Electron beam deposition (E-Beam) is a highly precise and efficient thin-film deposition technique used to create conformal coatings on optical surfaces. The process involves vaporizing source materials in a vacuum chamber using electron-beam bombardment, followed by the condensation of the vapor onto substrates. This method is enhanced by computer-controlled parameters such as heating, vacuum levels, and substrate positioning, ensuring coatings of pre-specified thicknesses. E-Beam deposition is particularly advantageous for high-volume applications due to its rapid processing capabilities and the use of cost-effective evaporative materials. Additionally, the process can be further improved with ion beam assistance, resulting in denser and more robust coatings with reduced stress.
Key Points Explained:
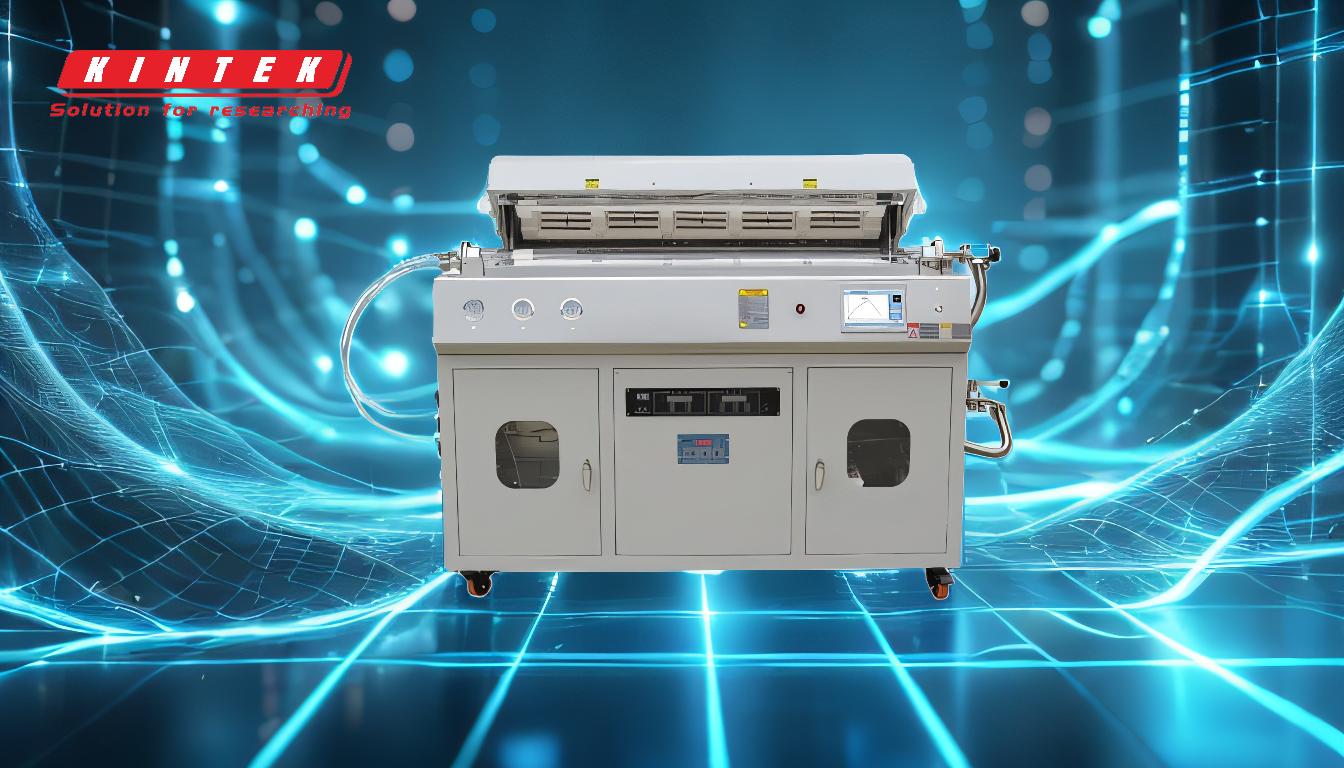
-
Vaporization of Source Materials:
- In electron beam deposition, the source material (often in powder or granular form) is vaporized using either heating or electron-beam bombardment. This step is crucial as it transforms the solid material into a vapor state, which is then deposited onto the substrate.
