A vacuum heat treat furnace is a specialized piece of equipment used to heat treat materials, particularly metals, in a controlled, oxygen-free environment. This process ensures enhanced material properties such as improved hardness, strength, and corrosion resistance. The furnace operates by removing air from the chamber using a vacuum system, heating the material to precise temperatures, and then cooling it under controlled conditions. Key components include the vacuum system, heating elements, cooling systems, and a control system. The vacuum environment prevents oxidation and contamination, leading to superior material quality and repeatable results.
Key Points Explained:
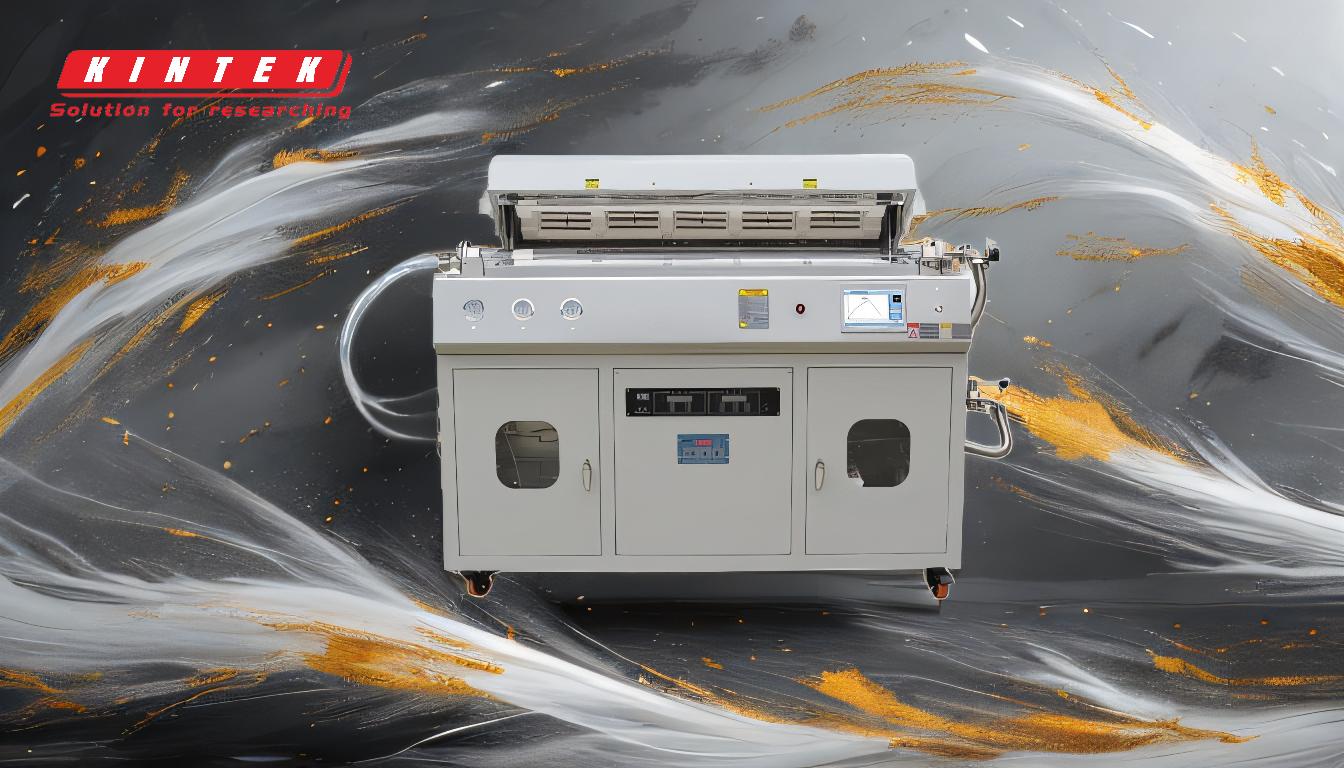
-
Vacuum System:
- The vacuum system is the core of the furnace, responsible for creating and maintaining a vacuum environment. It typically includes vacuum pumps, valves, measuring instruments, and pipelines.
- The vacuum pump removes air and gases from the chamber, ensuring no oxidation or contamination occurs during the heat treatment process.
- Components like the diffusion pump and vacuum valves work together to maintain the desired vacuum level, which is critical for achieving consistent results.
-
Heating Process:
- Once the vacuum is established, the heating elements are activated. These elements, often made of graphite or molybdenum, generate the required high temperatures.
- The temperature control system regulates the heating speed and holding time, ensuring precise thermal treatment of the materials.
- Heating in a vacuum environment allows for uniform temperature distribution, which is essential for achieving consistent material properties.
-
Cooling System:
- After the heating cycle, the cooling system is used to bring the materials back to room temperature in a controlled manner.
- Cooling methods may include gas quenching, oil quenching, or natural cooling, depending on the material and desired properties.
- The cooling process is carefully managed to prevent thermal shock and ensure the material achieves the desired hardness and microstructure.
-
Control System:
- The control system is the brain of the vacuum heat treat furnace, ensuring all processes are carried out with precision and repeatability.
- Modern furnaces are often computer-controlled, allowing for programmable heating and cooling cycles, real-time monitoring, and data logging.
- This automation ensures uniformity across batches and minimizes human error, making the process highly reliable.
-
Batch Processing:
- Vacuum heat treat furnaces operate as batch furnaces, processing one batch of parts at a time.
- Parts are loaded into the chamber, the door is sealed, and the vacuum is created. After the heat treatment cycle, the parts are cooled, unloaded, and the process repeats for the next batch.
- This method is ideal for high-precision applications where consistency and quality are paramount.
-
Advantages of Vacuum Heat Treatment:
- Oxidation Prevention: The absence of oxygen prevents oxidation, resulting in cleaner and brighter surfaces on the treated materials.
- Contamination-Free: The vacuum environment eliminates the risk of contamination from external gases or particles.
- Enhanced Material Properties: Vacuum heat treatment improves hardness, strength, and corrosion resistance, making it suitable for high-performance applications.
- Repeatability: The controlled environment and automated processes ensure consistent results across multiple batches.
-
Applications:
- Vacuum heat treat furnaces are widely used in industries such as aerospace, automotive, tool manufacturing, and medical devices.
- They are particularly effective for treating materials like titanium, stainless steel, and superalloys, which require precise thermal processing to achieve optimal properties.
By understanding these key points, a purchaser can better evaluate the capabilities and suitability of a vacuum heat treat furnace for their specific needs. The combination of advanced vacuum technology, precise temperature control, and automated systems makes this equipment indispensable for high-quality heat treatment processes.
Summary Table:
Component | Function |
---|---|
Vacuum System | Removes air and gases to prevent oxidation and contamination. |
Heating Elements | Generates precise high temperatures for uniform heat distribution. |
Cooling System | Controls cooling to prevent thermal shock and achieve desired properties. |
Control System | Automates heating and cooling cycles for repeatable, high-quality results. |
Batch Processing | Processes one batch at a time for consistency in high-precision applications. |
Discover how a vacuum heat treat furnace can enhance your material properties—contact our experts today!