Melting metal in an induction furnace is a highly efficient and controlled process that leverages electromagnetic induction to generate heat within the metal itself. This method is widely used in industries for melting various metals, including gold, due to its precision, speed, and ability to preserve alloying elements. The process involves several key steps, from preparing the metal and crucible to adjusting the furnace settings and ensuring safety measures. Below is a detailed explanation of how to melt metal in an induction furnace, with a focus on the use of an IGBT induction furnace.
Key Points Explained:
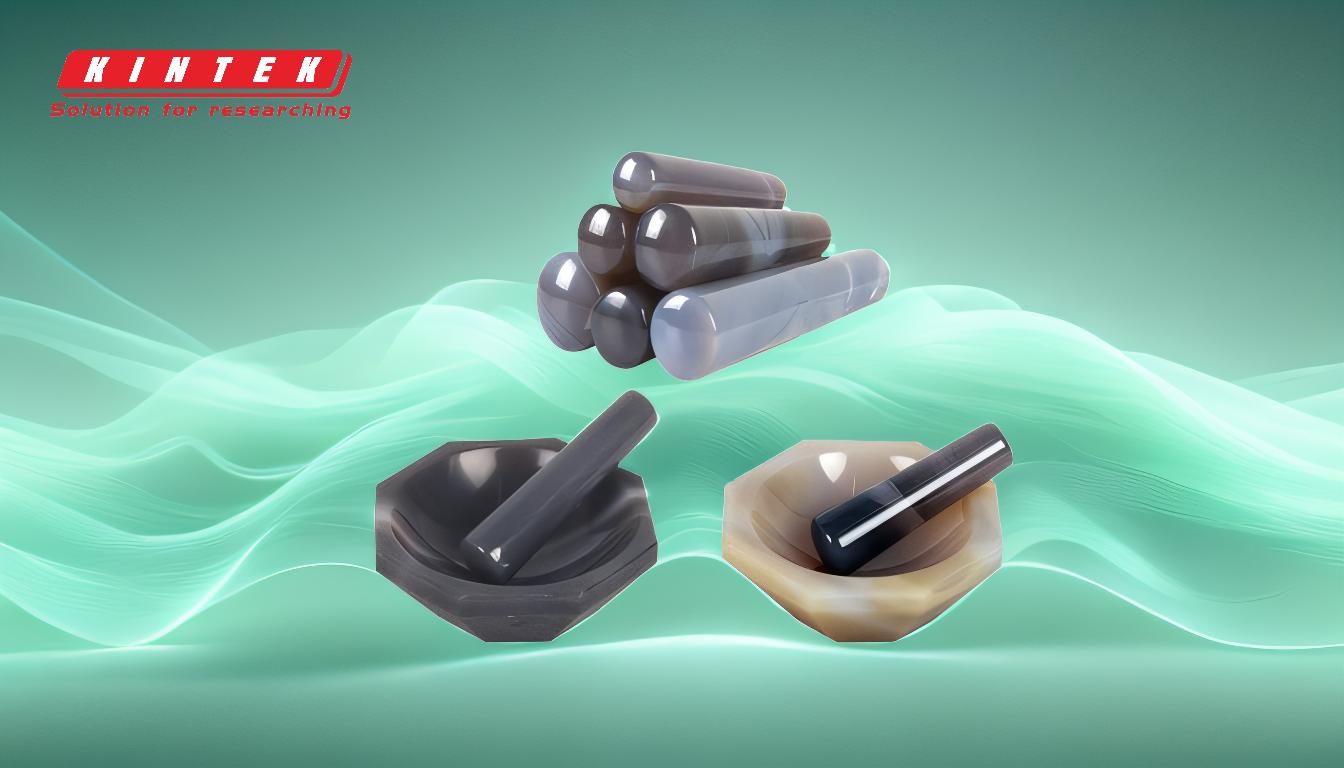
-
Understanding Induction Furnace Principles:
- Induction furnaces work by creating a magnetic field that induces eddy currents within the metal, generating heat through Joule heating. This method does not require combustion or an arc, making it safer and more energy-efficient.
- The furnace's temperature can be precisely controlled, ensuring that only the required melting temperature is reached. This prevents the loss of valuable alloying elements and improves the overall efficiency of the process.
-
Preparation of the Metal and Crucible:
- Choose a crucible made of materials like graphite carbon or clay that can withstand high temperatures and hold the metal securely.
- If melting gold or other precious metals, use flux (a mixture of borax and sodium carbonate) to remove impurities. This step ensures the purity of the molten metal.
-
Safety Measures:
- Always wear protective gear, including goggles, gloves, face shields, and an apron, to protect against splashes and heat.
- Ensure the melting area is free from flammable materials and is well-ventilated.
-
Loading the Furnace:
- Place the crucible containing the metal and flux into the induction furnace. The furnace's design, such as a rotatable turret in vacuum induction melting furnaces, can facilitate easy loading and unloading.
-
Adjusting Furnace Settings:
- Set the temperature and frequency of the furnace based on the type and amount of metal being melted. For gold, the melting point is approximately 1064°C.
- The IGBT induction furnace is particularly effective for this process due to its ability to provide precise control over temperature and frequency.
-
Melting Process:
- Once the furnace is activated, the magnetic field induces eddy currents in the metal, heating it until it melts. This process typically takes between 2 to 20 minutes, depending on the furnace's power and the metal's properties.
- A thermocouple can be used to monitor the temperature of the molten metal, ensuring it reaches the desired level.
-
Pouring and Forming:
- After the metal has completely melted, it can be poured into a mold or granulation tank using a tundish or ladle. Care must be taken to avoid spills or splashes.
- In vacuum induction melting furnaces, a turning mechanism is often used to pour the molten metal into forming molds, completing the smelting process.
-
Maintenance and Repair:
- Regular maintenance is essential to ensure the furnace operates efficiently. Depending on the extent of damage, repairs may involve scraping off slag, setting a die, and filling with quartz sand.
- For partial repairs, damaged areas can be fixed with a steel plate and filled with quartz sand, followed by compacting and heating the furnace.
By following these steps, you can effectively melt metal in an induction furnace, leveraging the advanced capabilities of an IGBT induction furnace to achieve precise and efficient results. This method is not only faster but also safer and more environmentally friendly compared to traditional melting techniques.
Summary Table:
Step | Key Details |
---|---|
1. Understanding Principles | Induction creates eddy currents, generating heat via Joule heating. No combustion required. |
2. Preparation | Use high-temperature crucibles (graphite/carbon) and flux for precious metals. |
3. Safety Measures | Wear protective gear and ensure a well-ventilated, flammable-free workspace. |
4. Loading the Furnace | Place crucible with metal and flux into the furnace. |
5. Adjusting Settings | Set temperature and frequency based on metal type (e.g., gold melts at 1064°C). |
6. Melting Process | Magnetic field heats metal; process takes 2-20 minutes. Monitor with thermocouple. |
7. Pouring and Forming | Pour molten metal into molds using tundish or ladle. |
8. Maintenance | Regular upkeep ensures efficiency; repair damaged areas with quartz sand. |
Ready to optimize your metal melting process? Contact us today to learn more about IGBT induction furnaces!