Pyrolysis is a thermochemical process that decomposes organic materials at high temperatures in the absence of oxygen. This absence of oxygen prevents combustion, allowing the material to break down into smaller molecules and chemical compounds, producing gases, liquids (such as pyrolysis oil or bio-oil), and solids. The process typically occurs at temperatures exceeding 430°C (800°F) and is used to convert waste or biomass into valuable products while minimizing pollutants and harmful emissions. Pyrolysis is widely applied in industries such as waste management, energy production, and chemical refining due to its ability to produce clean and usable outputs without burning the feedstock.
Key Points Explained:
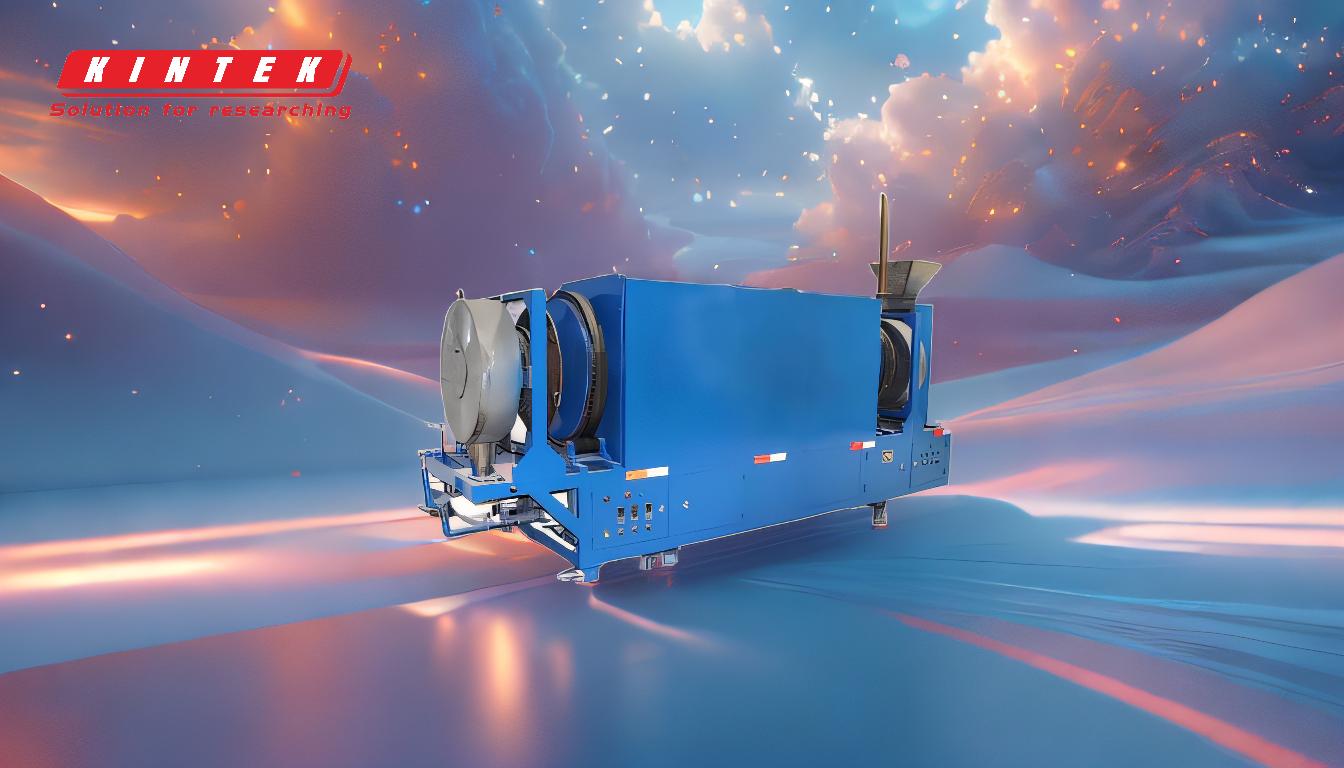
-
Definition and Mechanism of Pyrolysis
- Pyrolysis is the thermal decomposition of organic materials in the absence of oxygen.
- The process involves heating the material to high temperatures (typically 350°C–800°C) in a non-reactive atmosphere, causing the chemical bonds in the material to break down.
- Without oxygen, combustion is avoided, and the material decomposes into smaller molecules, producing gases, liquids (bio-oil), and solid residues.
-
Role of Oxygen Absence
- The absence of oxygen is critical to prevent combustion, which would release heat, produce ash, and generate harmful pollutants like dioxins and furans.
- By excluding oxygen, pyrolysis ensures controlled chemical reactions, leading to the breakdown of the material into useful products rather than burning it.
-
Temperature and Pressure Conditions
- Pyrolysis typically occurs at elevated temperatures, ranging from 350°C to 800°C, depending on the material and desired products.
- The process often involves pressure buildup within the reactor, which aids in breaking down larger molecules into smaller components.
-
Products of Pyrolysis
- Gases: Includes syngas (a mixture of hydrogen, carbon monoxide, and methane), which can be used as a fuel or chemical feedstock.
- Liquids: Pyrolysis oil or bio-oil, a liquid fuel that can be refined further for energy or chemical production.
- Solids: Char or biochar, a carbon-rich residue that can be used as a soil amendment or fuel.
-
Applications and Benefits
- Waste Management: Converts waste materials like plastics, biomass, and rubber into valuable products, reducing landfill dependency.
- Energy Production: Produces syngas and bio-oil, which can be used as renewable energy sources.
- Pollution Reduction: Minimizes emissions of harmful pollutants compared to traditional burning methods.
-
Comparison to Combustion
- Combustion requires oxygen and results in the complete oxidation of the material, producing heat, ash, and pollutants.
- Pyrolysis, in contrast, avoids oxidation, allowing for the recovery of usable products and reducing environmental impact.
-
Industrial Relevance
- Pyrolysis is widely used in industries such as petroleum refining (thermal cracking), biomass conversion, and waste-to-energy systems.
- It is a key technology for sustainable resource recovery and circular economy initiatives.
By understanding these key points, it becomes clear how pyrolysis operates without oxygen to transform organic materials into valuable products while minimizing environmental harm. This makes it a versatile and environmentally friendly process for various industrial applications.
Summary Table:
Aspect | Details |
---|---|
Definition | Thermal decomposition of organic materials in the absence of oxygen. |
Temperature Range | 350°C–800°C, depending on material and desired products. |
Key Products | Gases (syngas), liquids (bio-oil), and solids (biochar). |
Applications | Waste management, energy production, chemical refining. |
Environmental Benefit | Minimizes pollutants and harmful emissions compared to combustion. |
Discover how pyrolysis can revolutionize your waste and energy processes—contact us today!