Microwave sintering is an advanced material processing technique that uses microwave energy to heat and densify ceramic or powder materials. Unlike traditional sintering methods that rely on external heat sources, microwave sintering generates heat internally within the material through dielectric loss in a microwave electromagnetic field. This process offers significant advantages, including faster heating rates, uniform temperature distribution, energy efficiency, and the ability to produce fine-grained, high-density materials. However, it also presents challenges such as limited penetration depth in conductive materials and the need for specialized equipment like susceptor plates and cooling systems. Microwave sintering is particularly effective for high-performance ceramics and small-scale production, making it a valuable method in materials science and engineering.
Key Points Explained:
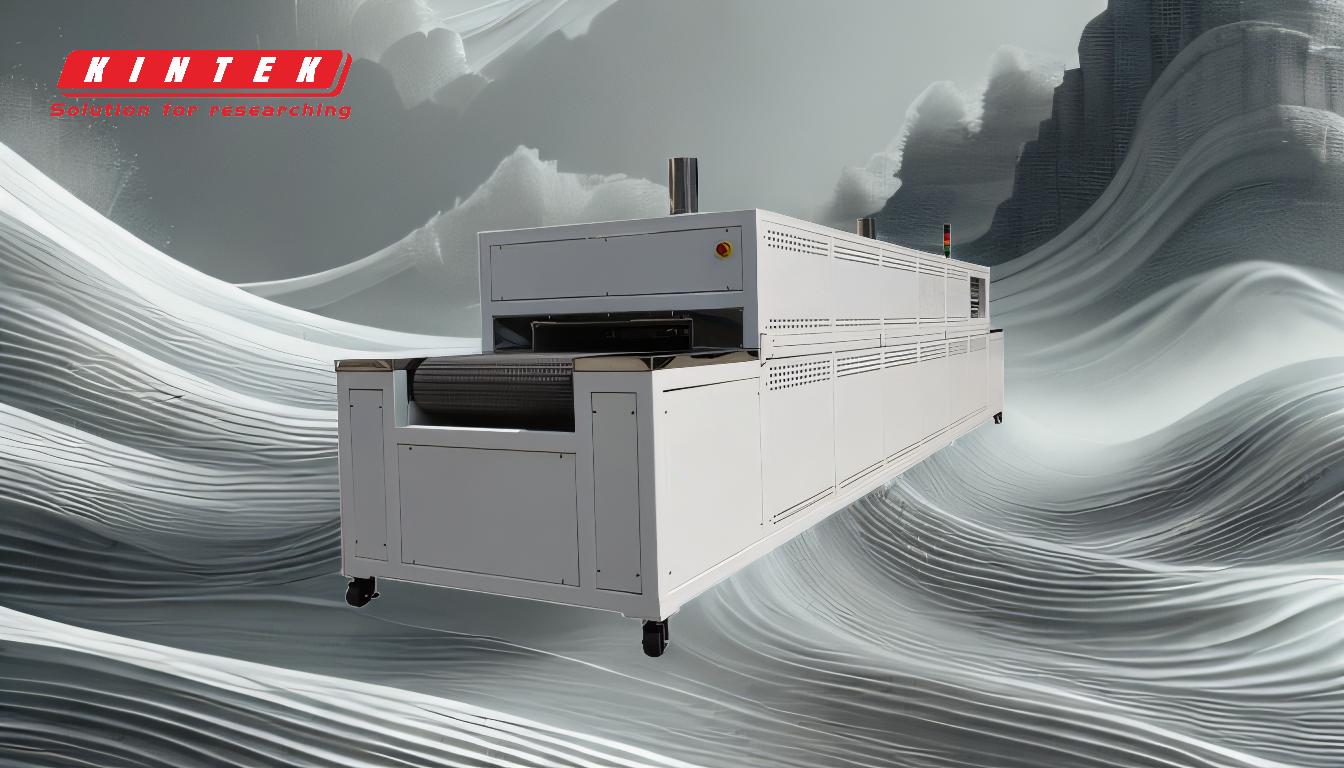
-
Principle of Microwave Sintering:
- Microwave sintering relies on the dielectric loss of materials when exposed to a microwave electromagnetic field. This interaction generates heat internally within the material, raising it to the sintering temperature.
