A tilting furnace, often referred to as a rotating furnace, operates by utilizing a tilting mechanism to pour molten metal or other materials from the furnace chamber. This type of furnace is commonly used in foundries and metalworking industries for melting and casting processes. The furnace is designed with a robust structure that allows it to tilt or rotate, enabling precise control over the pouring of molten material. The heating mechanism can vary, but it typically involves electric heating elements or gas burners to achieve the required temperatures. The tilting action is usually powered by hydraulic or mechanical systems, ensuring smooth and controlled movement. This design facilitates efficient material handling, reduces manual labor, and enhances safety during operation.
Key Points Explained:
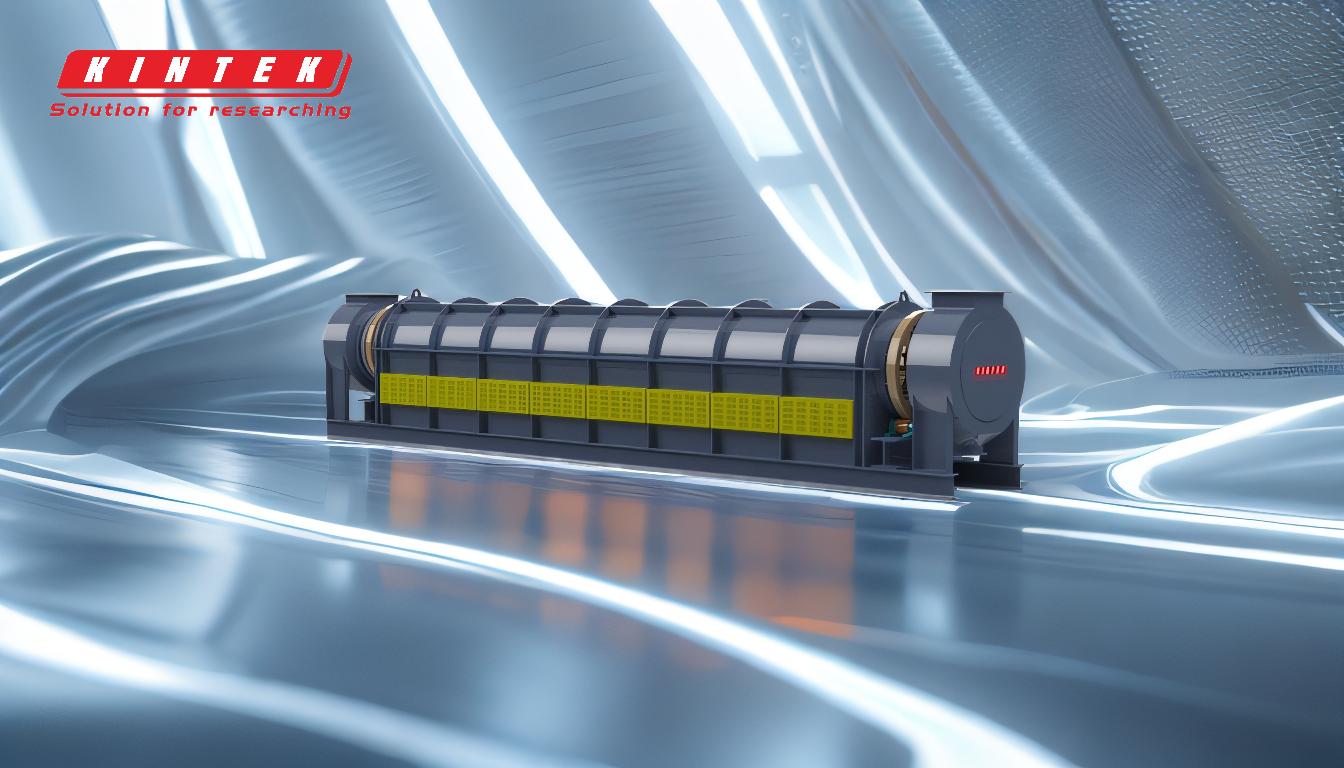
-
Tilting Mechanism:
- The core feature of a tilting furnace is its ability to tilt or rotate. This mechanism is crucial for pouring molten materials, such as metal, into molds or other containers.
