A pyrolysis machine works by thermally decomposing organic materials like biomass, plastics, or tires in the absence of oxygen. The process involves several stages: material preparation (drying, shredding), feeding into a reactor, heating to high temperatures (200-900°C), and decomposing the material into syngas, bio-oil, and bio-char. The syngas is often recycled to fuel the reactor, while bio-oil and bio-char are collected for further use. The machine includes systems for gas purification, waste heat recovery, and emission control to ensure efficient and environmentally friendly operation.
Key Points Explained:
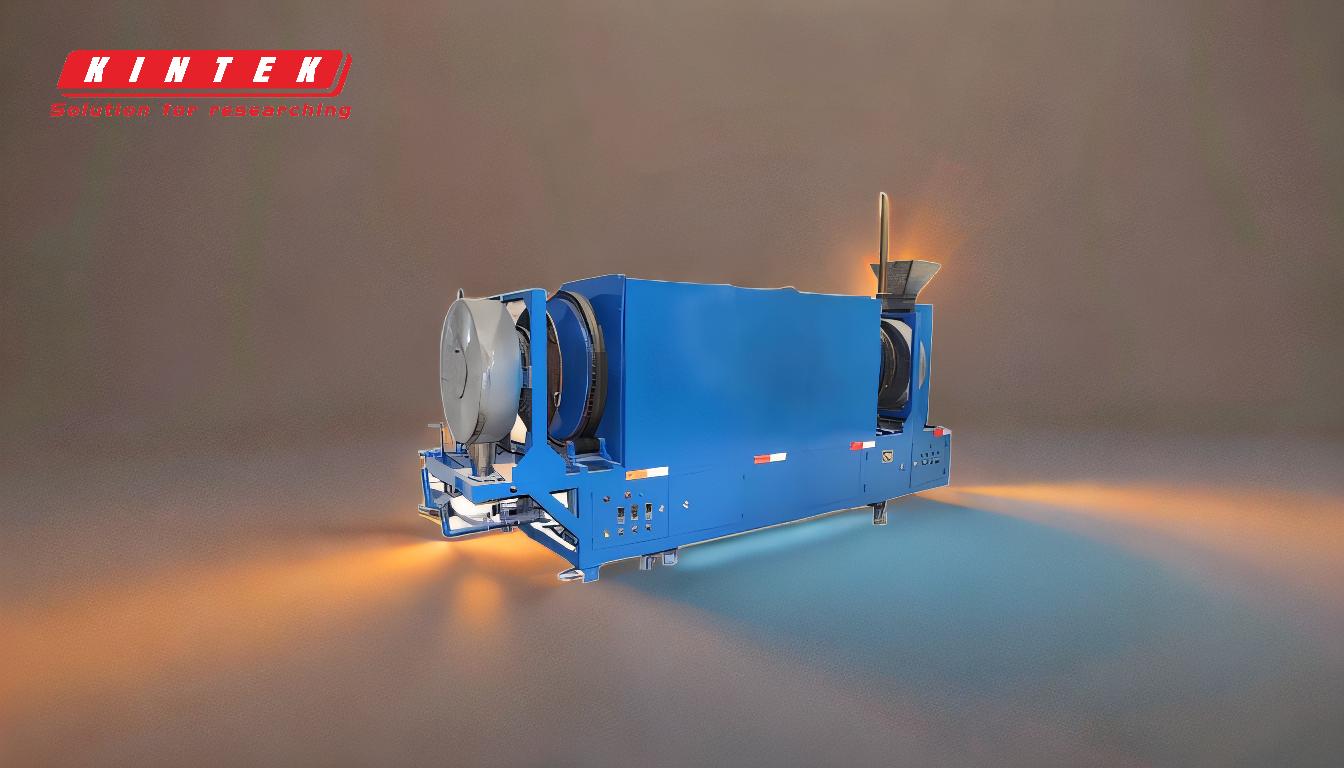
-
Material Preparation:
- Crushing and Drying: Materials like biomass, plastics, or tires are first shredded and dried to reduce moisture content (≤15%) and size (≤30mm). This ensures efficient pyrolysis.
- Pre-Treatment: Non-plastic impurities are removed, and the material is ground to the required size for uniform heating.
-
Feeding into the Reactor:
- The prepared material is fed into a pyrolysis reactor, which operates in an oxygen-free environment to prevent combustion.
- The reactor is often a rotary kiln or a chamber designed to ensure even heating.
-
Heating and Pyrolysis:
- The reactor is heated to temperatures between 200-900°C, depending on the material and desired outputs.
- The absence of oxygen causes the material to decompose rather than burn, producing syngas, bio-oil, and bio-char.
-
Output Separation:
- Biochar: Solid residue settles at the bottom of the reactor and is collected for use as a soil amendment or sorbent.
- Bio-Oil: Vapors are condensed into liquid oil, which can be refined for use as fuel or industrial feedstock.
- Syngas: Non-condensable gases are cleaned, desulfurized, and recycled to fuel the reactor or used as an energy source.
-
Gas and Heat Management:
- Combustible gases generated during pyrolysis are cleaned and used to heat the reactor, improving energy efficiency.
- Waste heat from the process is often reused to preheat or dry incoming materials, reducing overall energy consumption.
-
Emission Control:
- Smoke and flue gases are treated through de-dusting and purification systems to meet environmental standards before being discharged.
- Advanced systems include cyclones, scrubbers, and filters to remove particulates and harmful gases.
-
Safety and Automation:
- Pyrolysis machines are equipped with safety systems to monitor temperature, pressure, and gas composition, ensuring safe operation.
- Automation controls optimize the process for efficiency and consistency.
-
Applications of Outputs:
- Bio-Oil: Used as a renewable fuel or refined into chemicals.
- Biochar: Improves soil fertility or acts as a carbon sorbent.
- Syngas: Provides energy for the reactor or external use.
By following these steps, a pyrolysis machine efficiently converts waste materials into valuable products while minimizing environmental impact.
Summary Table:
Stage | Key Process | Output |
---|---|---|
Material Preparation | Shredding, drying (≤15% moisture, ≤30mm size), and pre-treatment of materials | Prepared feedstock for pyrolysis |
Feeding into Reactor | Material fed into an oxygen-free reactor (rotary kiln or chamber) | Evenly heated material ready for pyrolysis |
Heating and Pyrolysis | Heating to 200-900°C in absence of oxygen | Syngas, bio-oil, and bio-char produced |
Output Separation | Biochar collected as solid residue; bio-oil condensed; syngas cleaned and reused | Biochar, bio-oil, and syngas ready for use |
Gas and Heat Management | Combustible gases recycled; waste heat reused for preheating/drying | Improved energy efficiency and reduced energy consumption |
Emission Control | Smoke and flue gases treated with cyclones, scrubbers, and filters | Environmentally compliant emissions |
Safety and Automation | Monitors temperature, pressure, and gas composition; automation for optimization | Safe, efficient, and consistent operation |
Applications | Bio-oil as fuel/chemicals; biochar for soil/adsorption; syngas for energy | Renewable energy, soil enhancement, and industrial feedstock |
Discover how a pyrolysis machine can transform waste into valuable resources—contact our experts today!