Black PVD (Physical Vapor Deposition) coating is renowned for its durability, making it a popular choice in industries where surface protection and longevity are critical. The durability of black PVD coating is influenced by factors such as the substrate material, coating thickness, bond strength, and environmental conditions like temperature and wear. It offers exceptional wear resistance, corrosion resistance, and hardness, making it suitable for demanding applications in automotive, aerospace, and medical industries. While the coating is thin (0.5 to 5 microns), its robust properties ensure it outperforms traditional finishes in terms of durability and longevity.
Key Points Explained:
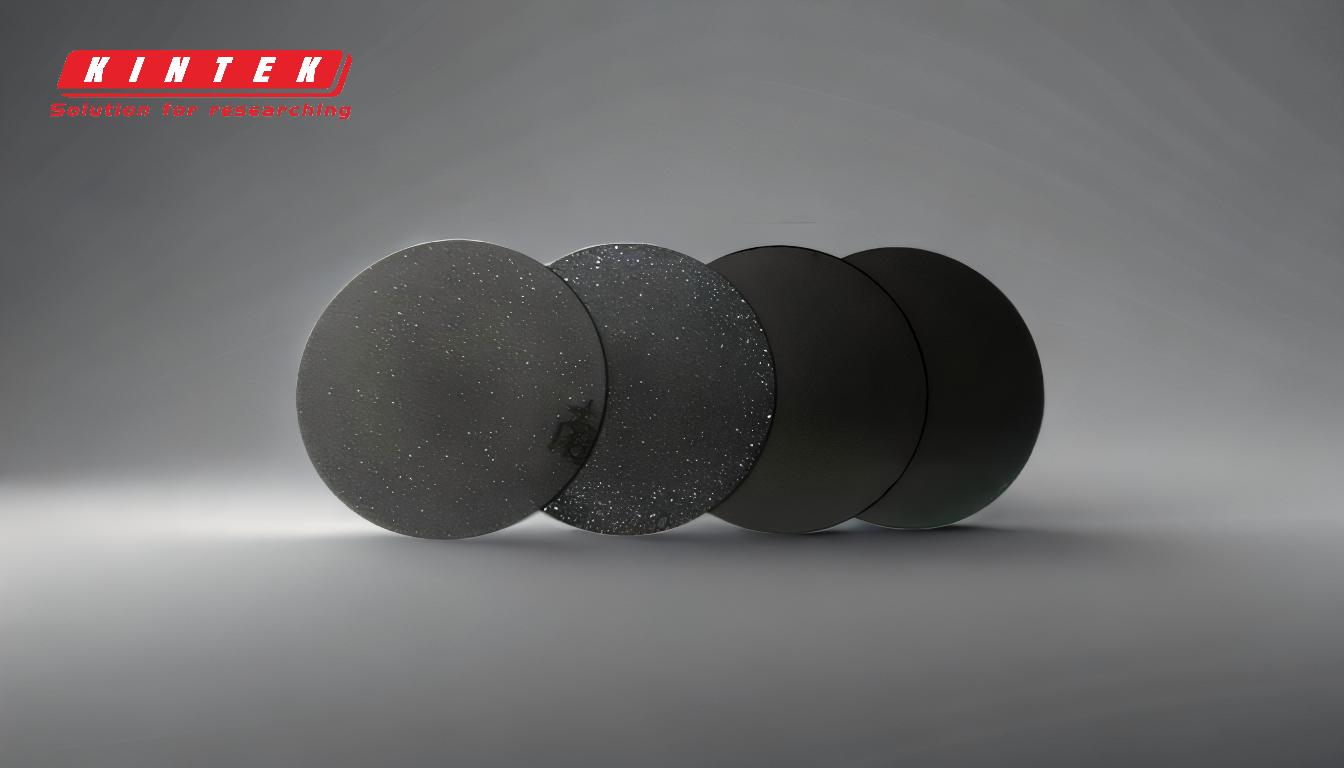
-
Durability Factors of Black PVD Coating
- Substrate Material: The underlying material significantly impacts the durability of the coating. For instance, TiN coatings on Ti-6Al-4V alloy enhance fatigue limits and endurance.
- Coating Thickness: Black PVD coatings are typically thin (0.5 to 5 microns), but their thinness does not compromise durability. Instead, it allows for precise replication of the original finish.
- Bond Strength: The adhesion between the coating and substrate is critical. Strong bonding ensures the coating remains intact under stress or wear.
- Environmental Exposure: Resistance to high temperatures, abrasion, and corrosion contributes to its durability in harsh environments.
-
Exceptional Properties of Black PVD Coating
- Wear Resistance: PVD coatings are highly resistant to wear and tear, making them ideal for components subjected to friction or mechanical stress.
- Corrosion Resistance: Black PVD coatings provide excellent protection against oxidation and corrosion, extending the lifespan of coated materials.
- Hardness: The coatings are super-hard, offering superior durability compared to traditional finishes.
- Low Friction: Reduced friction properties enhance performance in applications like automotive or aerospace components.
-
Applications and Industry Suitability
- Automotive: Used for engine components, gears, and decorative trims due to wear resistance and aesthetic appeal.
- Aerospace: Ideal for turbine blades and other high-stress components requiring durability and corrosion resistance.
- Medical: Suitable for surgical instruments and implants due to biocompatibility and wear resistance.
- Industrial Tools: Enhances the lifespan of cutting tools and molds by reducing wear and friction.
-
Comparison to Traditional Finishes
- Black PVD coatings outperform traditional finishes like electroplating or powder coating in terms of hardness, wear resistance, and longevity.
- Their thinness allows for precise application without altering the dimensions of the substrate, making them suitable for intricate designs.
-
Limitations and Considerations
- While highly durable, black PVD coatings are not indestructible. Extreme mechanical stress or improper application can compromise their performance.
- Proper surface preparation and adherence to application guidelines are essential to maximize durability.
In conclusion, black PVD coating is a highly durable solution for various industries, offering superior wear resistance, corrosion resistance, and hardness. Its performance is influenced by factors like substrate material, coating thickness, and environmental conditions, but when applied correctly, it provides unmatched durability compared to traditional finishes.
Summary Table:
Aspect | Details |
---|---|
Durability Factors | Substrate material, coating thickness, bond strength, environmental exposure |
Key Properties | Wear resistance, corrosion resistance, hardness, low friction |
Applications | Automotive, aerospace, medical, industrial tools |
Comparison | Outperforms traditional finishes in hardness, wear resistance, and longevity |
Limitations | Requires proper surface preparation and application guidelines |
Learn how black PVD coating can enhance your products—contact our experts today!