A temperature controller is a device designed to regulate the temperature of a system by comparing a sensor signal (typically from a thermocouple) with a predefined set point. It converts the millivolt signal from the thermocouple into a temperature reading and uses computer logic and hardware to adjust heating or cooling mechanisms accordingly. The controller ensures the system follows a programmed heating cycle, maintaining precise temperature control. Proper calibration is essential to ensure accuracy, as electronics can degrade over time, leading to significant temperature misreporting if not serviced.
Key Points Explained:
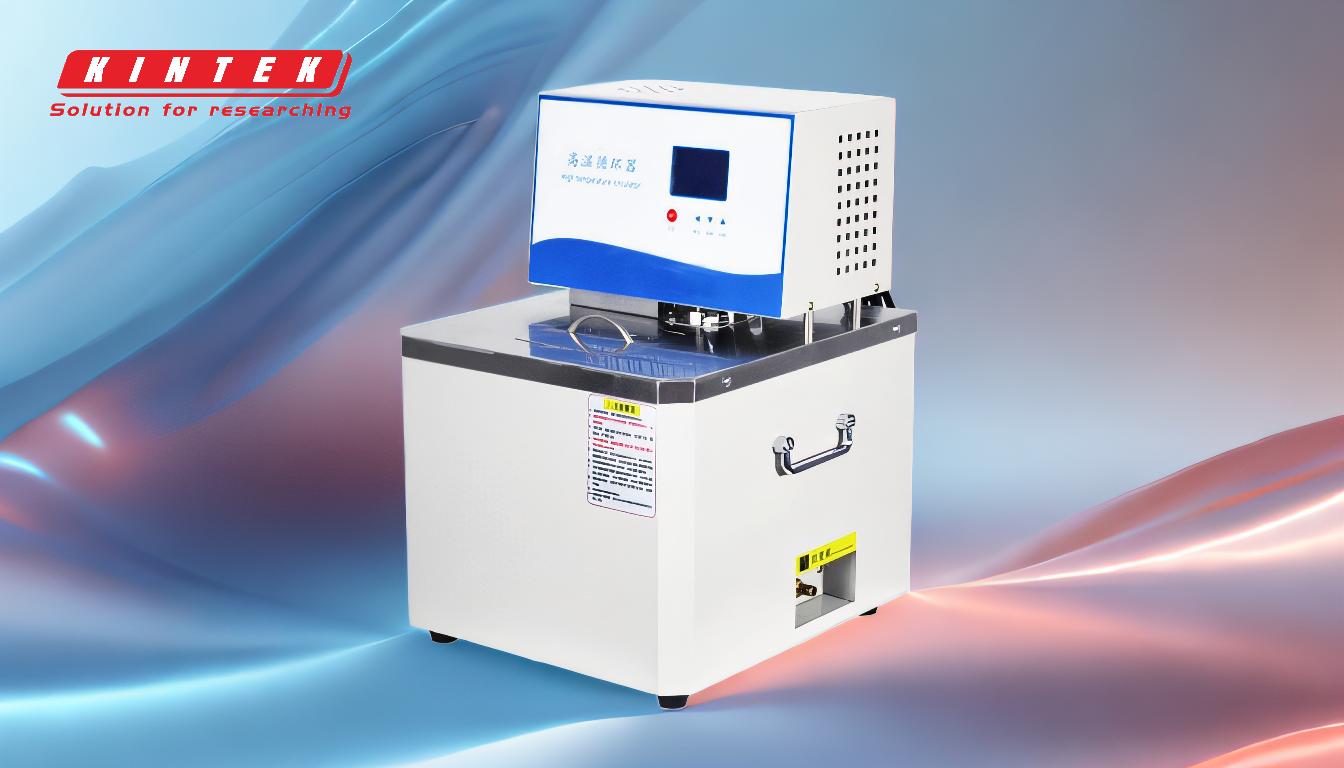
-
Basic Functionality of a Temperature Controller:
- A temperature controller acts as a voltmeter, converting millivolt signals from a thermocouple into temperature readings.
- It compares the sensor signal with a set point (desired temperature) to determine the deviation.
- Based on this deviation, the controller adjusts heating or cooling mechanisms to maintain the desired temperature.
-
Role of Thermocouples:
- Thermocouples are sensors that generate a millivolt signal proportional to the temperature they measure.
- This signal is fed into the temperature controller, which processes it to determine the current system temperature.
-
Computer Logic and Hardware:
- The controller includes built-in computer logic to perform calculations and make decisions based on the deviation between the sensor signal and the set point.
- It uses hardware components to activate heating or cooling systems, such as furnaces or cooling fans, to adjust the temperature.
-
Programmed Heating Cycles:
- Temperature controllers can be programmed with specific heating or cooling cycles to achieve precise temperature profiles over time.
- This is particularly useful in industrial processes where temperature control is critical for product quality.
-
Importance of Calibration:
- Proper calibration is essential to ensure the accuracy of the temperature controller.
- Over time, electronic components can degrade, leading to errors in temperature reporting (up to 50°C if not serviced).
- Regular maintenance and calibration help maintain the controller's accuracy and reliability.
-
Applications of Temperature Controllers:
- Temperature controllers are used in various applications, including industrial furnaces, HVAC systems, and laboratory equipment.
- They are critical in processes where maintaining a specific temperature is vital for safety, efficiency, or product quality.
-
Types of Temperature Controllers:
- On/Off Controllers: The simplest type, which turns the heating or cooling system on or off based on the temperature deviation.
- Proportional Controllers: Adjust the power supplied to the heating or cooling system proportionally to the temperature deviation.
- PID Controllers: Use Proportional, Integral, and Derivative control to provide precise and stable temperature regulation.
By understanding these key points, equipment and consumable purchasers can make informed decisions about selecting and maintaining temperature controllers for their specific needs.
Summary Table:
Key Aspect | Description |
---|---|
Basic Functionality | Converts thermocouple signals to temperature readings and adjusts heating/cooling. |
Role of Thermocouples | Generates millivolt signals proportional to temperature for the controller. |
Computer Logic & Hardware | Uses logic and hardware to adjust systems based on temperature deviations. |
Programmed Heating Cycles | Enables precise temperature profiles for industrial processes. |
Importance of Calibration | Ensures accuracy; degradation can cause errors up to 50°C if not serviced. |
Applications | Used in industrial furnaces, HVAC systems, and laboratory equipment. |
Types of Controllers | On/Off, Proportional, and PID controllers for varying levels of precision. |
Ensure precise temperature control for your systems—contact our experts today to find the right solution!