To melt copper using induction, an induction furnace is employed, which utilizes electromagnetic induction to generate heat within the metal. This method is highly efficient, offering precise temperature control and minimal metal loss, making it ideal for applications such as custom castings or large bronze structures. The process involves placing copper in a crucible within the furnace, where an alternating magnetic field induces eddy currents in the metal, causing it to heat up and melt. After melting, the liquid copper undergoes further processes like smelting, purifying, and casting to achieve the desired final product.
Key Points Explained:
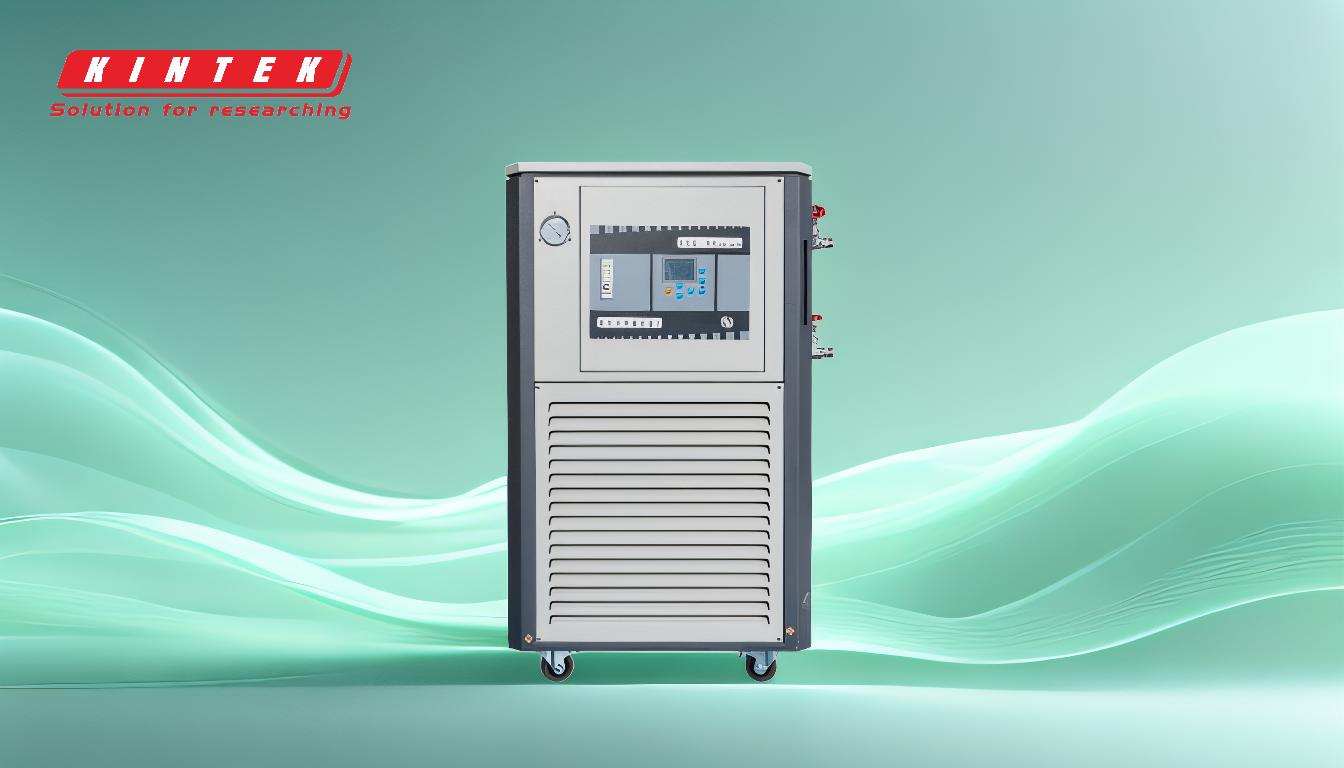
-
Understanding Induction Melting:
- Induction melting is a process where electromagnetic induction is used to heat and melt metals. An alternating magnetic field induces eddy currents within the metal, generating heat due to the metal's electrical resistance.
- This method is particularly effective for copper due to its high electrical conductivity, allowing for rapid and efficient heating.
-
Role of the Crucible:
- The crucible is a container made of refractory material that holds the copper during the melting process. It must withstand high temperatures and the corrosive nature of molten copper.
- The crucible is placed inside the induction furnace, where it is surrounded by the induction coil that generates the magnetic field.
-
Induction Furnace Components:
- Induction Coil: The coil is a critical component that generates the alternating magnetic field. It is typically made of copper tubing and is water-cooled to prevent overheating.
- Power Supply: The power supply, often utilizing IGBT (Insulated Gate Bipolar Transistor) technology, provides the high-frequency alternating current needed to create the magnetic field. IGBT-based power supplies are known for their efficiency and precise control.
- Control System: Modern induction furnaces are equipped with advanced control systems that allow for precise temperature regulation, ensuring optimal melting conditions for copper.
-
Melting Process:
- Heating: When the furnace is activated, the alternating magnetic field induces eddy currents in the copper, causing it to heat up rapidly. The heat is generated directly within the metal, leading to efficient and uniform melting.
- Melting: As the temperature rises, the copper transitions from a solid to a liquid state. The process is quick, often taking only a few minutes, depending on the amount of copper and the power of the furnace.
- Maintenance of Temperature: Once melted, the control system maintains the copper at the desired temperature, ready for the next steps in the process.
-
Post-Melting Processes:
- Smelting and Purifying: After melting, the copper may undergo additional smelting to remove impurities. This can involve adding fluxes or other materials to the molten copper to separate and remove unwanted elements.
- Casting: The purified molten copper is then poured into molds to create the desired shapes, such as ingots, billets, or custom castings. The precise temperature control of the induction furnace ensures high-quality castings with minimal defects.
-
Advantages of Induction Melting for Copper:
- Efficiency: Induction melting is highly energy-efficient, as the heat is generated directly within the metal, reducing energy losses.
- Precision: The ability to precisely control the temperature ensures consistent quality in the melted copper, which is crucial for applications requiring high purity or specific mechanical properties.
- Minimal Metal Loss: The process results in low metal loss, making it cost-effective, especially for high-value materials like copper.
- Environmental Benefits: Induction melting produces fewer emissions compared to traditional melting methods, contributing to a cleaner and safer working environment.
In summary, melting copper with induction involves using an induction furnace to generate heat through electromagnetic induction. The process is efficient, precise, and suitable for a wide range of applications, from custom castings to large-scale bronze structures. The use of advanced components like IGBT-based power supplies and precise control systems ensures optimal performance and high-quality results.
Summary Table:
Key Aspect | Details |
---|---|
Process | Electromagnetic induction heats copper via eddy currents, melting it rapidly. |
Crucible Role | Holds copper; made of refractory material to withstand high temperatures. |
Induction Furnace Components | Includes induction coil, IGBT-based power supply, and advanced control system. |
Advantages | High efficiency, precise temperature control, minimal metal loss, eco-friendly. |
Applications | Custom castings, large bronze structures, and high-purity copper products. |
Ready to optimize your copper melting process? Contact us today for expert guidance and solutions!