- The tilting action is typically powered by hydraulic systems, which provide the necessary force and control for smooth operation. Mechanical systems, such as gears and levers, are also used in some designs.
- This mechanism allows for precise control over the pouring process, reducing spillage and ensuring accurate placement of the molten material.
-
Heating System:
- Tilting furnaces can use various heating methods, including electric heating elements or gas burners. The choice of heating system depends on the specific application and the type of material being melted.
- Electric heating elements generate heat through electrical resistance, converting electrical energy into thermal energy. This method is often used for smaller furnaces or in applications requiring precise temperature control.
- Gas burners, on the other hand, use combustion to produce heat. This method is typically used in larger furnaces or when higher temperatures are required.
-
Furnace Structure:
- The furnace is constructed with a robust frame to support the weight of the molten material and withstand the high temperatures involved in the melting process.
- The interior of the furnace is lined with refractory materials, which are designed to resist extreme heat and prevent heat loss. This lining also protects the furnace structure from thermal damage.
- The tilting mechanism is integrated into the furnace structure, allowing the entire furnace to tilt or rotate as needed.
-
Applications:
- Tilting furnaces are widely used in foundries for melting and casting metals such as iron, steel, aluminum, and copper. They are also used in the glass industry for melting and shaping glass.
- The ability to tilt the furnace makes it particularly suitable for processes that require precise pouring, such as casting intricate shapes or filling molds with molten material.
- In addition to metal and glass, tilting furnaces can be used for melting other materials, such as ceramics and certain types of plastics.
-
Advantages:
- Efficiency: The tilting mechanism allows for efficient pouring, reducing the need for manual handling and minimizing material waste.
- Safety: By automating the pouring process, tilting furnaces reduce the risk of accidents and injuries associated with handling molten materials.
- Precision: The controlled tilting action ensures accurate pouring, which is essential for producing high-quality castings and other products.
- Versatility: Tilting furnaces can be used for a wide range of materials and applications, making them a versatile tool in various industries.
-
Operation:
- The operation of a tilting furnace begins with loading the raw material into the furnace chamber. The material is then heated to the required temperature using the chosen heating method.
- Once the material has reached the desired temperature, the tilting mechanism is activated. The furnace tilts, allowing the molten material to flow out of the chamber and into the mold or container.
- After pouring, the furnace is returned to its original position, and the process can be repeated as needed.
-
Maintenance:
- Regular maintenance is essential to ensure the efficient and safe operation of a tilting furnace. This includes inspecting and replacing refractory linings, checking the tilting mechanism for wear and tear, and maintaining the heating system.
- Proper maintenance helps to extend the lifespan of the furnace and prevent costly downtime due to equipment failure.
In summary, a tilting furnace, or rotating furnace, is a versatile and efficient tool used in various industries for melting and pouring materials. Its unique tilting mechanism allows for precise control over the pouring process, enhancing safety and productivity. The furnace's robust structure, combined with its efficient heating system, makes it an essential piece of equipment in foundries and other industrial settings.
Summary Table:
Feature | Description |
---|---|
Tilting Mechanism | Powered by hydraulic or mechanical systems for precise pouring of molten materials. |
Heating System | Uses electric heating elements or gas burners for efficient temperature control. |
Furnace Structure | Robust design with refractory lining to withstand high temperatures and heat loss. |
Applications | Used in foundries, metalworking, and glass industries for melting and casting. |
Advantages | Enhances efficiency, safety, precision, and versatility in material handling. |
Operation | Load material, heat, tilt to pour, and return to original position for reuse. |
Maintenance | Regular checks on refractory linings, tilting mechanisms, and heating systems. |
Interested in integrating a tilting furnace into your operations? Contact us today for expert advice and solutions!