To increase the efficiency of your induction furnace, you can focus on optimizing power usage, improving melting speed, and reducing energy losses. Key strategies include upgrading to IGBT induction technology, increasing power supply capacity, optimizing charge size and feeding methods, maintaining proper molten iron outlet temperatures, and minimizing thermal power loss. Additionally, using high-voltage primary coils, emptying the furnace completely after smelting, and incorporating waste heat recovery systems can further enhance efficiency. These measures collectively lead to faster heating, reduced energy consumption, and higher production output.
Key Points Explained:
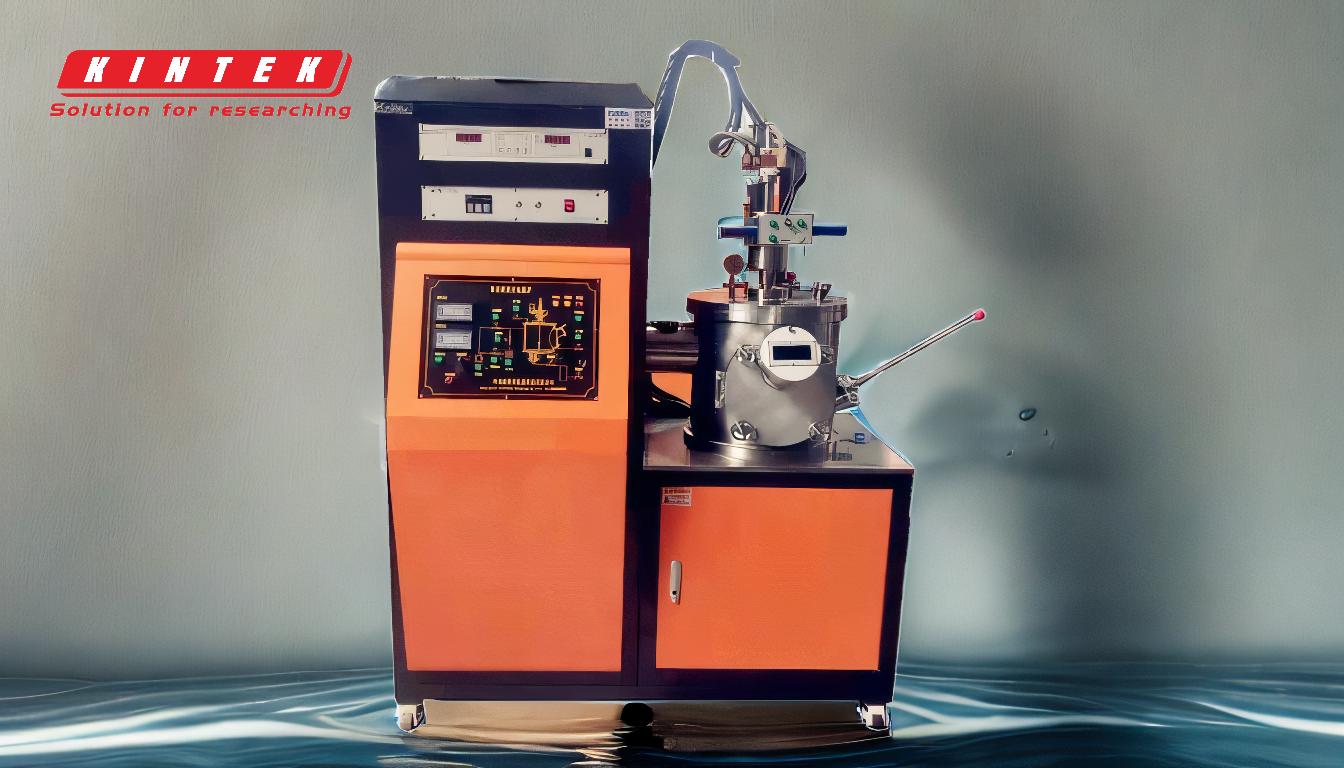
-
Upgrade to IGBT Induction Technology:
- IGBT (Insulated Gate Bipolar Transistor) induction technology is a modern advancement that significantly reduces energy consumption by 15-30%. This technology improves the overall efficiency of the furnace by optimizing power usage and minimizing heat loss.
-
Increase Power Supply Capacity:
- One of the most direct ways to increase melting speed is to boost the power of the induction furnace's power supply. A higher power supply allows for faster heating and melting, which in turn increases production efficiency.
-
Optimize Charge Size and Feeding Methods:
- Choosing the right charge size and feeding method is crucial for efficient melting. A well-sized charge ensures uniform heating, while the correct feeding method minimizes delays and energy wastage. Properly managing these factors can lead to faster melting times and reduced energy consumption.
-
Maintain Appropriate Molten Iron Outlet Temperature:
- Keeping the molten iron outlet temperature at an optimal level is essential for efficient operation. Too high a temperature can lead to excessive energy use, while too low a temperature can slow down the melting process. Maintaining the right balance ensures efficient energy use and faster processing.
-
Use High-Voltage Primary Coils:
- Induction furnaces with high-voltage primary coils can produce frequencies ranging from 50 Hz to 10,000 Hz. This high-frequency operation allows for rapid heating and higher thermal efficiency, leading to quicker melting times and reduced energy loss.
-
Empty the Furnace Completely After Smelting:
- Ensuring that the furnace is completely emptied at the end of the smelting process helps in proper separation of melted metal from impurities. This not only improves the quality of the output but also makes the furnace ready for the next batch more quickly, saving time and energy.
-
Minimize Thermal Power Loss:
- Reducing thermal power loss can be achieved by optimizing the space layout of the furnace and using materials that ensure smooth current flow. Minimizing these losses leads to more efficient energy use and lower operational costs.
-
Incorporate Waste Heat Recovery Systems:
- Adding a ceramic matrix recuperator to the exhaust system can recover waste heat and use it to preheat the combustion air. This method can improve energy efficiency by up to 50%, making the furnace more environmentally friendly and cost-effective.
-
Continuous Feeding of Auxiliary Stirring Steel:
- Continuously feeding auxiliary stirring steel into the furnace can increase the melting speed and reduce power consumption. This method ensures that the molten metal is uniformly heated, leading to more efficient melting and less energy waste.
By implementing these strategies, you can significantly enhance the efficiency of your induction furnace, leading to faster production times, reduced energy consumption, and higher overall output.
Summary Table:
Strategy | Key Benefit |
---|---|
Upgrade to IGBT Induction Technology | Reduces energy consumption by 15-30%, optimizing power usage and minimizing heat loss. |
Increase Power Supply Capacity | Boosts melting speed and production efficiency. |
Optimize Charge Size & Feeding Methods | Ensures uniform heating, faster melting, and reduced energy waste. |
Maintain Molten Iron Outlet Temperature | Balances energy use and processing speed for efficient operation. |
Use High-Voltage Primary Coils | Enables rapid heating and higher thermal efficiency. |
Empty Furnace Completely After Smelting | Improves output quality and reduces downtime. |
Minimize Thermal Power Loss | Enhances energy efficiency and lowers operational costs. |
Incorporate Waste Heat Recovery Systems | Recovers waste heat, improving energy efficiency by up to 50%. |
Continuous Feeding of Stirring Steel | Increases melting speed and reduces power consumption. |
Ready to optimize your induction furnace? Contact our experts today for tailored solutions!