Calibrating a muffle furnace is a critical process to ensure accurate temperature readings and reliable performance. The process involves several steps, including initial setup, temperature adjustment, and verification of the furnace's functionality. Proper calibration ensures that the furnace operates within the desired temperature range, which is essential for consistent and accurate results in laboratory or industrial applications. Below is a detailed explanation of the calibration process, broken down into key steps and considerations.
Key Points Explained:
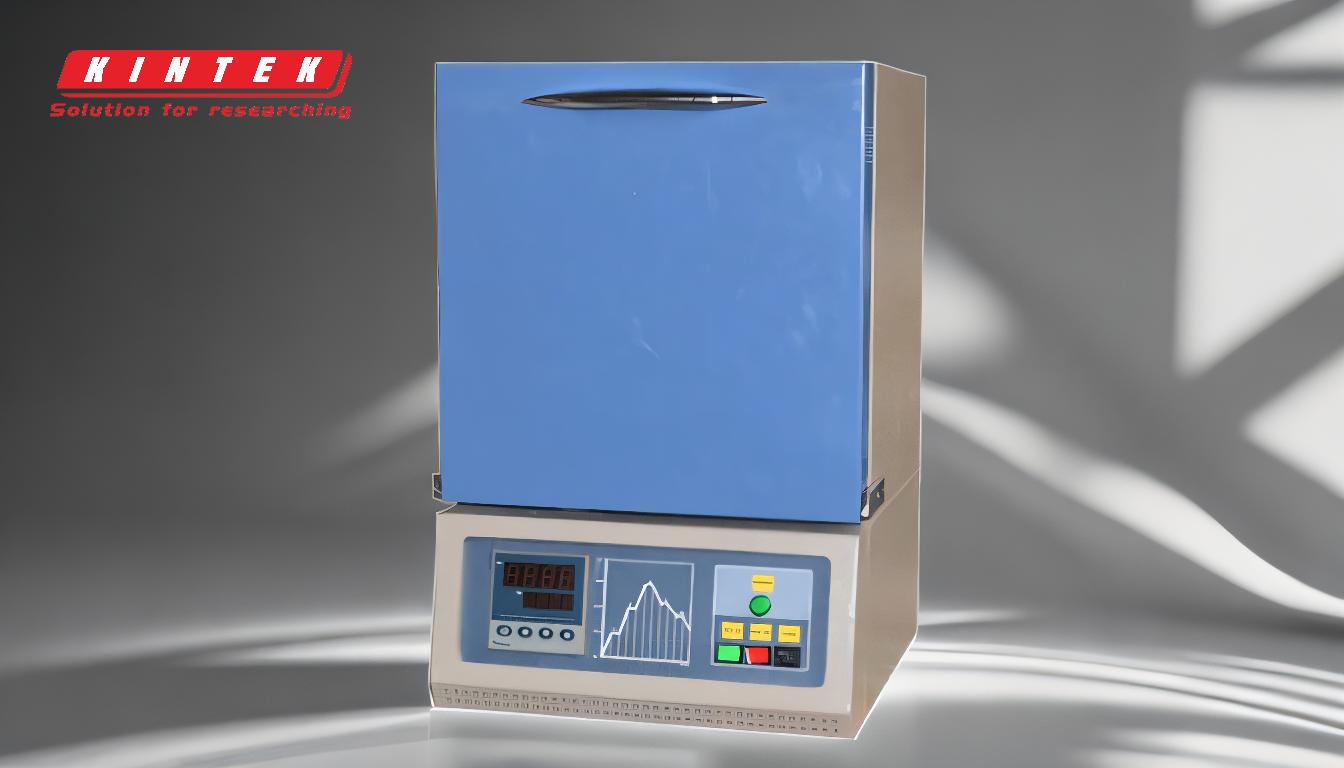
-
Initial Setup and Inspection
- After unpacking the muffle furnace, inspect it for any damage and ensure all accessories are present.
- Place the furnace on a flat, stable surface to avoid vibrations, which can affect its performance.
