Starting a pyrolysis plant involves a series of well-defined steps, from initial planning and regulatory compliance to the actual setup and operation of the plant. The process requires careful consideration of feedstock availability, technology selection, and adherence to safety and environmental regulations. Below is a detailed guide on how to start a pyrolysis plant, broken down into key steps and considerations.
Key Points Explained:
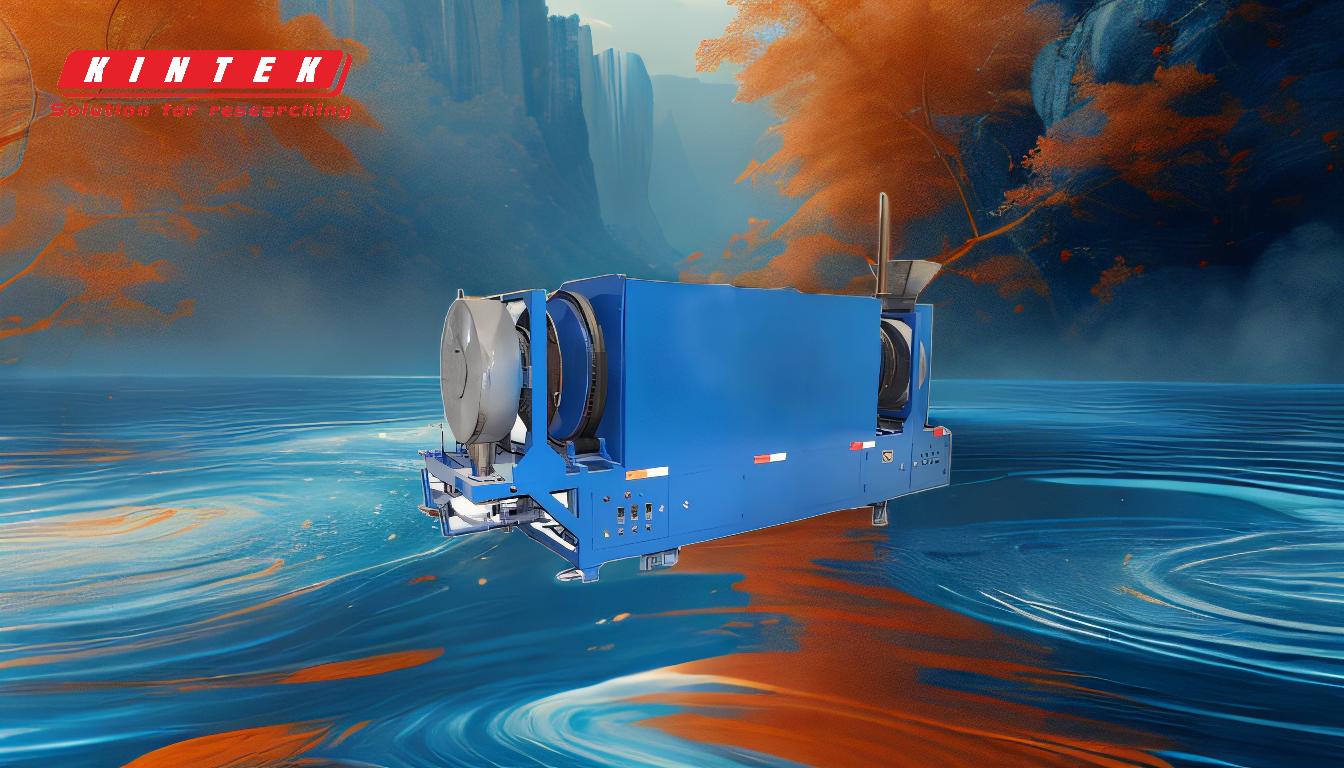
-
Feasibility Study and Planning:
- Feedstock Availability: Assess the availability and suitability of feedstock (e.g., plastic waste, biomass, tires) in your area. The type and quality of feedstock will influence the design and capacity of your pyrolysis plant.
- Market Analysis: Conduct a market analysis to understand the demand for the end products (e.g., bio-oil, bio-char, syngas) and potential revenue streams.
- Site Selection: Choose a location that is accessible to feedstock suppliers and product markets, and that complies with zoning and environmental regulations.
