Electron-beam (e-beam) deposition is a sophisticated thin film deposition technique widely used in industries and research for creating high-quality, precise thin films. It operates under vacuum conditions, where a focused electron beam is used to heat and vaporize a target material, which then condenses onto a substrate to form a thin film. This method is particularly valued for its ability to deposit materials with high melting points and for producing films with excellent purity and uniformity. Below, we break down the process and its key aspects in detail.
Key Points Explained:
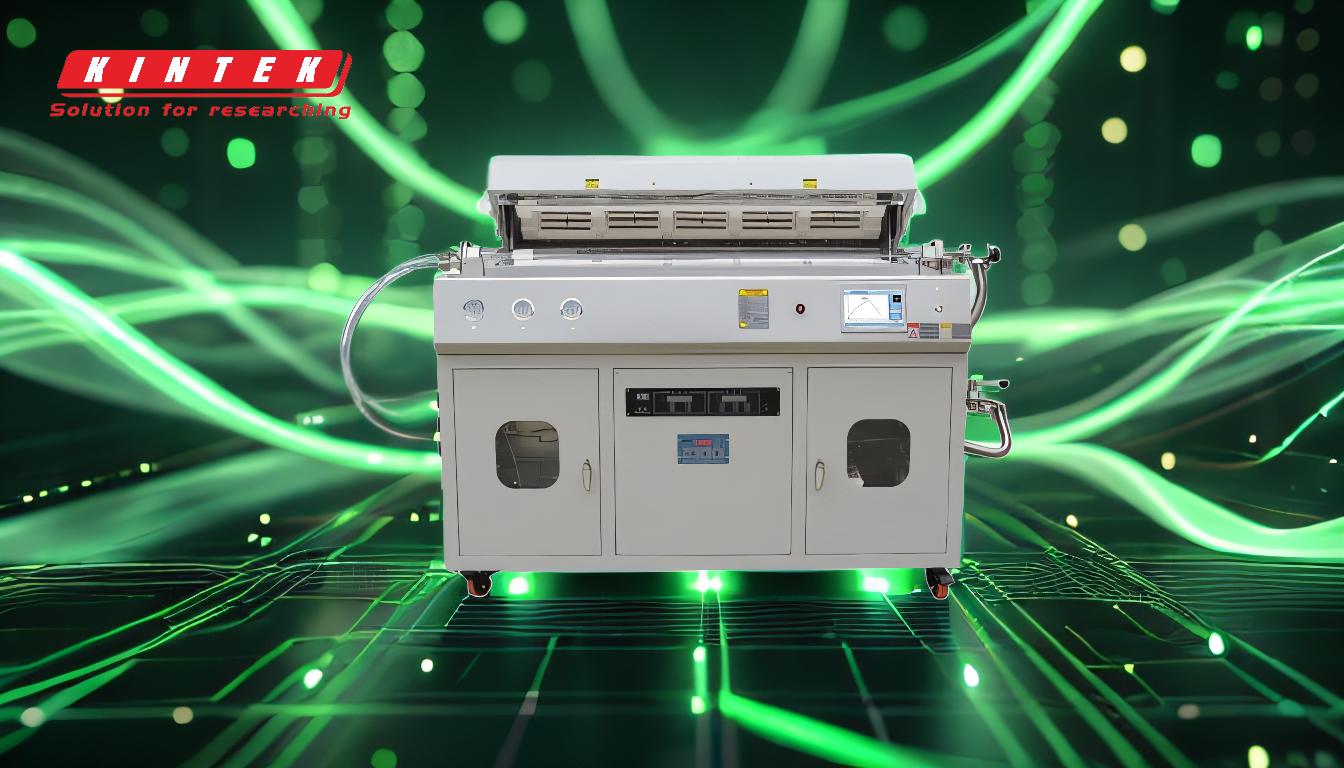
-
Vacuum Environment:
- E-beam deposition requires a high-vacuum environment to ensure minimal contamination and to allow the electron beam to travel unimpeded. This vacuum is typically maintained at pressures around 10^-6 Torr or lower.
- The vacuum environment also prevents oxidation and other chemical reactions that could degrade the quality of the deposited film.
-
Electron Beam Generation:
- A high-energy electron beam is generated using an electron gun, which typically consists of a heated filament (cathode) that emits electrons when heated.
- These electrons are then accelerated towards the target material by applying a high voltage, often in the range of several kilovolts.
-
Target Heating and Vaporization:
- The focused electron beam strikes the target material, transferring its kinetic energy and causing localized heating. This heating is intense enough to vaporize the target material.
- The target material is often placed in a crucible, which can be rotated or moved to ensure uniform erosion and deposition.
-
Deposition onto Substrate:
- The vaporized material travels through the vacuum and condenses onto a substrate positioned above the target. The substrate is usually held at a controlled temperature to influence the film's microstructure and properties.
- The deposition rate and thickness of the film can be precisely controlled by adjusting the electron beam current, the duration of deposition, and the distance between the target and the substrate.
-
Film Properties and Post-Deposition Treatments:
- After deposition, the thin film may undergo additional treatments such as annealing to improve its structural and electrical properties.
- The film's properties, such as thickness, uniformity, and adhesion, are then analyzed using various characterization techniques like X-ray diffraction (XRD), scanning electron microscopy (SEM), and atomic force microscopy (AFM).
-
Advantages of E-Beam Deposition:
- High Purity: The vacuum environment and precise control over the deposition process result in films with minimal impurities.
- Versatility: E-beam deposition can be used with a wide range of materials, including metals, ceramics, and semiconductors.
- High Melting Point Materials: This method is particularly effective for depositing materials with very high melting points, which are difficult to vaporize using other techniques.
-
Applications:
- E-beam deposition is used in various applications, including the fabrication of optical coatings, semiconductor devices, and protective coatings.
- It is also employed in research and development for creating thin films with specific properties for experimental purposes.
In summary, e-beam deposition is a highly controlled and versatile thin film deposition technique that leverages the power of electron beams to vaporize and deposit materials onto substrates in a vacuum environment. Its ability to produce high-purity, uniform films makes it indispensable in both industrial and research settings.
Summary Table:
Aspect | Details |
---|---|
Vacuum Environment | Maintained at ~10^-6 Torr to prevent contamination and oxidation. |
Electron Beam Generation | High-energy beam generated via an electron gun, accelerated by high voltage. |
Target Heating | Electron beam vaporizes target material, often in a rotating crucible. |
Deposition onto Substrate | Vaporized material condenses on a temperature-controlled substrate. |
Film Properties | Post-deposition treatments like annealing enhance film quality. |
Advantages | High purity, versatility, and ability to deposit high-melting-point materials. |
Applications | Optical coatings, semiconductors, protective coatings, and R&D. |
Discover how e-beam deposition can elevate your thin film projects—contact our experts today!