Physical Vapor Deposition (PVD) coating is a sophisticated process used to create thin, durable, and highly adherent coatings on various substrates. It involves vaporizing a solid material in a vacuum environment and depositing it atom by atom onto a target surface. This process enhances the substrate's properties, such as durability, functionality, and appearance, while being environmentally friendly. The PVD process typically involves four to five main steps, depending on the specific technique used, and can be tailored to produce coatings with specific properties by introducing reactive gases.
Key Points Explained:
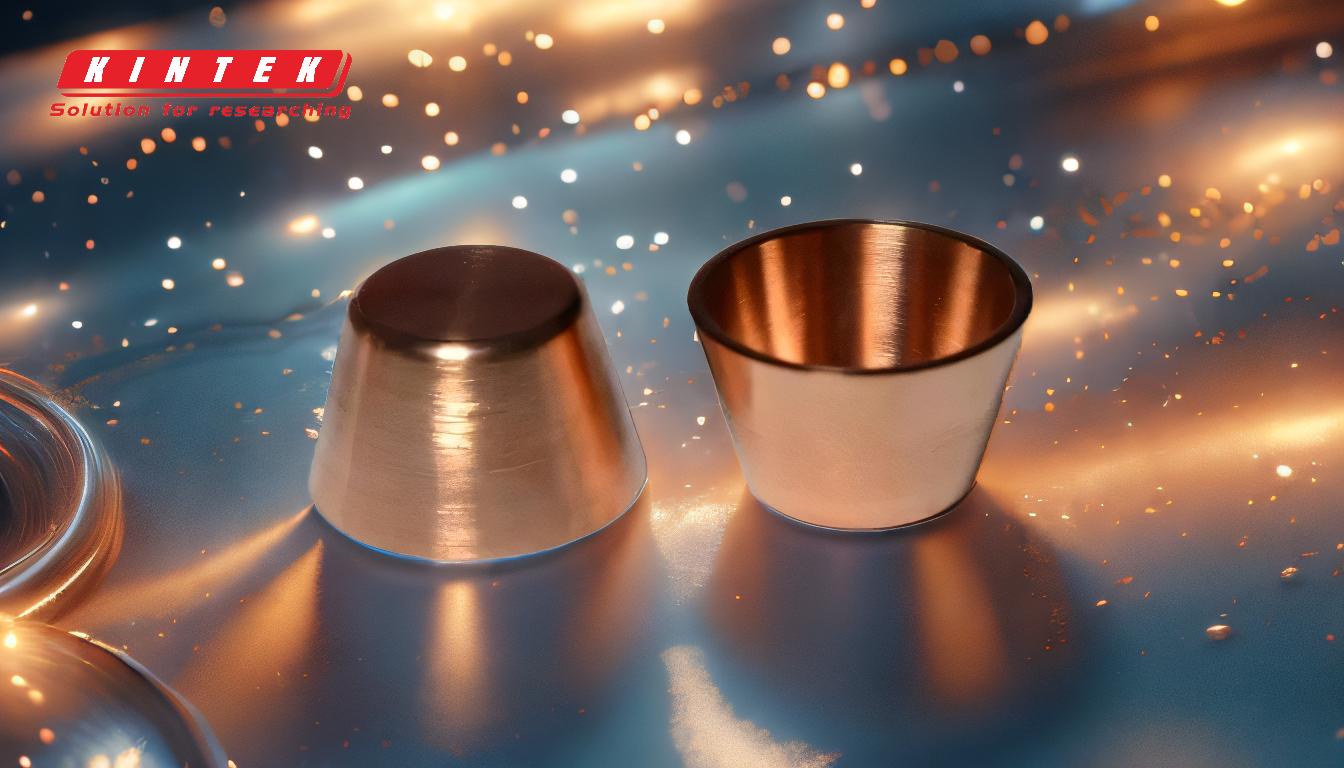
-
Vacuum Environment:
- PVD coating occurs in a vacuum chamber to ensure a clean and controlled environment.
- The vacuum prevents contamination and allows the vaporized material to deposit uniformly on the substrate.
- Inert gases like Argon are often used to maintain a chemically unreactive atmosphere, ensuring the purity of the coating.
-
Vaporization of the Target Material:
- The solid target material is vaporized using high-energy sources such as electron beams, ion bombardment, or cathodic arcs.
- This step involves bombarding the target material with energy to dislodge atoms, converting them into a vapor or plasma state.
- Techniques like sputtering or thermal evaporation are commonly used for this purpose.
-
Transportation of Vaporized Material:
- The vaporized atoms or molecules are transported through the vacuum chamber to the substrate.
- This step ensures that the vaporized material reaches the substrate uniformly, allowing for even deposition.
-
Reaction with Gases (Optional):
- Reactive gases such as nitrogen, oxygen, or hydrocarbons can be introduced into the chamber to modify the composition of the coating.
- For example, adding nitrogen can result in the formation of metal nitrides, which are known for their hardness and wear resistance.
- This step allows for the creation of coatings with specific properties, such as metal oxides, carbides, or nitrides.
-
Deposition on the Substrate:
- The vaporized material condenses on the substrate, forming a thin, uniform layer.
- The coating bonds strongly with the substrate at the atomic level, creating a highly adherent and durable layer.
- The thickness of the coating is typically in the micron range, making it extremely thin yet effective.
-
Purging the Chamber:
- After deposition, the chamber is purged with inert gases to remove any residual vapors or byproducts.
- This step ensures the cleanliness and safety of the process, preparing the chamber for the next cycle.
-
Benefits of PVD Coating:
- Durability: The coatings are highly resistant to wear, corrosion, and oxidation.
- Functionality: PVD coatings can enhance properties like hardness, lubricity, and electrical conductivity.
- Aesthetics: The process can produce coatings with a wide range of colors and finishes.
- Environmental Friendliness: PVD is a clean process with minimal waste and no harmful byproducts.
-
Applications of PVD Coating:
- Industrial Tools: Cutting tools, molds, and dies benefit from increased wear resistance.
- Automotive: Components like pistons, gears, and decorative trims are coated for durability and aesthetics.
- Medical Devices: Surgical instruments and implants are coated for biocompatibility and corrosion resistance.
- Electronics: PVD coatings are used in semiconductors, displays, and sensors for improved performance.
By understanding these key points, a purchaser of equipment or consumables can evaluate the suitability of PVD coating for their specific needs, ensuring optimal performance and cost-effectiveness.
Summary Table:
Key Aspect | Details |
---|---|
Process | Vaporizes solid material in a vacuum, depositing it atom by atom on a surface. |
Steps | Vacuum environment, vaporization, transportation, reaction (optional), deposition, purging. |
Benefits | Durability, functionality, aesthetics, environmental friendliness. |
Applications | Industrial tools, automotive, medical devices, electronics. |
Environmental Impact | Minimal waste, no harmful byproducts. |
Learn how PVD coating can improve your products—contact us today for expert advice!