- Financial Planning: Prepare a detailed business plan, including capital investment, operational costs, and projected revenues. Consider potential funding sources and return on investment (ROI).
-
Regulatory Compliance and Permits:
- Environmental Regulations: Ensure that your plant complies with local, state, and federal environmental regulations. This may include air quality standards, waste disposal regulations, and emissions controls.
- Permits and Licenses: Obtain all necessary permits and licenses before starting construction. This may include environmental permits, building permits, and operational licenses.
- Safety Standards: Adhere to safety standards and regulations to protect workers and the surrounding community. This includes fire safety, chemical handling, and emergency response plans.
-
Technology and Equipment Selection:
- Pyrolysis Reactor: Choose a pyrolysis reactor that suits your feedstock and desired end products. Consider factors such as reactor type (e.g., fixed bed, fluidized bed), capacity, and heating method (e.g., direct or indirect heating).
- Preprocessing Equipment: Invest in equipment for feedstock preparation, such as shredders, dryers, and separators, to remove impurities and ensure optimal feedstock quality.
- Condensation and Separation Systems: Install systems for condensing and separating the pyrolysis products (e.g., bio-oil, syngas, bio-char). This may include condensers, cyclones, and quench systems.
- Control and Safety Systems: Implement control systems for monitoring and optimizing the pyrolysis process, as well as safety systems to prevent accidents and ensure safe operation.
-
Plant Design and Construction:
- Plant Layout: Design the plant layout to optimize workflow, minimize material handling, and ensure safety. Consider the placement of the reactor, preprocessing equipment, and product storage areas.
- Construction: Hire experienced contractors to build the plant according to the design specifications. Ensure that construction adheres to all relevant codes and standards.
- Infrastructure: Develop necessary infrastructure, such as access roads, utilities (e.g., water, electricity), and waste management systems.
-
Commissioning and Operation:
- Testing and Commissioning: Before full-scale operation, conduct thorough testing of all equipment and systems to ensure they function correctly. This may include trial runs with feedstock to optimize process parameters.
- Staff Training: Train operators and maintenance staff on the safe and efficient operation of the plant. This includes understanding the pyrolysis process, equipment maintenance, and emergency procedures.
- Startup: Begin operations with a gradual ramp-up to full capacity. Monitor the process closely and make adjustments as needed to optimize performance and product quality.
-
Maintenance and Optimization:
- Routine Maintenance: Establish a maintenance schedule to keep the plant running smoothly. This includes regular inspections, cleaning, and replacement of worn parts.
- Process Optimization: Continuously monitor and optimize the pyrolysis process to improve efficiency, product quality, and profitability. This may involve adjusting temperature, residence time, and feedstock composition.
- Environmental Monitoring: Regularly monitor emissions and waste products to ensure compliance with environmental regulations. Implement measures to minimize environmental impact, such as recycling waste heat or using scrubbers to reduce emissions.
-
Product Handling and Distribution:
- Product Storage: Store the end products (e.g., bio-oil, bio-char, syngas) in appropriate facilities to maintain quality and prevent contamination.
- Distribution: Develop a distribution network to transport products to customers or markets. This may include partnerships with fuel distributors, agricultural suppliers, or industrial users.
- Quality Control: Implement quality control measures to ensure that the products meet customer specifications and industry standards.
By following these steps, you can successfully start and operate a pyrolysis plant, converting waste materials into valuable products while adhering to regulatory and safety standards.
Summary Table:
Step | Key Considerations |
---|---|
Feasibility Study | Assess feedstock availability, market demand, site selection, and financial planning. |
Regulatory Compliance | Obtain permits, adhere to environmental and safety standards. |
Technology Selection | Choose pyrolysis reactor, preprocessing, and condensation systems. |
Plant Design & Construction | Design layout, hire contractors, and develop infrastructure. |
Commissioning & Operation | Test equipment, train staff, and start operations gradually. |
Maintenance & Optimization | Schedule maintenance, optimize processes, and monitor environmental impact. |
Product Handling | Store, distribute, and ensure quality control of end products. |
Ready to start your pyrolysis plant? Contact us today for expert guidance and support!