Evaporating metal is a process commonly used in thin-film deposition, where a metal is heated to its vaporization point in a controlled environment, allowing its vapor to condense on a substrate to form a thin layer. This process is widely used in industries such as semiconductors, optics, and coatings. The key to evaporating metal lies in creating the right conditions—high vacuum and precise heating—to ensure the metal vaporizes without contamination or oxidation. Techniques like thermal evaporation and electron beam evaporation are commonly employed, each with specific advantages depending on the material and application.
Key Points Explained:
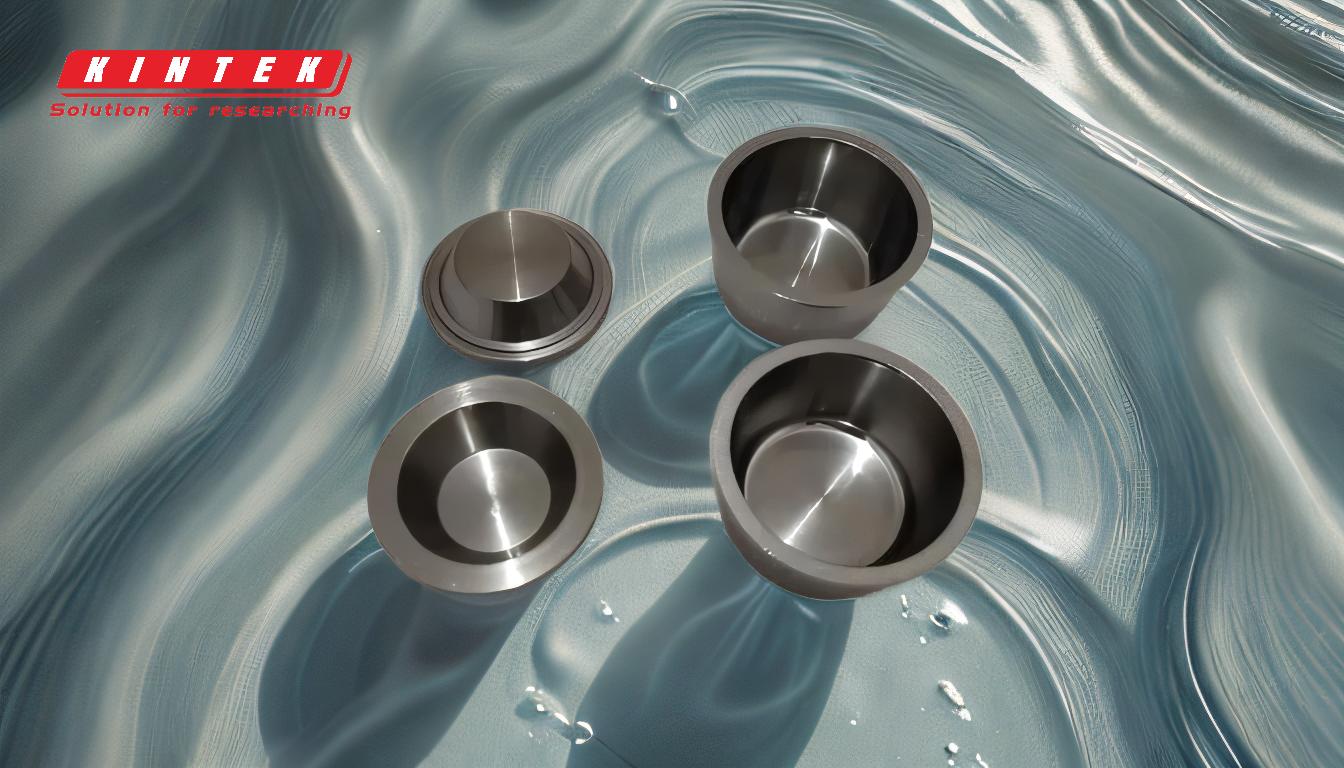
-
Understanding the Basics of Metal Evaporation
- Metal evaporation involves heating a metal until it vaporizes and then depositing the vapor onto a substrate to form a thin film.
- This process requires a high-vacuum environment to prevent contamination and ensure the vapor can travel freely to the substrate.
- The vacuum chamber, typically made of stainless steel, houses the crucible or boat (made of refractory materials like tungsten or molybdenum) that holds the metal to be evaporated.
-
Thermal Evaporation Techniques
- Resistive Heating Evaporation: The metal is heated using a resistive heating element, such as a tungsten filament or boat. This method is suitable for metals with lower melting points.
- Electron Beam Evaporation (E-Beam): A focused electron beam is used to heat the metal to extremely high temperatures, making it ideal for metals with high melting points. The electron beam is directed at the metal source, avoiding contamination of the filament.
- Flash Evaporation: Small amounts of metal are rapidly heated to vaporization, often used for materials that decompose at high temperatures.
- Induction Heating Evaporation: Uses electromagnetic induction to heat the metal, providing precise temperature control.
- Knudsen Cell Evaporation: A specialized method for evaporating materials with very low vapor pressures, often used in research settings.
-
Electron Beam Evaporation in Detail
- E-beam evaporation is particularly useful for depositing high-purity films of refractory metals and compounds.
- The process involves generating an electron beam from a tungsten filament, which is then directed onto the metal source using magnetic fields.
- The high-energy electrons strike the metal, heating it to the point of vaporization.
- One challenge is the production of X-rays, which can damage sensitive materials like CMOS layers on wafers. This is mitigated through annealing steps.
-
Materials Suitable for Evaporation
- A wide range of materials can be evaporated, including pure metals (e.g., aluminum, gold), as well as compounds like antimonides, arsenides, borides, carbides, fluorides, nitrides, oxides, selenides, silicides, sulfides, and tellurides.
- The choice of material depends on the desired properties of the thin film, such as conductivity, reflectivity, or chemical resistance.
-
Steps in the Metal Deposition Process
- Preparation: Start with a clean substrate, such as a silicon wafer.
- Loading: Place the metal to be evaporated into the crucible or boat.
- Evaporation: Heat the metal using the chosen technique (e.g., resistive heating or electron beam) until it vaporizes.
- Deposition: The metal vapor travels through the vacuum chamber and condenses onto the substrate, forming a thin film.
- Post-Processing: Annealing or other treatments may be applied to improve film quality or address issues like X-ray damage.
-
Applications of Metal Evaporation
- Semiconductors: Depositing thin films of metals like aluminum or copper for interconnects.
- Optics: Creating reflective coatings for mirrors or anti-reflective coatings for lenses.
- Coatings: Applying protective or decorative layers on various materials.
-
Advantages and Challenges
- Advantages: High-purity films, precise control over film thickness, and compatibility with a wide range of materials.
- Challenges: Requires specialized equipment, high energy consumption, and potential issues like contamination or X-ray damage.
By understanding these key points, one can effectively choose the appropriate evaporation technique and parameters for a specific application, ensuring high-quality thin-film deposition.
Summary Table:
Aspect | Details |
---|---|
Process | Heating metal to vaporize and deposit thin films on a substrate in a high-vacuum environment. |
Key Techniques | Thermal evaporation, electron beam evaporation, flash evaporation, induction heating. |
Materials | Pure metals (e.g., aluminum, gold) and compounds (e.g., oxides, nitrides). |
Applications | Semiconductors, optics, protective coatings. |
Advantages | High-purity films, precise thickness control, wide material compatibility. |
Challenges | Specialized equipment, high energy use, potential contamination or X-ray damage. |
Ready to optimize your thin-film deposition process? Contact our experts today for tailored solutions!