Thin films are created using a variety of deposition techniques that allow precise control over thickness, composition, and properties. These methods can be broadly categorized into physical, chemical, and electrically-based processes. Common techniques include evaporation, sputtering, chemical vapor deposition (CVD), spin coating, and more specialized methods like Langmuir-Blodgett film formation. Each method has unique advantages and is chosen based on the desired film properties and application, such as semiconductors, flexible solar cells, or OLEDs. The process typically involves depositing a thin layer of material onto a substrate, often within a vacuum chamber, to achieve atomic-level precision.
Key Points Explained:
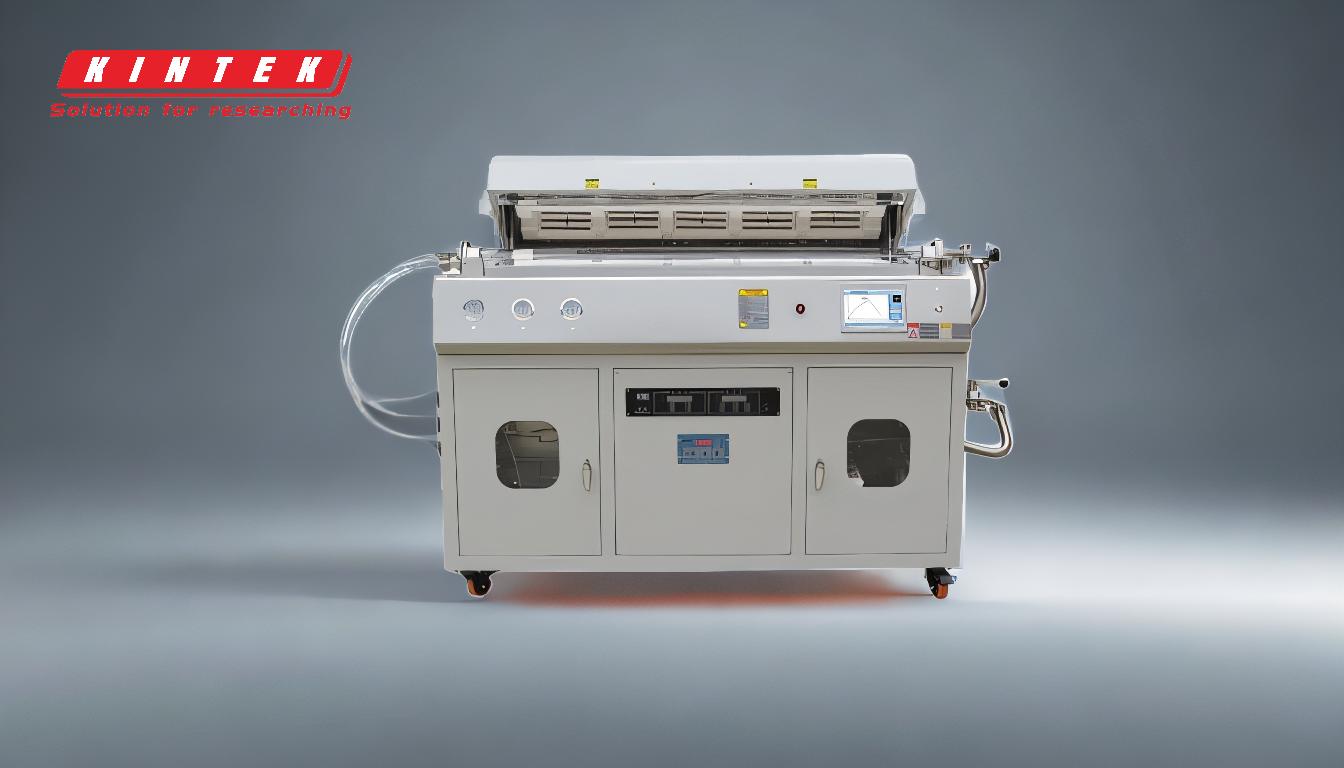
-
Overview of Thin Film Deposition:
- Thin films are layers of material deposited onto a substrate, often with thicknesses ranging from a few nanometers to several micrometers.
- The process is called deposition and involves precise control over the thickness, composition, and properties of the film.
