Molybdenum enhances corrosion resistance primarily through its ability to form stable, protective oxide layers on the surface of metals. When incorporated into alloys, molybdenum improves their resistance to pitting and crevice corrosion, especially in environments containing chlorides or acids. This makes molybdenum a valuable element in industries where materials are exposed to harsh conditions, such as chemical processing, marine applications, and high-temperature environments. Its lower density and cost-effectiveness compared to tungsten also make it a preferred choice for applications like solar panel coatings and molybdenum boat manufacturing.
Key Points Explained:
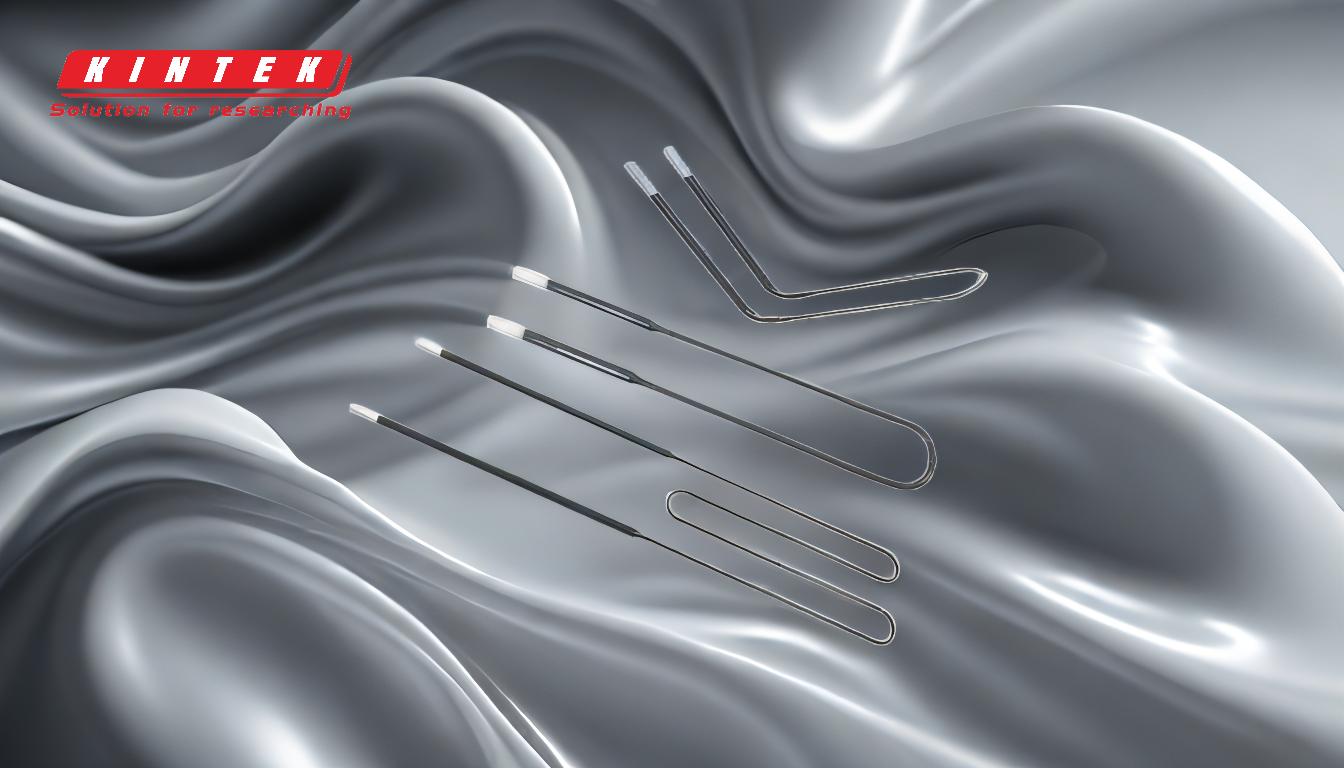
-
Formation of Protective Oxide Layers:
- Molybdenum forms stable oxide layers on metal surfaces, which act as a barrier against corrosive agents.
- These oxides are chemically inert and prevent further oxidation or degradation of the underlying metal.
-
Resistance to Pitting and Crevice Corrosion:
- Molybdenum significantly reduces the susceptibility of alloys to localized corrosion, such as pitting and crevice corrosion.
- This is particularly important in environments with chlorides, acids, or other aggressive chemicals.
-
Application in Harsh Environments:
- Molybdenum-containing alloys are widely used in industries like chemical processing, marine engineering, and high-temperature applications.
- Its ability to withstand extreme conditions makes it ideal for components exposed to corrosive media.
-
Comparison with Tungsten:
- Molybdenum has a lower density and is more cost-effective than tungsten, making it a practical alternative.
- While tungsten has a lower vapor pressure and is less prone to contamination, molybdenum's corrosion resistance and affordability make it suitable for many applications, including molybdenum boat production.
-
Role in Thin-Film Coatings:
- Molybdenum is used in coatings for solar panels and other thin-film applications due to its excellent thermal and electrical conductivity.
- Its corrosion resistance ensures the longevity and durability of these coatings in outdoor and high-temperature environments.
-
Synergy with Other Materials:
- Molybdenum can be combined with other materials, such as graphene or polymers, to enhance their chemical and thermal properties.
- This synergy improves the overall performance of composite materials in corrosive environments.
By understanding these key points, it becomes clear how molybdenum plays a vital role in enhancing corrosion resistance, making it an indispensable material in various industrial applications.
Summary Table:
Key Mechanism | Benefits |
---|---|
Formation of Protective Oxide Layers | Acts as a barrier against corrosive agents; prevents further oxidation. |
Resistance to Pitting and Crevice Corrosion | Reduces susceptibility to localized corrosion in chloride or acid environments. |
Application in Harsh Environments | Ideal for chemical processing, marine engineering, and high-temperature uses. |
Comparison with Tungsten | Lower density and cost-effective, making it a practical alternative. |
Role in Thin-Film Coatings | Ensures durability in solar panels and high-temperature applications. |
Synergy with Other Materials | Enhances chemical and thermal properties of composites in corrosive settings. |
Want to learn more about molybdenum's corrosion-resistant properties? Contact our experts today for tailored solutions!