PVD (Physical Vapor Deposition) coatings are known for their exceptional durability, hardness, and resistance to corrosion and scratches. However, proper maintenance is essential to preserve their longevity and appearance. Maintenance primarily involves gentle cleaning with soft cloths, mild soap, and water, while avoiding harsh chemicals, abrasive materials, and cleaning agents containing acids or bleach. The lifespan of PVD coatings can vary significantly depending on factors such as substrate type, coating thickness, bond strength, and environmental exposure. By following simple care guidelines, PVD-coated items can retain their functionality and aesthetic appeal for years, even in harsh conditions.
Key Points Explained:
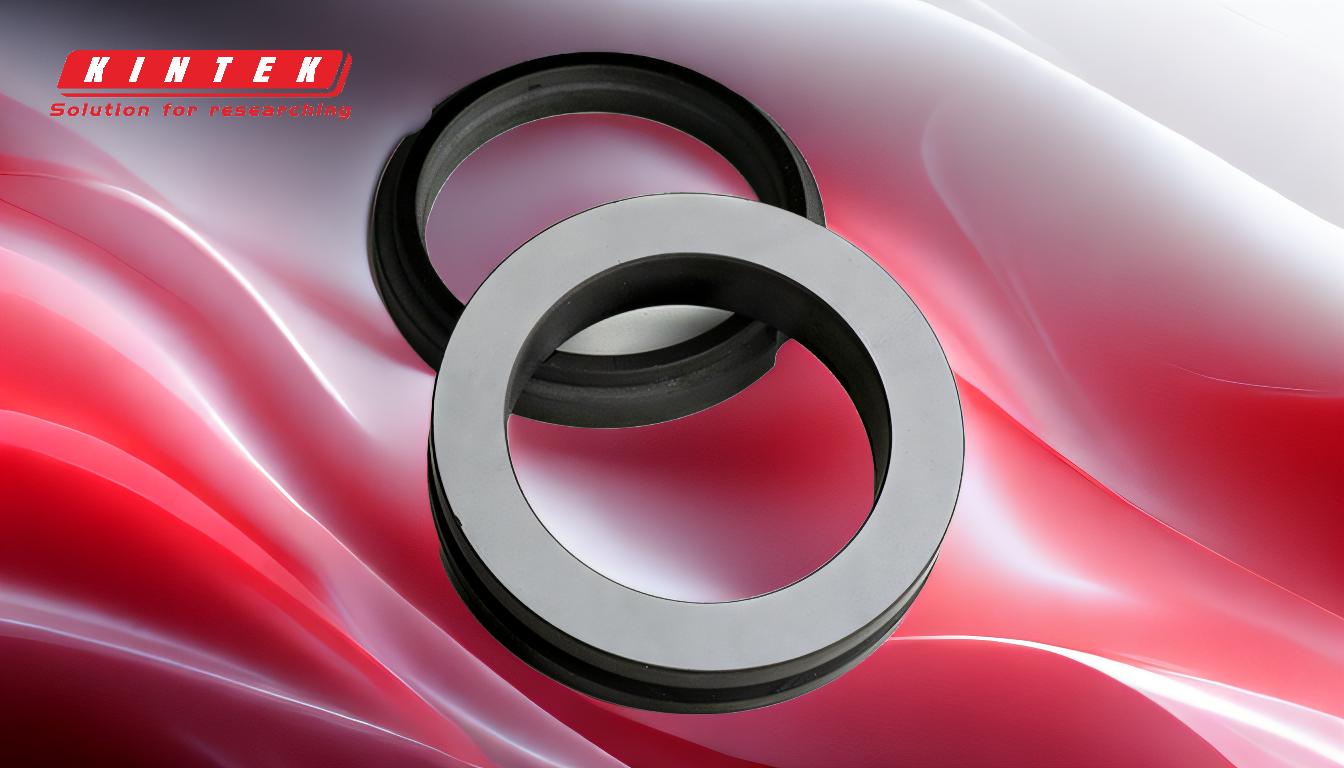
-
Daily Cleaning and Care:
- Use Soft Cloths: Clean PVD-coated surfaces with a soft, clean cotton or microfiber cloth to avoid scratches or abrasions.
- Mild Soap and Water: Use water and mild soap for cleaning. Avoid harsh chemicals or abrasive materials that could damage the coating.
- Avoid Acidic or Caustic Agents: Do not use cleaning products containing hydrochloric, hydrofluoric, phosphoric acid, or other caustic agents, as they can degrade the coating.
- No Bleach or Scouring Pads: Bleach and scouring pads are too abrasive and can strip or scratch the PVD coating.
-
Avoiding Damage:
- Prevent Hard Knocks: While PVD coatings are highly durable, they can still be damaged by hard impacts or repeated rubbing with abrasive materials.
- Environmental Exposure: Prolonged exposure to harsh environments, such as high temperatures or corrosive substances, can affect the coating's lifespan. Minimize such exposure when possible.
-
Factors Affecting Lifespan:
- Substrate Type: The material underneath the PVD coating plays a role in how long the coating lasts. A strong bond between the coating and substrate is crucial.
- Coating Thickness: Thicker coatings generally last longer but may require more precise application techniques.
- Bond Strength: The adhesion between the coating and the substrate determines how well the coating resists wear and tear.
- Application Conditions: The environment in which the PVD-coated item is used (e.g., coastal areas with salt exposure) can impact durability.
-
Durability of PVD Coatings:
- Hardness: PVD coatings are four times harder than chrome, making them highly resistant to scratches and wear.
- Corrosion Resistance: The coating's non-corrosive properties make it ideal for use in harsh environments, such as near the coast or in industrial settings.
- Longevity: With proper care, PVD coatings can last anywhere from 10 years to hundreds of years, depending on the application and maintenance.
-
PVD Coating Process:
- Vapor Deposition: The PVD process involves heating a target material until it vaporizes and then depositing the vapor onto the substrate in a vacuum environment. This ensures a pure, durable coating.
- Annealing Process: In some cases, the coating is removed and replaced through an annealing process, which requires specific temperature and time settings to maintain quality.
- Impurity-Free Coating: The vacuum environment ensures the coating is free from impurities, enhancing its durability and wear resistance.
-
Maintenance Simplicity:
- Easy Cleaning: Routine maintenance is straightforward and does not require specialized tools or products.
- Avoid Tarnish or Rust Removers: Products designed to remove tarnish or rust should not be used on PVD coatings, as they can damage the surface.
- Regular Inspections: Periodically inspect PVD-coated items for signs of wear or damage to address issues early and extend the coating's lifespan.
By following these guidelines, PVD-coated items can maintain their durability, functionality, and aesthetic appeal for an extended period, even in demanding environments. Proper care ensures that the coating's unique properties, such as hardness and corrosion resistance, are preserved over time.
Summary Table:
Key Maintenance Tips | Details |
---|---|
Daily Cleaning | Use soft cloths, mild soap, and water. Avoid harsh chemicals and bleach. |
Avoiding Damage | Prevent hard knocks and minimize exposure to harsh environments. |
Factors Affecting Lifespan | Substrate type, coating thickness, bond strength, and application conditions. |
Durability | Resistant to scratches, corrosion, and wear; lasts 10+ years with proper care. |
Easy Maintenance | No specialized tools needed; avoid tarnish or rust removers. |
Regular Inspections | Check for wear or damage to address issues early. |
Ensure your PVD-coated items stay durable and beautiful—contact us today for expert advice!