XRF fused beads are prepared by melting a mixture of sample material and flux at high temperatures to create a homogeneous glass bead. This process reduces mineralogical and matrix effects, leading to more accurate analyses. However, it involves high sample dilution, which can negatively impact trace element analysis, and requires significant initial investment in fusion equipment and consumables like platinum crucibles. The resulting beads are typically thin, which can cause issues with infinite thickness for heavier elements.
Key Points Explained:
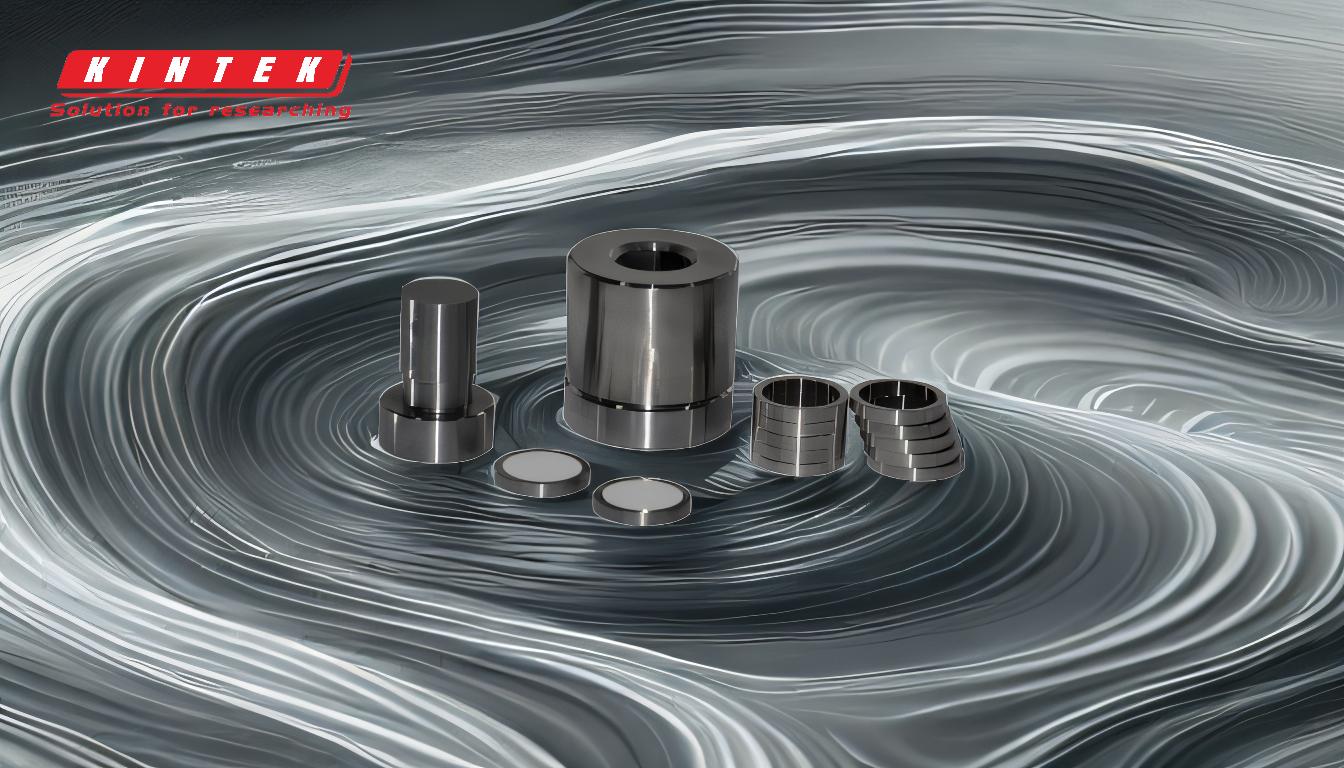
-
Reduction of Mineralogical and Matrix Effects:
- Fused beads are created by melting a sample with a flux, which homogenizes the material. This process minimizes variations in mineral composition and matrix effects, leading to more consistent and accurate XRF analyses.
-
Versatility in Calibration:
- The fusion process allows for the combination of different matrix types into a single calibration curve. This versatility is particularly beneficial when analyzing samples with varying compositions, as it simplifies the calibration process and enhances the flexibility of the analysis.
-
High Sample Dilution:
- One of the main drawbacks of using fused beads is the high dilution of the sample. The sample is mixed with a large amount of flux, which can dilute trace elements to levels that are difficult to detect accurately. This is a significant limitation for analyses requiring high sensitivity to trace elements.
-
Initial Costs and Equipment Requirements:
- Preparing fused beads requires specialized equipment, including fusion machines and platinum crucibles. The initial investment in these tools and consumables can be substantial, making this method more expensive compared to other sample preparation techniques.
-
Thin Beads and Infinite Thickness Issues:
- Fused beads are typically about 3mm thick. This thinness can lead to issues with infinite thickness, especially for heavier elements. Infinite thickness refers to the depth at which additional material does not affect the XRF signal. For heavier elements, the thinness of the bead may not provide sufficient material depth, potentially leading to inaccurate measurements.
-
Benefits vs. Downsides:
- While fused beads offer advantages like reduced matrix effects and versatile calibration, they also come with significant downsides such as high sample dilution, high initial costs, and potential issues with infinite thickness. These factors must be carefully considered when deciding whether to use fused beads for XRF sample preparation.
Summary Table:
Aspect | Details |
---|---|
Preparation Process | Melting sample material with flux at high temperatures to create a homogeneous glass bead. |
Reduced Matrix Effects | Minimizes mineralogical and matrix variations for more accurate XRF analyses. |
Versatility in Calibration | Combines different matrix types into a single calibration curve. |
High Sample Dilution | Trace elements may be diluted, impacting sensitivity. |
Initial Costs | Requires fusion machines and platinum crucibles, leading to high investment. |
Thin Beads & Infinite Thickness | 3mm thickness may cause issues for heavier elements. |
Need help with XRF fused bead preparation? Contact our experts today for tailored solutions!