Time is a critical factor in the pyrolysis process, influencing the degree of thermal conversion, product composition, and overall efficiency. The residence time, which refers to the duration that the feedstock remains in the pyrolysis chamber, directly impacts the breakdown of organic materials and the formation of gas, liquid, and solid products. Longer residence times generally lead to more complete decomposition, favoring the production of non-condensable gases, while shorter times may result in higher yields of solid char or liquid bio-oil. Additionally, the interplay between time and other factors like temperature, feedstock properties, and particle size further determines the quality and distribution of pyrolysis products. Understanding how time affects pyrolysis is essential for optimizing process conditions to achieve desired outcomes.
Key Points Explained:
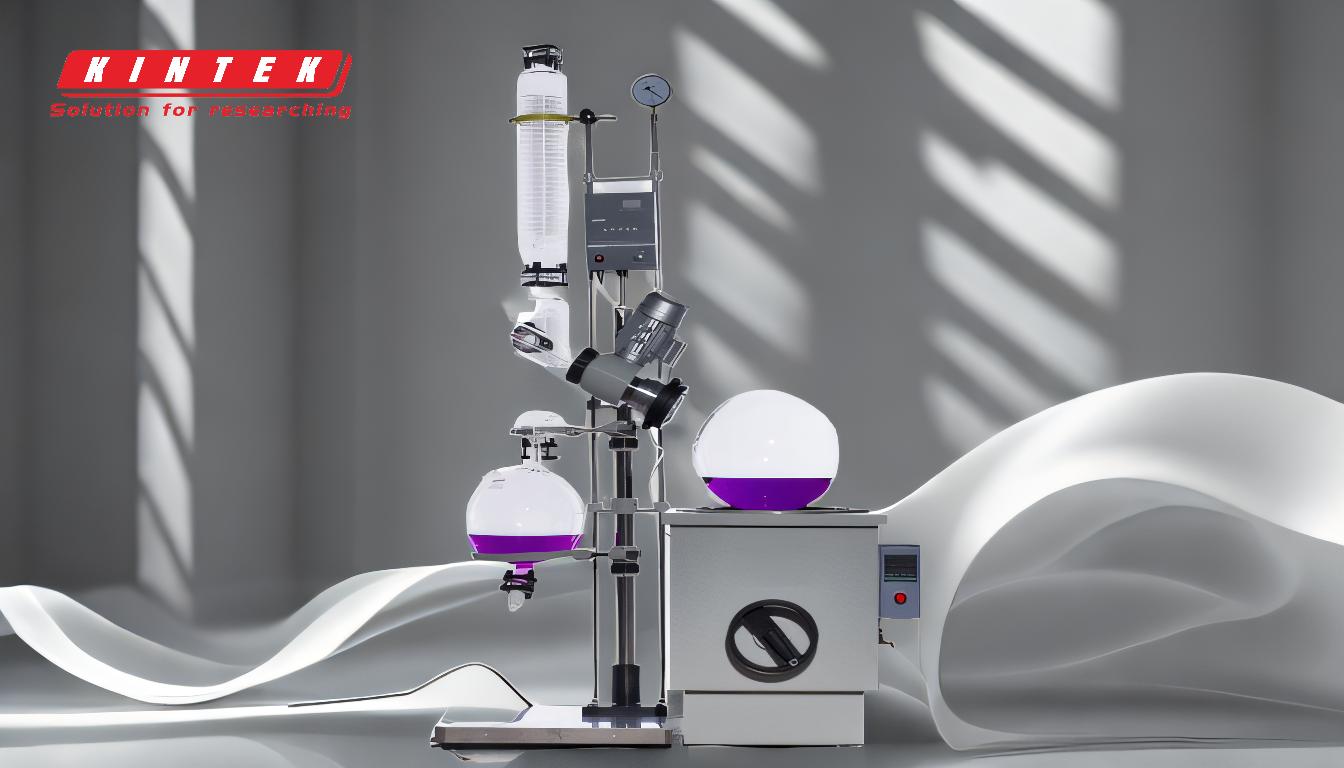
-
Residence Time and Thermal Conversion:
- Residence time refers to the duration the feedstock spends in the pyrolysis chamber.
- Longer residence times allow for more complete thermal decomposition of organic materials, leading to higher yields of non-condensable gases.
- Shorter residence times may result in incomplete decomposition, favoring the production of solid char or liquid bio-oil.
- The degree of thermal conversion is directly proportional to the residence time, as more time allows for greater breakdown of complex molecules into simpler compounds.
-
Impact on Product Composition:
- The composition of pyrolysis products (gas, liquid, and solid) is influenced by residence time.
- Longer residence times tend to increase the production of non-condensable gases (e.g., hydrogen, methane, and carbon monoxide) due to prolonged exposure to high temperatures.
- Shorter residence times favor the formation of liquid bio-oil and solid char, as the feedstock does not spend enough time in the reactor to fully decompose into gases.
- The balance between these products can be adjusted by controlling the residence time to meet specific application requirements.
-
Interaction with Temperature:
- Residence time works in tandem with temperature to determine pyrolysis outcomes.
- Higher temperatures combined with longer residence times maximize gas production, as both factors promote the breakdown of organic materials.
- Lower temperatures with shorter residence times are more suitable for producing high-quality solid char or liquid bio-oil.
- The optimal combination of temperature and residence time depends on the desired product distribution and feedstock properties.
-
Feedstock Properties and Particle Size:
- The nature of the feedstock, including moisture content, fixed carbon, and volatile matter, influences how residence time affects pyrolysis.
- Smaller particle sizes decompose more quickly, reducing the required residence time for complete thermal conversion.
- Larger particles may require longer residence times to achieve the same level of decomposition.
- Moisture content in the feedstock can also affect the process, as it may require additional time for evaporation before pyrolysis begins.
-
Process Efficiency and Optimization:
- Residence time is a key factor in optimizing pyrolysis efficiency.
- Too short a residence time may result in incomplete decomposition and lower yields of desired products.
- Too long a residence time can lead to excessive energy consumption and over-decomposition of materials, reducing the quality of solid or liquid products.
- Balancing residence time with other process parameters (e.g., temperature, pressure, and feed rate) is essential for achieving optimal efficiency and product quality.
-
Environmental and Economic Considerations:
- Residence time affects the energy consumption and greenhouse gas (GHG) emissions of the pyrolysis process.
- Longer residence times may increase energy use and emissions, particularly if the process requires additional heating or extended reactor operation.
- Optimizing residence time can reduce energy costs and minimize environmental impacts, making the process more sustainable and economically viable.
By carefully controlling residence time and understanding its interaction with other factors, pyrolysis processes can be tailored to produce specific products efficiently and sustainably. This knowledge is crucial for equipment and consumable purchasers aiming to optimize pyrolysis systems for their unique applications.
Summary Table:
Factor | Impact on Pyrolysis |
---|---|
Residence Time | Longer times favor gas production; shorter times favor bio-oil and char. |
Temperature Interaction | Higher temps + longer times maximize gas; lower temps + shorter times favor bio-oil. |
Feedstock Properties | Moisture, fixed carbon, and particle size influence required residence time. |
Process Efficiency | Optimal residence time balances energy use, product quality, and decomposition. |
Environmental Impact | Longer times may increase energy use and emissions; optimization reduces costs. |
Ready to optimize your pyrolysis process? Contact our experts today for tailored solutions!