- Ensure the controller is not exposed to overheating or excessive heat sources, as this can interfere with its operation.
Why this matters: Proper setup ensures the furnace operates safely and efficiently. Any physical damage or missing components can lead to inaccurate temperature readings or operational failures.
-
Thermocouple Installation and Wiring
- Insert the thermocouple into the furnace, ensuring it is securely placed. Fill any gaps with asbestos rope to prevent heat loss.
- Connect the thermocouple to the controller using compensation wires, ensuring the correct polarity is maintained.
- Install a power switch at the power line inlet and ensure both the furnace and controller are properly grounded.
Why this matters: The thermocouple is the primary sensor for temperature measurement. Proper installation and wiring ensure accurate temperature readings and prevent electrical hazards.
-
Adjusting the Temperature Controller
- Before use, adjust the thermostat to zero points. If using a cold junction compensator, set the mechanical zero points to the reference temperature.
- If not using a cold junction compensator, adjust the mechanical zero-point to the zero scale. This indicates the temperature difference between the measuring point and the thermocouple's cold end.
Why this matters: Zeroing the controller ensures that the temperature readings are accurate and aligned with the actual furnace temperature.
-
Powering On and Initial Heating
- Set the desired temperature on the temperature controller and turn on the power.
- Observe the ammeter and temperature control meter. If the ammeter shows a reading and the temperature gradually rises, the furnace is functioning normally.
- Monitor the temperature indicator lights: green indicates heating, and red indicates the furnace has reached the set temperature.
Why this matters: This step verifies that the furnace and controller are working correctly and that the temperature is increasing as expected.
-
Temperature Calibration and Verification
- After the furnace reaches the set temperature, use a calibrated external thermometer or thermocouple to verify the accuracy of the furnace's temperature readings.
- If discrepancies are found, adjust the temperature controller accordingly to align the readings.
Why this matters: Calibration ensures that the furnace's internal temperature matches the set temperature, which is crucial for precise heating processes.
-
Stabilization and Testing
- For the first use or after a long period of disuse, allow the furnace to run empty for a period to stabilize the temperature and reduce impurities.
- Place a test sample in the furnace and monitor the temperature to ensure it remains consistent and accurate.
Why this matters: Stabilization ensures the furnace operates reliably and consistently, while testing with a sample confirms its readiness for actual use.
-
Post-Use Procedures
- After use, turn off the power and allow the furnace to cool to a safe temperature before removing samples.
- Regularly clean the furnace chamber and inspect the thermocouple and wiring for wear or damage.
Why this matters: Proper maintenance ensures the furnace remains in good working condition and extends its lifespan.
By following these steps, you can ensure that your muffle furnace is properly calibrated and ready for accurate and reliable operation. Regular calibration and maintenance are essential to maintain the furnace's performance and ensure consistent results in your heating processes.
Summary Table:
Step | Key Actions | Why It Matters |
---|---|---|
Initial Setup and Inspection | Inspect for damage, ensure accessories, place on stable surface, protect controller. | Ensures safe and efficient operation; prevents inaccurate readings or failures. |
Thermocouple Installation | Securely place thermocouple, fill gaps, connect to controller, ground properly. | Ensures accurate temperature readings and prevents electrical hazards. |
Adjusting Temperature Controller | Zero the thermostat or set mechanical zero points. | Aligns temperature readings with actual furnace temperature. |
Powering On and Heating | Set temperature, monitor ammeter and temperature control, observe indicator lights. | Verifies proper furnace and controller functionality. |
Temperature Calibration | Use external thermometer to verify accuracy; adjust controller if needed. | Ensures internal temperature matches set temperature for precise heating. |
Stabilization and Testing | Run empty to stabilize, test with sample to confirm consistency. | Ensures reliable operation and readiness for actual use. |
Post-Use Procedures | Turn off power, cool furnace, clean chamber, inspect thermocouple and wiring. | Maintains furnace condition and extends lifespan. |
Need help calibrating your muffle furnace? Contact our experts today for professional guidance!