailed explanation of how carbon crucibles are made, focusing on the key steps and materials involved.
Key Points Explained:
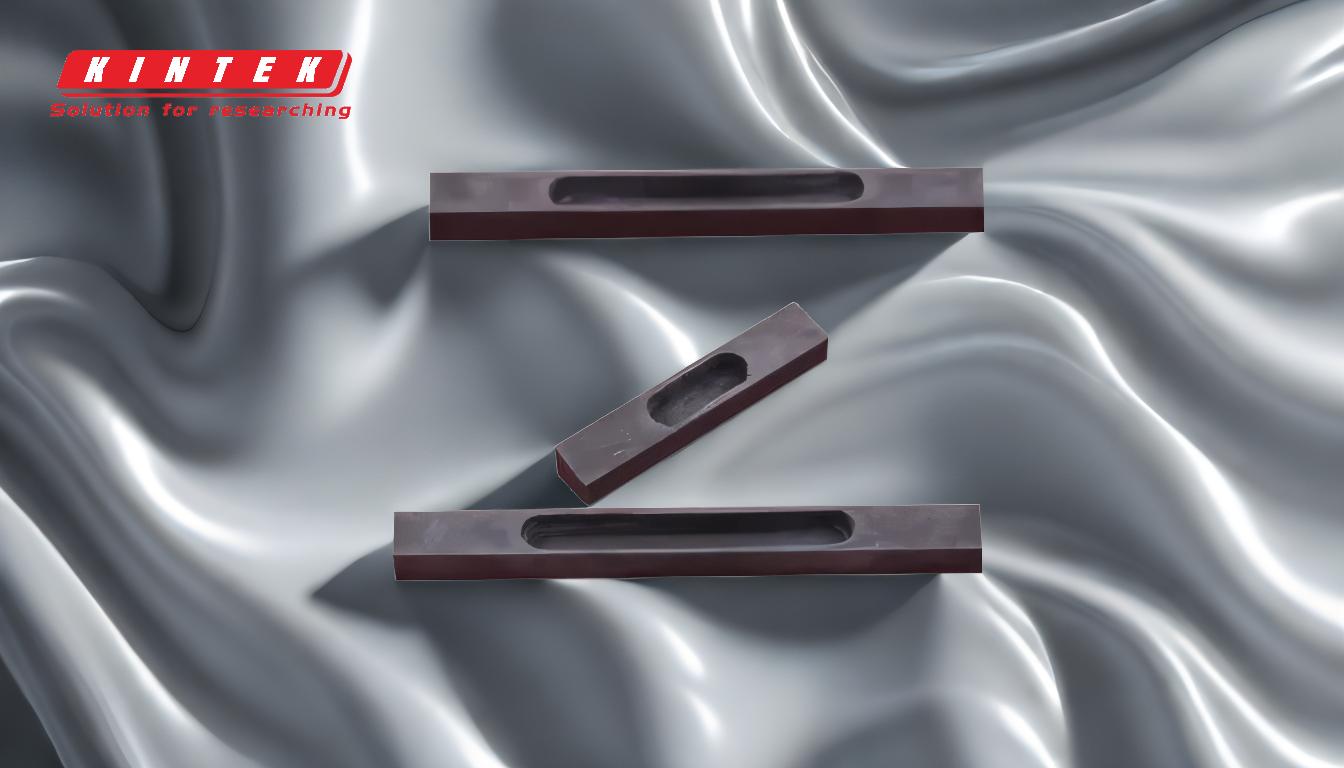
-
Raw Material Selection
- The production of carbon crucibles begins with the selection of high-quality raw materials. For silicon carbide crucibles, advanced refractory materials and high-tech formulas are used. These materials are chosen for their ability to withstand extreme temperatures, resist chemical erosion, and provide long service life.
- In the case of molybdenum crucibles, molybdenum powder is used as the primary raw material. This powder is selected for its high melting point, thermal conductivity, and mechanical strength.
-
Isostatic Molding
- The isostatic molding method is a key step in the production of carbon crucibles. This process involves applying uniform pressure from all directions to the raw material, ensuring a dense and homogeneous structure.
- For silicon carbide crucibles, this method helps achieve large volume density, which is critical for their high-temperature strength and resistance to acid erosion.
- For molybdenum crucibles, cold isostatic pressing is used to compact the molybdenum powder into a solid form before sintering.
-
Sintering Process
- After molding, the crucibles undergo a sintering process to bond the particles and enhance their mechanical properties. For molybdenum crucibles, this involves sintering in a circulating water-cooled intermediate frequency sintering furnace for approximately 9-10 hours.
- Sintering ensures the crucibles achieve the desired density, strength, and thermal stability.
-
Forging and Machining
- Molybdenum crucibles are further processed by forging and machining. The molybdenum rod is forged using a 1000 kg air hammer in a muffle furnace, which improves its structural integrity.
- After forging, the crucibles are machined to form grooves and achieve the desired surface roughness (typically Ra1.6 - Ra3.2μm). This step ensures precision and smoothness, which are essential for their performance in high-temperature applications.
-
Quality Assurance
- A strict quality assurance inspection system is implemented throughout the manufacturing process. This includes testing for density, thermal resistance, and mechanical strength to ensure the crucibles meet industry standards.
- The use of advanced quality control measures ensures that the crucibles have a service life 3-5 times longer than traditional clay graphite crucibles.
-
Final Properties
- The finished carbon crucibles exhibit properties such as high-temperature strength, acid erosion resistance, and large volume density. These properties make them suitable for demanding applications in industries like metallurgy, chemical processing, and materials research.
In summary, the production of carbon crucibles involves a combination of advanced materials, precise molding and sintering techniques, and rigorous quality control. These steps ensure that the crucibles meet the high standards required for industrial and scientific applications.
Summary Table:
Step | Description |
---|---|
Raw Material Selection | High-quality materials like silicon carbide or molybdenum powder are chosen for durability. |
Isostatic Molding | Uniform pressure ensures a dense, homogeneous structure for high-temperature strength. |
Sintering Process | Particles are bonded to enhance density, strength, and thermal stability. |
Forging and Machining | Molybdenum rods are forged and machined for structural integrity and precision. |
Quality Assurance | Rigorous testing ensures density, thermal resistance, and mechanical strength meet industry standards. |
Final Properties | Crucibles exhibit high-temperature strength, acid resistance, and large volume density. |
Interested in high-performance carbon crucibles? Contact us today to learn more!