Heat treatment furnaces are classified based on several factors, including the type of heat treatment they perform, their operating temperature ranges, the source of heat, and their structural design. For example, furnaces are categorized into low-temperature (0–700°C), general-purpose (700–1050°C), and high-temperature (1000–1400°C) ranges, each suited for specific processes like tempering, hardening, or carburizing. Additionally, they can be classified by heat source, such as solid, liquid, or gaseous fuels, and by design, including vertical, horizontal, single-chamber, or multi-chamber configurations. Specialized furnaces like roller hearth or integral-quench furnaces are also used for specific treatments like annealing.
Key Points Explained:
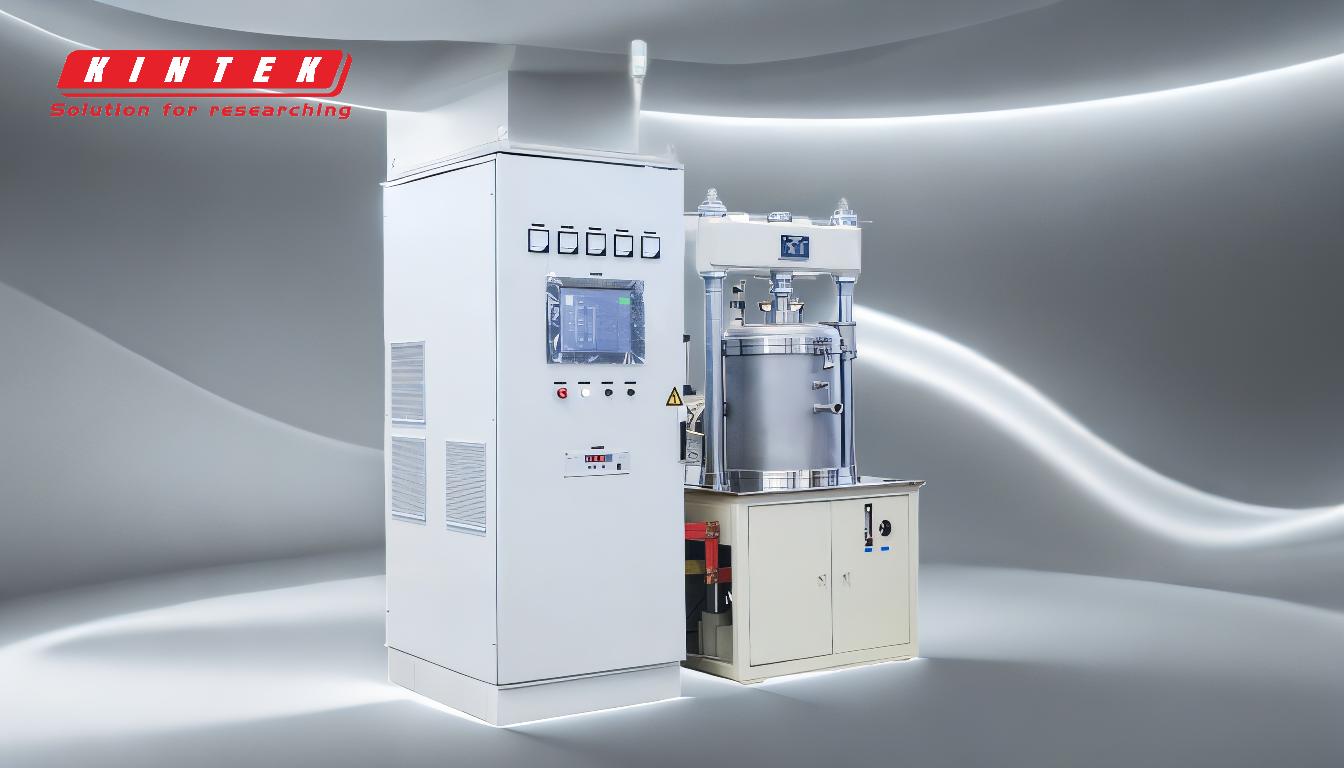
-
Classification by Heat Treatment Process:
- Low-Temperature Furnaces (0–700°C): Used for processes like tempering and sub-critical annealing. These furnaces often employ dry heat with forced air circulation or liquid baths (oil, lead, or salt).