- The electron beam is generated by accelerating electrons through a high-voltage electric field, typically up to 10 kV. This intense energy causes the source material to evaporate or sublimate, releasing vapor into the chamber.
-
Vacuum Environment:
- The entire process takes place in a vacuum chamber. This environment is essential for several reasons:
- It allows for high vapor pressures at specific temperatures, which is necessary for efficient vaporization.
- It minimizes contamination, ensuring that the deposited thin film is pure and free from impurities that could degrade its performance.
- The vacuum also helps in controlling the deposition rate and uniformity of the coating.
- The entire process takes place in a vacuum chamber. This environment is essential for several reasons:
-
Condensation and Coating Formation:
- Once the source material is vaporized, the resulting vapor travels through the vacuum chamber and condenses onto the substrate. This condensation process forms a thin, uniform layer of the material on the substrate.
- The substrate's position and rotation are precisely controlled by computer systems to ensure that the coating is applied evenly and conforms to the desired specifications.
-
Precision Control:
- Electron beam deposition relies heavily on precision computer control to achieve high-quality coatings. Key parameters that are controlled include:
- Heating: The temperature must be carefully regulated to ensure proper vaporization of the source material.
- Vacuum Levels: Maintaining the correct vacuum pressure is crucial for the efficiency and quality of the deposition process.
- Substrate Location and Rotation: These factors determine the uniformity and thickness of the coating. Precise control ensures that the coating is applied evenly across the substrate.
- Electron beam deposition relies heavily on precision computer control to achieve high-quality coatings. Key parameters that are controlled include:
-
Ion Beam Assistance:
- The deposition process can be enhanced by using an ion beam. This additional step increases the adhesion energy between the coating and the substrate, resulting in:
- Denser Coatings: The ion beam helps to pack the material more tightly, reducing porosity and increasing density.
- Reduced Stress: The enhanced adhesion energy also reduces internal stresses within the coating, making it more robust and durable.
- The deposition process can be enhanced by using an ion beam. This additional step increases the adhesion energy between the coating and the substrate, resulting in:
-
Advantages of E-Beam Deposition:
- Rapid Processing: E-Beam deposition is faster than other methods like magnetron sputtering, making it ideal for high-volume commercial applications.
- Cost-Effectiveness: The process uses a wider array of less expensive evaporative materials compared to the costly targets required for magnetron sputtering.
- Flexibility: E-Beam deposition is versatile and can be used for a variety of materials, including polymers, making it suitable for a wide range of applications.
-
Applications:
- Electron beam deposition is widely used in industries that require high-precision optical coatings, such as:
- Optics: For creating anti-reflective coatings, mirrors, and lenses.
- Electronics: For depositing thin films in semiconductor manufacturing.
- Medical Devices: For applying biocompatible coatings on implants and other medical equipment.
- Electron beam deposition is widely used in industries that require high-precision optical coatings, such as:
In summary, electron beam deposition is a sophisticated and versatile technique for creating high-quality thin films. Its ability to precisely control the deposition process, combined with the use of a vacuum environment and ion beam assistance, results in coatings that are dense, uniform, and highly adherent. These characteristics make E-Beam deposition a preferred method for a wide range of industrial applications.
Summary Table:
Key Aspect | Details |
---|---|
Process | Vaporization of source materials using electron-beam bombardment. |
Environment | Vacuum chamber to ensure purity and control deposition rate. |
Condensation | Vapor condenses onto substrates, forming uniform thin films. |
Precision Control | Computer-regulated heating, vacuum levels, and substrate positioning. |
Ion Beam Assistance | Enhances coating density and reduces stress for more durable films. |
Advantages | Rapid processing, cost-effectiveness, and versatility for various materials. |
Applications | Optics, electronics, and medical devices requiring high-precision coatings. |
Discover how electron beam deposition can elevate your projects—contact us today for expert guidance!