Chemical vapor deposition (CVD) is a versatile and widely used technique for synthesizing carbon nanotubes (CNTs) and other nanomaterials. The process involves the decomposition of gaseous precursors on a heated substrate, leading to the formation of solid carbon nanotubes. The key steps include the transport of gaseous reactants to the substrate, their adsorption, surface reactions, diffusion to growth sites, nucleation, and the eventual desorption of by-products. This method is highly controllable and scalable, making it ideal for producing high-quality CNTs with specific properties. Below, we break down the process and its significance in carbon nanotube synthesis.
Key Points Explained:
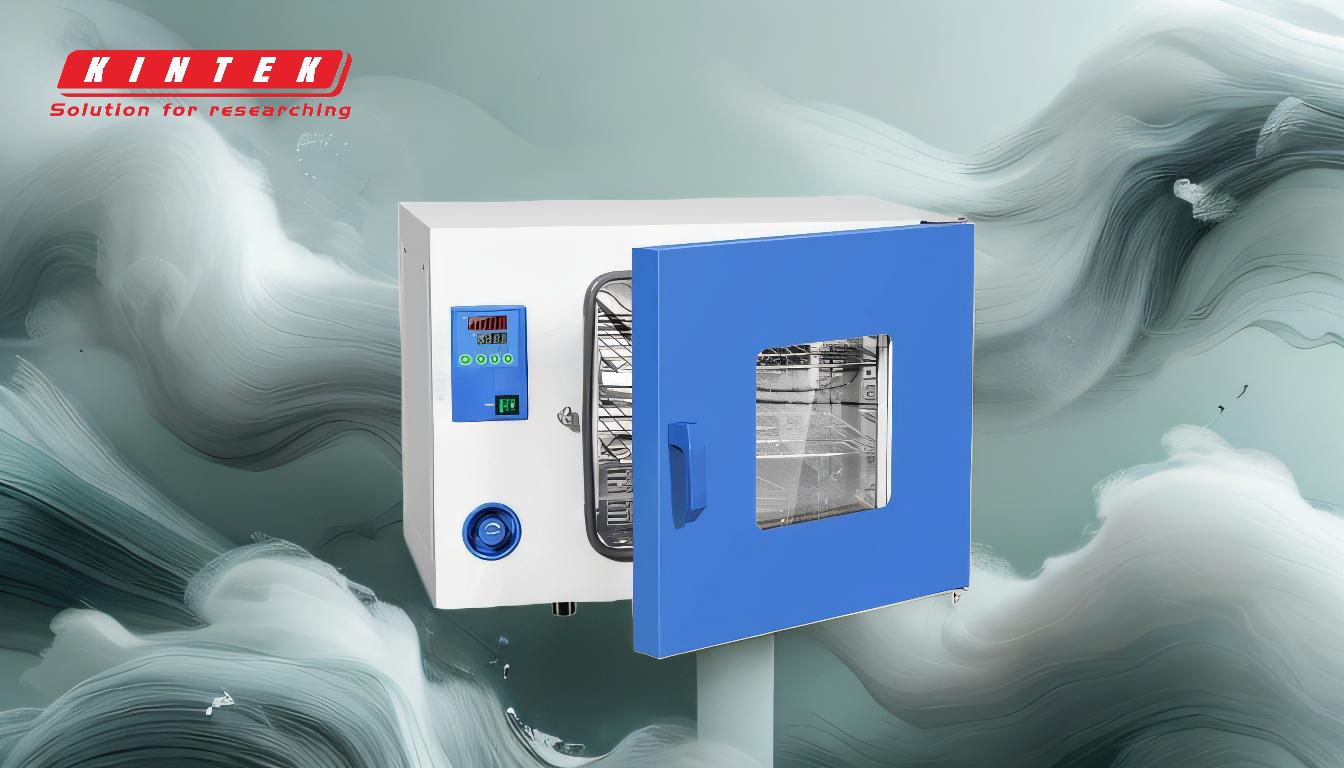
-
Introduction to Chemical Vapor Deposition (CVD):
- Chemical vapor deposition is a process where gaseous reactants are introduced into a reaction chamber and decompose on a heated substrate to form a solid material.