- Unlike conventional sintering, which uses external heat sources and transfers heat via conduction, microwave sintering is a volumetric heating process. This means the entire material is heated simultaneously, leading to faster and more uniform heating.
-
Components of a Microwave Sintering Furnace:
- Microwave Source: Generates the microwave energy required for heating.
- Heating Cavity: The chamber where the material is placed and exposed to microwave energy.
- Material Transfer System: Facilitates the movement of materials into and out of the furnace.
- Susceptor Plates and Trays: Often used to absorb microwave energy and convert it into heat, especially for materials that do not couple well with microwaves.
-
Process Steps:
- Charging: The ceramic or powder material is placed into the furnace.
- Vacuuming: The furnace is evacuated to remove gases and impurities, ensuring a clean environment for sintering.
- Microwave Heating: Microwave energy is applied to heat the material to the sintering temperature.
- Insulation: The material is held at the sintering temperature for a specific period to allow chemical reactions and crystallization.
- Cooling: The material is gradually cooled to room temperature, often requiring auxiliary cooling systems to manage heat dissipation.
-
Advantages of Microwave Sintering:
- Faster Heating Speed: Microwave sintering heats materials much faster than conventional methods, reducing processing time.
- Uniform Temperature Distribution: Volumetric heating ensures even temperature distribution, minimizing thermal gradients.
- Energy Efficiency: Direct energy conversion reduces energy consumption.
- Fine-Grained Materials: The rapid heating and cooling processes help maintain fine grain sizes, improving material properties.
- Environmental Friendliness: The process prevents oxidation and pollution, enhancing product quality.
-
Challenges and Limitations:
- Penetration Depth: Microwaves penetrate only a short distance in materials with high conductivity or permeability, limiting the size of the materials that can be effectively sintered.
- Run-Away Behavior: Some materials may fail to couple with microwaves or exhibit unpredictable heating behavior.
- Limited Productivity: Typically, only one compact can be sintered at a time, which may restrict large-scale production.
- Cooling Requirements: The rapid heating process necessitates efficient cooling systems to prevent overheating of the equipment.
-
Applications:
- Microwave sintering is particularly effective for producing high-performance ceramic materials, such as bioceramics, where maintaining fine grain sizes is critical.
- It is also used in the preparation of advanced materials that require precise control over microstructure and density.
-
Comparison with Conventional Sintering:
- Heating Mechanism: Conventional sintering relies on radiant or resistance heating, followed by thermal conduction, while microwave sintering uses direct electromagnetic energy conversion.
- Energy Efficiency: Microwave sintering is more energy-efficient due to its volumetric heating nature.
- Material Properties: Microwave sintering often results in better material density and finer grain sizes compared to conventional methods.
In summary, microwave sintering is a highly efficient and effective method for processing advanced materials, offering significant advantages over traditional sintering techniques. However, its application is limited by material properties and equipment requirements, making it most suitable for specialized applications where fine-grained, high-density materials are essential.
Summary Table:
Aspect | Details |
---|---|
Principle | Internal heat generation via dielectric loss in a microwave field. |
Components | Microwave source, heating cavity, material transfer system, susceptor plates. |
Process Steps | Charging, vacuuming, microwave heating, insulation, cooling. |
Advantages | Faster heating, uniform temperature, energy efficiency, fine-grained materials. |
Challenges | Limited penetration depth, run-away behavior, cooling requirements. |
Applications | High-performance ceramics, advanced materials with precise microstructure. |
Comparison | More energy-efficient and better material properties vs. conventional sintering. |
Ready to explore microwave sintering for your material processing needs? Contact our experts today to learn more!