A tube furnace operates by generating high temperatures within a cylindrical cavity, typically used for heating small samples, sintering, and various thermal processes. It consists of heating coils embedded in a thermally insulating matrix, a working tube (often made of quartz or alumina), and a temperature control system using a thermocouple. The furnace can create controlled environments, such as vacuum or gas atmospheres, to protect or chemically treat samples. Its design ensures efficient heat distribution, sample integrity, and precise temperature regulation, making it a versatile tool in laboratories and industrial settings.
Key Points Explained:
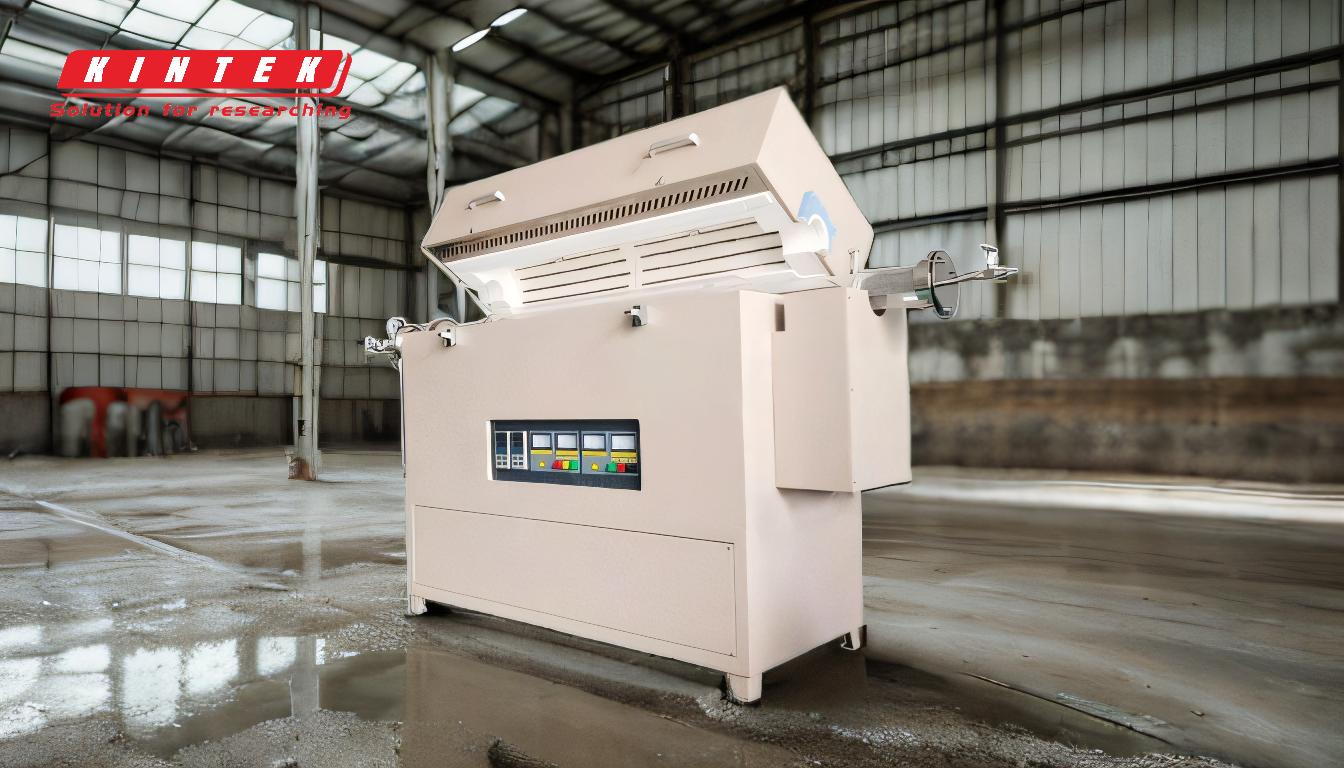
-
Basic Structure of a Tube Furnace:
- A tube furnace typically includes a cylindrical cavity surrounded by heating coils embedded in a thermally insulating matrix. This design ensures efficient heat retention and uniform temperature distribution.
- The working tube, often made of quartz or alumina, is placed inside the furnace to hold the sample. This tube can withstand high temperatures and chemical reactions, ensuring sample integrity.
- The furnace body is usually constructed with an alumina ceramic fiber heating chamber and a heavy-duty outer shell for durability and safety.
-
Heating Mechanism:
- The furnace generates high temperatures using medium-frequency induction heating or resistive heating elements. These elements heat the working tube and the sample through thermal radiation.
- The heating coils are strategically placed to ensure uniform heat distribution along the length of the tube, which is crucial for consistent results in experiments or processes.
-
Temperature Control:
- Temperature regulation is achieved using a thermocouple, which provides real-time feedback to the furnace's control system. This allows for precise temperature adjustments and maintenance of desired conditions.
- Advanced models may include programmable controllers for automated temperature profiles, enabling complex heating cycles.
-
Working Tube Functions:
- The working tube serves multiple purposes: it maintains the furnace interior, protects the sample from contamination, and prevents chemical reactions that could damage the furnace insulation.
- It also allows for the creation of controlled atmospheres, such as vacuum, inert gas, or reactive gas environments, depending on the application.
-
Applications and Versatility:
- Tube furnaces are ideal for heating small samples, sintering, and performing thermal treatments in laboratories, universities, and industrial settings.
- They are commonly used for processes like oxidation, reduction, annealing, and chemical vapor deposition (CVD).
- The ability to create specific atmospheric conditions makes them suitable for a wide range of materials, including metals, ceramics, and composites.
-
Additional Features:
- Many tube furnaces come equipped with a sealing flange at the end of the working tube, which can be used to create a vacuum or introduce gases.
- Some models include a vacuum pump and fittings for enhanced control over the internal environment.
- The furnace may also feature hinges for easy access to the working tube and sample.
-
Comparison with Other Furnace Types:
- Unlike a pusher furnace, which operates continuously by moving samples through a series of boats, a tube furnace is typically used for batch processing.
- Compared to a rotary furnace, which rotates materials around a central axis, a tube furnace provides a more controlled and static environment for heating.
By understanding these key points, a purchaser can evaluate whether a tube furnace meets their specific needs, considering factors like temperature range, sample size, and required atmospheric conditions.
Summary Table:
Feature | Description |
---|---|
Basic Structure | Cylindrical cavity with heating coils and a thermally insulating matrix. |
Heating Mechanism | Uses medium-frequency induction or resistive heating for uniform heat distribution. |
Temperature Control | Thermocouple-based system with programmable controllers for precise regulation. |
Working Tube | Made of quartz or alumina; withstands high temps and chemical reactions. |
Applications | Sintering, oxidation, reduction, annealing, and chemical vapor deposition (CVD). |
Additional Features | Sealing flange, vacuum pump, and hinges for easy access. |
Ready to find the perfect tube furnace for your needs? Contact our experts today for personalized advice!