- Applications include semiconductors, flexible electronics, solar cells, and OLEDs.
-
Physical Deposition Methods:
- Evaporation: A material is heated in a vacuum until it vaporizes, and the vapor condenses onto the substrate to form a thin film. This method is used for metals and simple compounds.
- Sputtering: A target material is bombarded with high-energy ions, causing atoms to be ejected and deposited onto the substrate. This technique is widely used for creating uniform films of metals, alloys, and ceramics.
- Ion Beam Deposition: A focused ion beam is used to deposit material onto the substrate, offering high precision and control.
-
Chemical Deposition Methods:
- Chemical Vapor Deposition (CVD): A chemical reaction occurs in a gas phase, producing a solid material that deposits onto the substrate. CVD is used for creating high-quality films of semiconductors, oxides, and other materials.
- Atomic Layer Deposition (ALD): A variant of CVD where films are deposited one atomic layer at a time, allowing for extremely precise control over thickness and composition.
-
Solution-Based Techniques:
- Spin Coating: A solution containing the material is applied to a substrate, which is then spun at high speed to spread the solution into a thin, uniform layer. This method is commonly used for polymers and organic materials.
- Dip Casting: The substrate is dipped into a solution, and a thin film forms as the solvent evaporates. This is a simple and cost-effective method for creating thin films.
- Langmuir-Blodgett Film Formation: A monolayer of molecules is spread on a liquid surface and then transferred onto a substrate. This method is used for creating highly ordered thin films.
-
Electrically-Based Methods:
- Electroplating: An electric current is used to deposit a thin layer of metal onto a conductive substrate. This method is used for creating metal films in electronics and decorative coatings.
- Plasma-Enhanced CVD (PECVD): A plasma is used to enhance the chemical reactions in CVD, allowing for lower deposition temperatures and better control over film properties.
-
Specialized Techniques:
- Self-Assembled Monolayers (SAMs): Molecules spontaneously organize into a single layer on a substrate. This method is used for creating highly ordered and functionalized surfaces.
- Layer-by-Layer (LbL) Assembly: Alternating layers of different materials are deposited onto a substrate, often using electrostatic interactions. This technique is used for creating multilayer films with tailored properties.
-
Applications of Thin Films:
- Semiconductors: Thin films are critical for the fabrication of integrated circuits and other electronic components.
- Flexible Electronics: Thin films of polymers and organic materials are used in flexible solar cells, OLEDs, and wearable devices.
- Optical Coatings: Thin films are used to create anti-reflective coatings, mirrors, and filters for optical devices.
- Protective Coatings: Thin films are used to protect surfaces from corrosion, wear, and other environmental factors.
-
Advantages and Challenges:
- Advantages: Thin film techniques allow for precise control over material properties, enabling the creation of advanced materials with tailored functionalities. They are also scalable and can be used for large-area deposition.
- Challenges: Some methods require expensive equipment and controlled environments (e.g., vacuum chambers). Achieving uniformity and reproducibility can also be challenging, especially for complex materials.
By understanding these key points, one can appreciate the versatility and importance of thin film deposition techniques in modern technology and materials science. Each method offers unique advantages, and the choice of technique depends on the specific requirements of the application.
Summary Table:
Category | Techniques | Applications |
---|---|---|
Physical Deposition | Evaporation, Sputtering, Ion Beam Deposition | Metals, alloys, ceramics, semiconductors |
Chemical Deposition | Chemical Vapor Deposition (CVD), Atomic Layer Deposition (ALD) | High-quality films, semiconductors, oxides |
Solution-Based | Spin Coating, Dip Casting, Langmuir-Blodgett Film Formation | Polymers, organic materials, highly ordered films |
Electrically-Based | Electroplating, Plasma-Enhanced CVD (PECVD) | Metal films, electronics, decorative coatings |
Specialized Techniques | Self-Assembled Monolayers (SAMs), Layer-by-Layer (LbL) Assembly | Functionalized surfaces, multilayer films with tailored properties |
Applications | Semiconductors, flexible electronics, optical coatings, protective coatings | Integrated circuits, solar cells, OLEDs, anti-reflective coatings, wear resistance |
Ready to explore thin film deposition solutions for your project? Contact our experts today to get started!