- This technique is particularly effective for synthesizing carbon nanotubes due to its ability to control growth conditions, such as temperature, pressure, and gas flow rates.
-
Steps Involved in CVD for Carbon Nanotube Synthesis:
- Transport of Gaseous Species: The precursor gases (e.g., methane, ethylene, or acetylene) are introduced into the reaction chamber and transported to the substrate surface.
- Adsorption on the Substrate: The gas molecules adsorb onto the heated substrate, which is often coated with a catalyst (e.g., iron, cobalt, or nickel nanoparticles).
- Surface-Catalyzed Reactions: The adsorbed gas molecules decompose on the catalyst surface, releasing carbon atoms that diffuse into the catalyst particles.
- Nucleation and Growth: Carbon atoms precipitate out of the catalyst particles, forming carbon nanotubes. The growth direction and structure of the nanotubes are influenced by the catalyst and growth conditions.
- Desorption of By-products: Gaseous by-products, such as hydrogen, are desorbed from the surface and removed from the reaction chamber.
-
Role of Catalysts in CVD:
- Catalysts play a critical role in controlling the diameter, length, and chirality of carbon nanotubes. The size and distribution of catalyst nanoparticles determine the growth characteristics of the nanotubes.
- Common catalysts include transition metals like iron, cobalt, and nickel, which are deposited on substrates such as silicon or quartz.
-
Types of CVD for Carbon Nanotube Synthesis:
- Thermal CVD: The substrate is heated to high temperatures (600–1200°C) to facilitate the decomposition of precursor gases.
- Plasma-Enhanced CVD (PECVD): A plasma is used to lower the reaction temperature, enabling growth on temperature-sensitive substrates.
- Catalytic CVD (CCVD): A combination of thermal energy and catalysts is used to enhance the growth efficiency and control the nanotube structure.
-
Applications of CVD-Grown Carbon Nanotubes:
- Carbon nanotubes synthesized via CVD are used in a wide range of applications, including electronics (transistors, sensors), energy storage (batteries, supercapacitors), and composite materials (strong and lightweight materials).
- The ability to produce high-quality, aligned, or patterned nanotubes makes CVD a preferred method for industrial and research applications.
-
Advantages of CVD for Carbon Nanotube Synthesis:
- Scalability: CVD can be scaled up for mass production of carbon nanotubes.
- Control Over Properties: Parameters like temperature, pressure, and gas composition can be adjusted to tailor the properties of the nanotubes.
- Versatility: CVD can be used to grow nanotubes on various substrates and in different configurations (e.g., aligned, random, or patterned).
-
Challenges and Future Directions:
- Uniformity: Achieving uniform nanotube growth over large areas remains a challenge.
- Cost: The high energy consumption and cost of precursor gases can limit the economic feasibility of CVD.
- Environmental Impact: Developing greener precursors and optimizing energy usage are areas of ongoing research.
In summary, chemical vapor deposition is a powerful and adaptable method for synthesizing carbon nanotubes. Its ability to precisely control growth conditions and produce high-quality materials makes it indispensable in nanotechnology and materials science. As research continues, advancements in CVD techniques are expected to further enhance the efficiency, scalability, and sustainability of carbon nanotube production.
Summary Table:
Key Aspect | Description |
---|---|
Process Overview | Decomposition of gaseous precursors on a heated substrate to form carbon nanotubes. |
Key Steps | Transport, adsorption, surface reactions, nucleation, growth, and desorption. |
Role of Catalysts | Control diameter, length, and chirality of nanotubes (e.g., iron, cobalt, nickel). |
Types of CVD | Thermal CVD, Plasma-Enhanced CVD (PECVD), Catalytic CVD (CCVD). |
Applications | Electronics, energy storage, composite materials. |
Advantages | Scalability, precise control over properties, versatility. |
Challenges | Uniformity, cost, environmental impact. |
Discover how CVD can revolutionize your nanotube production—contact our experts today!