Plasma-enhanced chemical vapor deposition (PECVD) significantly improves the CVD process by utilizing plasma to generate reactive species, activate surfaces, and enhance film growth. Plasma, composed of electrons and ions, breaks chemical bonds through electron-molecule collisions, creating radicals in the gas phase. These radicals and ions bombard the surface, activating it by forming dangling bonds and densifying the film by etching weakly bonded groups. This process not only enhances the quality of the deposited films but also allows for lower processing temperatures, making it suitable for heat-sensitive materials. Additionally, the vacuum environment in processes like short path vacuum distillation reduces boiling points, enabling efficient distillation of heavier molecules. Overall, plasma's role in PECVD is critical for achieving high-quality, uniform, and durable coatings.
Key Points Explained:
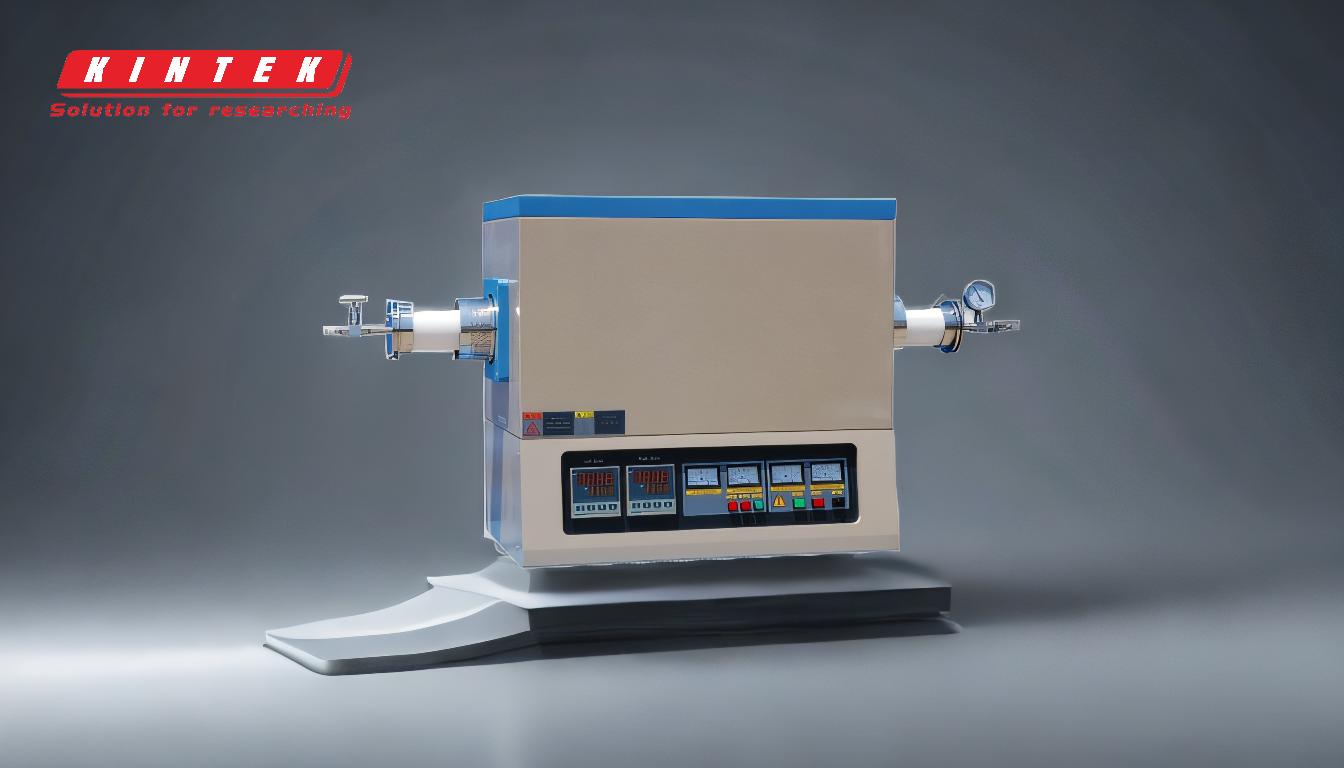
-
Plasma Generation and Reactive Species Formation:
- Plasma in PECVD is ignited using a high-frequency voltage applied to low-pressure gas, typically a hydrocarbon feedstock.
- Inelastic collisions within the plasma create reactive species such as radicals, ions, and electrons, which are essential for the deposition process.
- These reactive species are highly energetic and capable of breaking chemical bonds, initiating the growth of the desired film.
-
Surface Activation and Film Growth:
- Ions in the plasma bombard the substrate surface, creating dangling bonds that enhance surface reactivity.
- This activation promotes the adsorption of reactive species, leading to uniform film growth.
- The bombardment also densifies the film by etching away weakly bonded terminating groups, resulting in a more compact and durable coating.
-
Lower Processing Temperatures:
- Plasma enables CVD to occur at lower temperatures compared to traditional thermal CVD.
- This is particularly beneficial for depositing films on heat-sensitive substrates, such as polymers or electronic components, without causing thermal degradation.
-
Enhanced Film Properties:
- PECVD produces films with improved surface smoothness, electrical conductivity, and thermal conductivity.
- The even buildup of coating material ensures compatibility with other materials, making it suitable for applications in electronics, optics, and protective coatings.
-
Comparison with Short Path Vacuum Distillation:
- Similar to how vacuum reduces boiling points in short path vacuum distillation, plasma in PECVD lowers the energy required for chemical reactions.
- Both processes benefit from reduced operating pressures, enabling efficient processing of sensitive materials.
-
Applications of PECVD:
- PECVD is widely used in the semiconductor industry for depositing thin films, such as silicon nitride and silicon dioxide, on wafers.
- It is also employed in the production of protective coatings for electronic devices, ensuring durability and resistance to environmental factors.
By leveraging plasma, PECVD offers a versatile and efficient method for depositing high-quality films, making it indispensable in modern manufacturing and material science.
Summary Table:
Aspect | Description |
---|---|
Plasma Generation | High-frequency voltage ignites plasma, creating reactive species like radicals. |
Surface Activation | Ions bombard surfaces, forming dangling bonds for enhanced reactivity. |
Lower Processing Temperatures | Enables CVD on heat-sensitive materials without thermal degradation. |
Enhanced Film Properties | Produces smooth, conductive, and durable coatings. |
Applications | Used in semiconductors, electronics, and protective coatings. |
Learn how PECVD can revolutionize your material processing—contact our experts today!