Controlling high pressure in a reactor involves a combination of design, safety mechanisms, and operational strategies. High-pressure reactors are engineered to withstand extreme pressures and are equipped with features like pressure relief valves, sturdy materials, and inert inner surfaces to prevent corrosion. Pressure can be increased through heating, chemical reactions, or manual pressurization using inert gases. Safety is paramount, and proper monitoring and control systems are essential to prevent over-pressurization and ensure safe operation. Below, the key aspects of controlling high pressure in a reactor are explained in detail.
Key Points Explained:
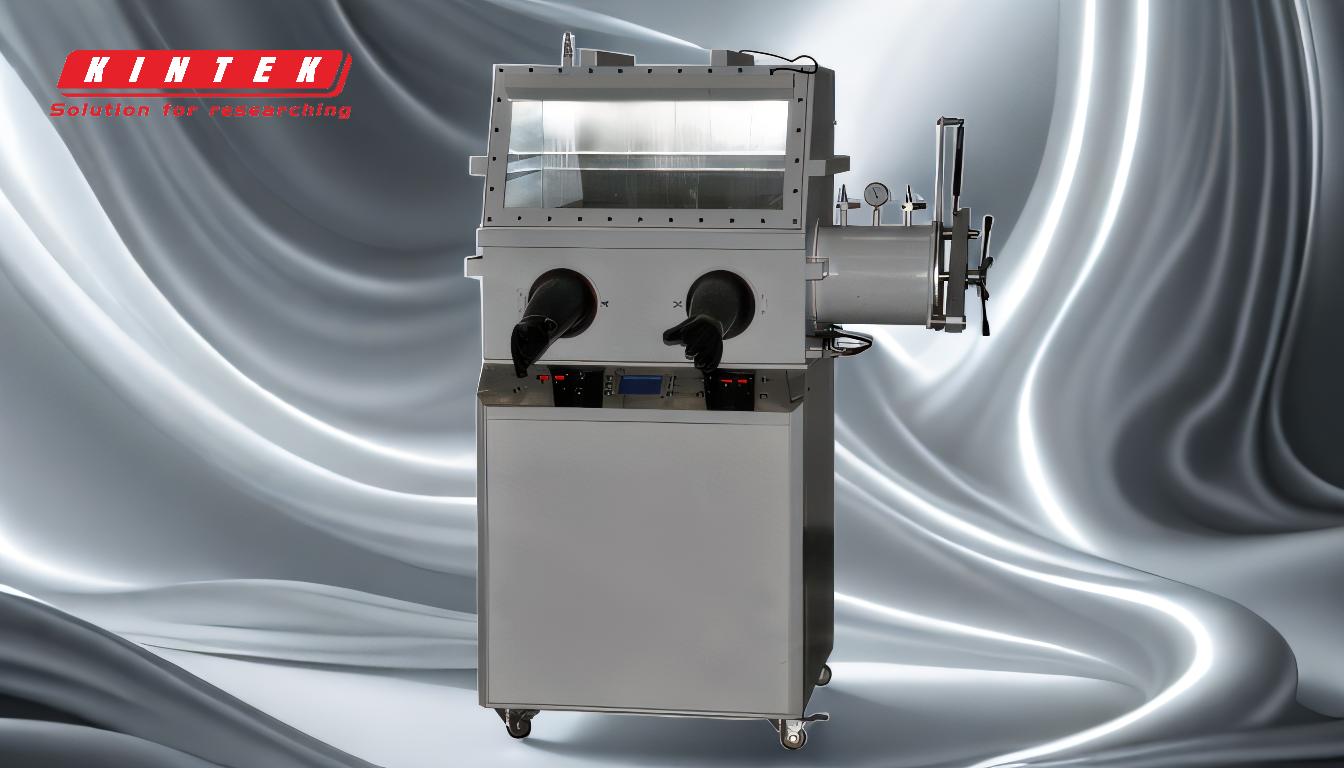
-
Design and Materials of High-Pressure Reactors
- High-pressure reactors are purpose-built vessels designed to withstand longitudinal and hoop stresses caused by internal pressure.
- They are constructed from durable materials, such as specialized alloys or reinforced designs, to ensure structural integrity under extreme conditions.
- The inner surface is often made inert to prevent corrosion or contamination, which could compromise the reactor's safety and performance.
-
Methods to Increase Pressure
- Heating: Heating a sealed reactor increases both temperature and pressure, as the gas or liquid inside expands. This method is effective for reactions that benefit from elevated temperatures.
- Chemical Reactions: Some reactions generate pressure as a byproduct. Agitation can accelerate this process, leading to faster pressure buildup.
- Manual Pressurization: When heating or reaction-generated pressure is insufficient or inappropriate, external pressurization is used. This involves introducing pressurized gas (e.g., from a compressor or pre-compressed canister) into the reactor.
-
Pressure Control Mechanisms
- Pressure Relief Valves: These are critical safety features that automatically release excess pressure to prevent over-pressurization and potential vessel failure.
- Monitoring Systems: Sensors and gauges are used to continuously monitor internal pressure, allowing operators to make adjustments as needed.
- Manual Adjustments: Operators can manually regulate pressure by adjusting gas flow, temperature, or agitation rates.
-
Safety Considerations
- High-pressure reactors require stringent safety measures due to the risks associated with extreme pressures.
- Safety features like pressure relief valves, burst disks, and fail-safes are essential to prevent accidents.
- Regular maintenance and inspection of the reactor and its components are necessary to ensure long-term safety and reliability.
-
Impact on Reaction Kinetics and Thermodynamics
- High-pressure environments can alter reaction kinetics and thermodynamic equilibrium, often leading to faster reaction rates and different product outcomes.
- This makes high-pressure reactors valuable for research and industrial applications where specific reaction conditions are required.
-
Challenges in High-Pressure Reactor Operation
- Safety Risks: The use of high pressures inherently increases the risk of accidents, necessitating robust safety protocols.
- Material Durability: The reactor and its components must be made from materials capable of withstanding extreme pressures without degrading.
- Cost and Complexity: Designing, constructing, and operating high-pressure reactors can be expensive and technically challenging.
By understanding these key points, operators and researchers can effectively control high pressure in reactors, ensuring safe and efficient operation while achieving desired reaction outcomes.
Summary Table:
Key Aspect | Details |
---|---|
Design & Materials | Built to withstand extreme pressures; durable alloys, inert inner surfaces. |
Pressure Increase Methods | Heating, chemical reactions, or manual pressurization with inert gases. |
Control Mechanisms | Pressure relief valves, monitoring systems, and manual adjustments. |
Safety Considerations | Relief valves, burst disks, fail-safes, and regular maintenance. |
Impact on Reactions | Alters kinetics and thermodynamics, enabling faster reactions. |
Operational Challenges | Safety risks, material durability, and high cost/complexity. |
Need help managing high-pressure reactor operations? Contact our experts today for tailored solutions!