- General-Purpose Furnaces (700–1050°C): Suitable for hardening, normalizing, and carburizing of carbon and low alloy steels.
- High-Temperature Furnaces (1000–1400°C): Designed for heat treatment of high-speed steels and other high-temperature cycles.
- Specialized Furnaces: Carburizing or carbonitriding furnaces are used for specific treatments requiring precise control of carbon or nitrogen content.
-
Classification by Heat Source:
- Solid Fuels: Includes coal, pulverized coal, and coke. These are chosen based on availability, cost, and technical suitability.
- Liquid Fuels: Such as gasoline and kerosene, which are often used for their ease of handling and consistent heat output.
- Gaseous Fuels: Includes coal gas and producer gas, which are preferred for their clean combustion and ease of control.
-
Classification by Structural Design:
- Vertical vs. Horizontal: Vertical furnaces are often used for compact spaces or specific processes, while horizontal furnaces are more common for general-purpose applications.
- Single-Chamber vs. Multi-Chamber: Single-chamber furnaces are simpler and more cost-effective, while multi-chamber furnaces allow for sequential processing and better temperature control.
- Modern Vacuum Furnaces: These are typically endothermic, with the entire shell serving as the vacuum container, and are available in vertical, horizontal, single-chamber, or three-chamber configurations.
-
Specialized Furnaces for Specific Processes:
- Roller Hearth Furnaces: Ideal for continuous annealing processes, allowing for uniform heating and cooling.
- Pusher Furnaces: Used for batch processing, where workpieces are pushed through the furnace in a controlled manner.
- Box Furnaces: Suitable for small-scale or batch heat treatment, offering flexibility in processing different materials.
- Pot/Pit Furnaces: Often used for localized heat treatment or processes requiring immersion in a liquid medium.
- Conveyor Belt Furnaces: Designed for continuous processing of small parts, ensuring consistent heat treatment.
- Integral-Quench Furnaces: Combine heating and quenching in a single unit, reducing handling and improving efficiency.
-
Considerations for Equipment Purchasers:
- Temperature Range: Ensure the furnace can handle the required temperature range for the intended processes.
- Fuel Type: Choose a furnace that uses a fuel type that is cost-effective and readily available.
- Design and Configuration: Consider the space available and the specific needs of the heat treatment process when selecting between vertical, horizontal, single-chamber, or multi-chamber designs.
- Specialized Features: For processes like annealing or carburizing, specialized furnaces like roller hearth or integral-quench furnaces may be necessary.
By understanding these classifications, purchasers can make informed decisions that align with their specific heat treatment needs, ensuring optimal performance and cost-efficiency.
Summary Table:
Classification | Key Features |
---|---|
By Heat Treatment Process | - Low-Temperature (0–700°C): Tempering, sub-critical annealing. |
- General-Purpose (700–1050°C): Hardening, normalizing, carburizing. | |
- High-Temperature (1000–1400°C): High-speed steel treatments. | |
- Specialized: Carburizing, carbonitriding furnaces. | |
By Heat Source | - Solid Fuels: Coal, coke. |
- Liquid Fuels: Gasoline, kerosene. | |
- Gaseous Fuels: Coal gas, producer gas. | |
By Structural Design | - Vertical, Horizontal, Single-Chamber, Multi-Chamber, Modern Vacuum Furnaces. |
Specialized Furnaces | - Roller Hearth, Pusher, Box, Pot/Pit, Conveyor Belt, Integral-Quench Furnaces. |
Need help choosing the right heat treatment furnace? Contact our experts today!