Increasing the efficiency of an induction furnace, particularly an IGBT induction furnace, involves optimizing various aspects of its design, operation, and maintenance. By focusing on factors such as energy consumption, heat management, and process control, you can significantly enhance the furnace's performance and reduce operational costs. Below is a detailed breakdown of strategies to improve efficiency.
Key Points Explained:
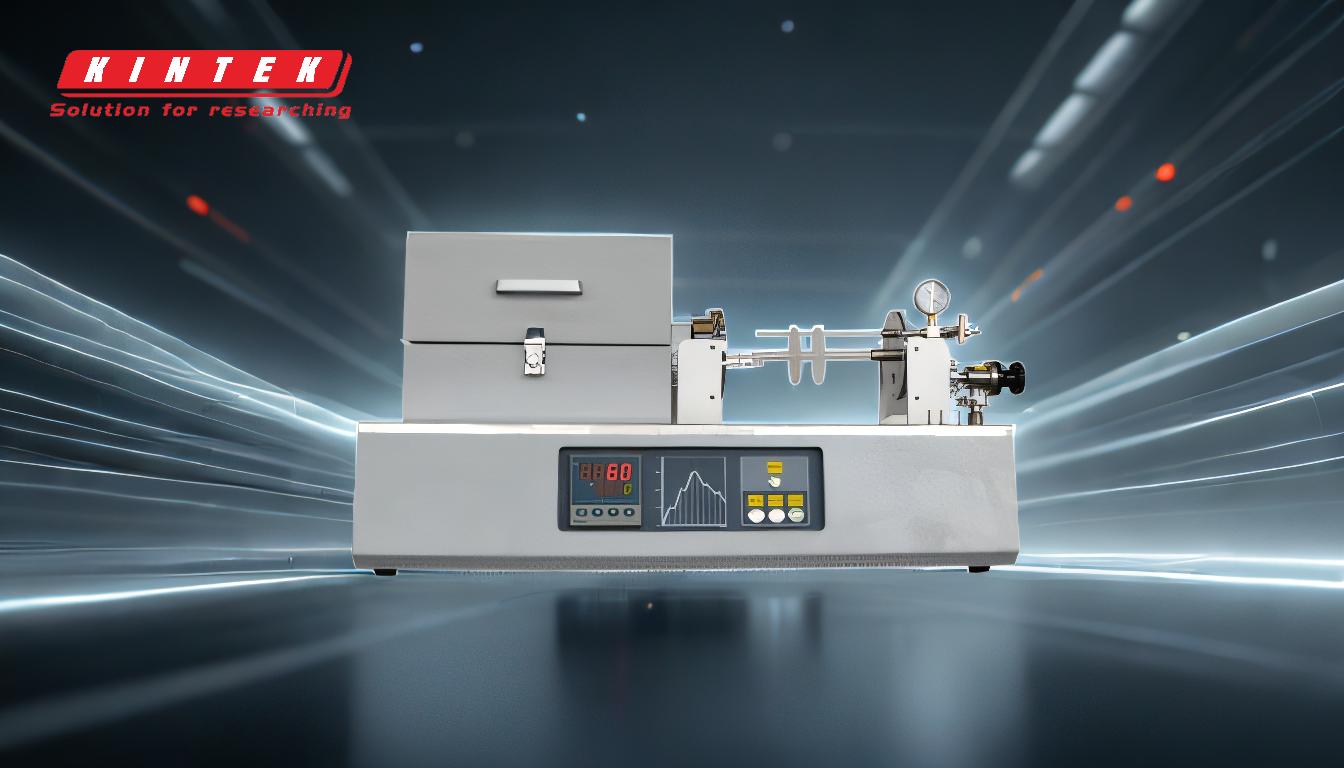
-
Optimize Power Supply and Frequency Settings
- Use IGBT Technology: IGBT (Insulated Gate Bipolar Transistor) induction furnaces are known for their high efficiency and precise control. Ensure the power supply is configured to match the furnace's requirements, as IGBT systems allow for better frequency modulation, reducing energy losses.
- Adjust Frequency: The frequency of the power supply should be optimized based on the material being melted. Lower frequencies are suitable for larger loads, while higher frequencies work better for smaller loads, improving energy efficiency.
-
Improve Thermal Insulation
- Upgrade Lining Materials: Use high-quality refractory materials for the furnace lining to minimize heat loss. Advanced materials like ceramic fiber or alumina-based linings can withstand high temperatures and reduce energy consumption.
- Seal Gaps and Leaks: Ensure the furnace is properly sealed to prevent heat from escaping. Regularly inspect and repair any gaps or cracks in the insulation.
-
Enhance Load Management
- Optimize Batch Sizes: Operate the furnace at or near its full capacity to maximize energy efficiency. Running the furnace with smaller loads increases energy consumption per unit of material.
- Preheat Charge Materials: Preheating the raw materials before loading them into the furnace reduces the energy required to reach melting temperatures, improving overall efficiency.
-
Implement Advanced Control Systems
- Automated Process Control: Use advanced control systems to monitor and adjust parameters like temperature, power input, and melting time in real-time. Automation ensures optimal performance and minimizes human error.
- Data Analytics: Collect and analyze operational data to identify inefficiencies and areas for improvement. Predictive maintenance systems can also help prevent downtime and maintain consistent performance.
-
Regular Maintenance and Upgrades
- Inspect and Replace Components: Regularly inspect critical components like coils, capacitors, and power supplies. Replace worn-out parts to maintain efficiency and prevent breakdowns.
- Upgrade to Modern Equipment: If using an older furnace, consider upgrading to a modern IGBT induction furnace with better energy efficiency and advanced features.
-
Reduce Heat Loss During Operation
- Minimize Open Lid Time: Keep the furnace lid closed as much as possible to prevent heat loss. Use automated lid systems to reduce exposure time.
- Use Heat Recovery Systems: Implement systems to capture and reuse waste heat generated during the melting process, such as preheating incoming materials or generating steam for other processes.
-
Train Operators for Efficient Operation
- Skill Development: Train operators on best practices for running the furnace efficiently, including proper loading techniques, monitoring procedures, and troubleshooting.
- Encourage Energy-Conscious Behavior: Promote a culture of energy efficiency among staff to ensure everyone contributes to optimizing furnace performance.
-
Monitor and Reduce Energy Consumption
- Install Energy Meters: Use energy meters to track power consumption and identify patterns or anomalies. This data can help pinpoint areas where energy usage can be reduced.
- Adopt Energy-Efficient Practices: Implement practices like scheduling operations during off-peak hours to take advantage of lower electricity rates.
By implementing these strategies, you can significantly increase the efficiency of your induction furnace, leading to higher productivity, reduced energy costs, and improved operational performance. The use of advanced technologies like IGBT induction furnaces further enhances these benefits, making them a valuable investment for modern industrial applications.
Summary Table:
Strategy | Key Actions |
---|---|
Optimize Power Supply | Use IGBT technology, adjust frequency based on material |
Improve Thermal Insulation | Upgrade lining materials, seal gaps and leaks |
Enhance Load Management | Optimize batch sizes, preheat charge materials |
Implement Advanced Control Systems | Use automation, data analytics, and predictive maintenance |
Regular Maintenance | Inspect and replace components, upgrade to modern equipment |
Reduce Heat Loss | Minimize open lid time, use heat recovery systems |
Train Operators | Develop skills, encourage energy-conscious behavior |
Monitor Energy Consumption | Install energy meters, adopt energy-efficient practices |
Ready to maximize your induction furnace efficiency? Contact our experts today for tailored solutions!