Physical Vapor Deposition (PVD) is a sophisticated technology used to deposit thin films of material onto various substrates. The process involves the transformation of a solid material into a vapor phase in a high vacuum environment, which then condenses to form a thin film on the substrate. This method is widely used in industries for coating applications to enhance surface properties such as hardness, wear resistance, and corrosion resistance. Below is a detailed explanation of how a PVD machine operates, focusing on its key components and the process flow.
Key Points Explained:
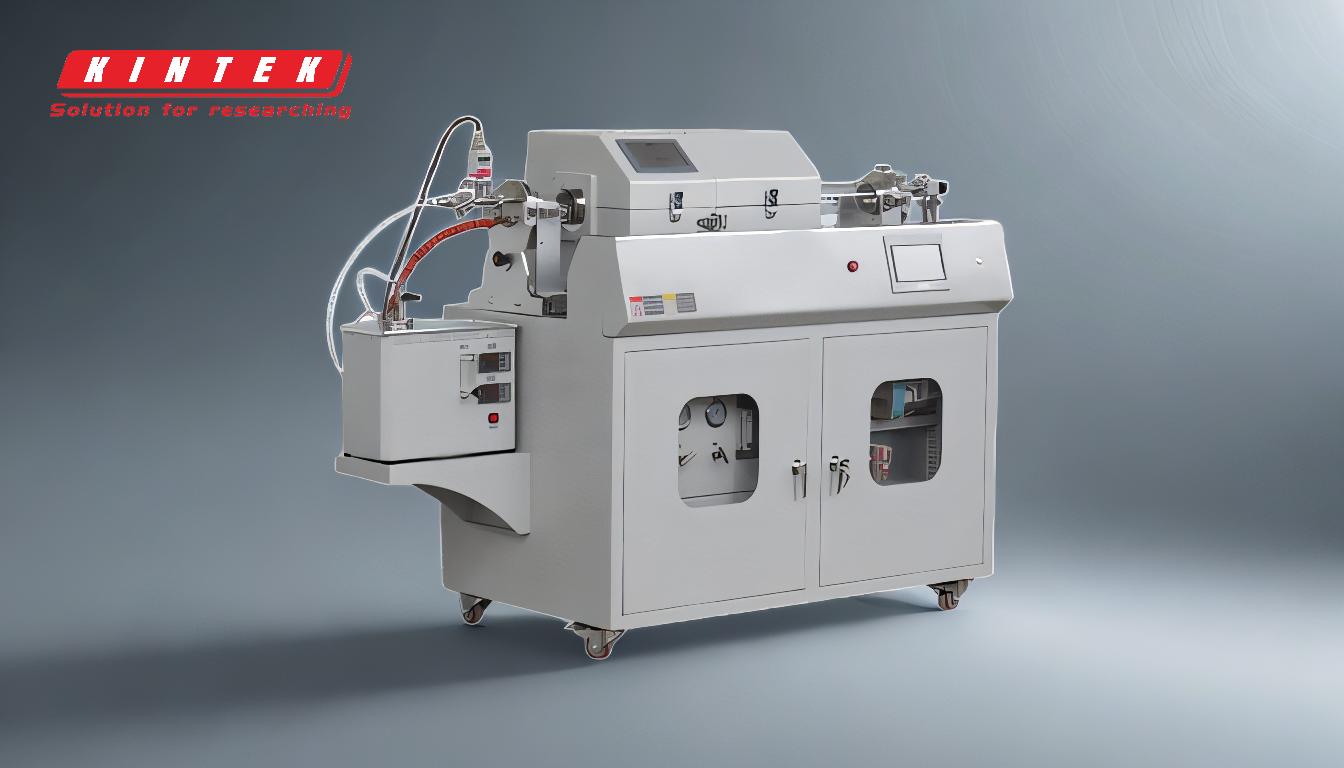
-
High Vacuum Environment:
- The PVD process takes place in a high vacuum chamber to minimize contamination and ensure a pure deposition environment.
- The vacuum level is typically maintained at pressures ranging from 10^-3 to 10^-6 Torr, which helps in achieving a clean and controlled deposition process.
-
Heat Source and Vaporization:
- A heat source, often an electron beam or resistive heating, is used to vaporize the solid target material.
- The target material is heated to temperatures between 250 to 350 degrees Celsius, causing it to transition from a solid to a vapor state.
- This vaporization process generates a vapor stream that is directed towards the substrate.
-
Vapor Stream and Deposition:
- The vaporized material forms a stream that travels through the vacuum chamber and deposits onto the substrate surface.
- The substrate is typically positioned opposite the target material to ensure uniform coating.
- The deposition process results in the formation of a thin film, which can range from a few nanometers to several micrometers in thickness.
-
Types of PVD Techniques:
- Evaporation: Involves heating the target material until it evaporates and then condenses on the substrate.
- Sputtering: Uses energetic ions to bombard the target material, ejecting atoms that then deposit onto the substrate.
- Arc Vapor Deposition: Utilizes an electric arc to vaporize the target material, which is then deposited onto the substrate.
-
Applications of PVD:
- PVD is extensively used in the manufacturing of semiconductors, optical coatings, and decorative finishes.
- It is also employed in the production of cutting tools, medical devices, and aerospace components to enhance their durability and performance.
-
Advantages of PVD:
- High Purity: The vacuum environment ensures minimal contamination, leading to high-purity coatings.
- Versatility: PVD can be used to deposit a wide range of materials, including metals, ceramics, and composites.
- Durability: PVD coatings are known for their excellent adhesion, hardness, and wear resistance.
-
Comparison with Chemical Vapor Deposition (CVD):
- Unlike PVD, which uses physical means to vaporize the material, chemical vapor deposition machine involves chemical reactions to deposit thin films.
- CVD typically operates at higher temperatures and can produce thicker and more uniform coatings compared to PVD.
In summary, a PVD machine operates by creating a high vacuum environment, vaporizing a solid target material using a heat source, and depositing the resulting vapor onto a substrate to form a thin film. This process is highly versatile and offers numerous advantages, making it a preferred choice for various industrial applications.
Summary Table:
Key Aspect | Details |
---|---|
High Vacuum Environment | Maintains pressures of 10^-3 to 10^-6 Torr for contamination-free deposition. |
Heat Source | Electron beam or resistive heating vaporizes target material (250-350°C). |
Vapor Stream | Vaporized material deposits onto substrates, forming thin films. |
PVD Techniques | Evaporation, sputtering, and arc vapor deposition. |
Applications | Semiconductors, optical coatings, cutting tools, and aerospace components. |
Advantages | High purity, versatility, and durable coatings with excellent adhesion. |
Discover how PVD technology can enhance your applications—contact our experts today!