PVD (Physical Vapor Deposition) plating is renowned for its exceptional durability, making it one of the most robust coatings available today. It outperforms traditional finishes like electroplating, offering superior resistance to abrasion, corrosion, and wear. PVD-coated items, such as jewelry, can last anywhere from 3 to 10 years with proper care, depending on factors like coating thickness, substrate type, and environmental conditions. Its high temperature tolerance and impact strength further enhance its suitability for demanding applications. Overall, PVD plating is a long-lasting and reliable solution for industries requiring durable and high-performance coatings.
Key Points Explained:
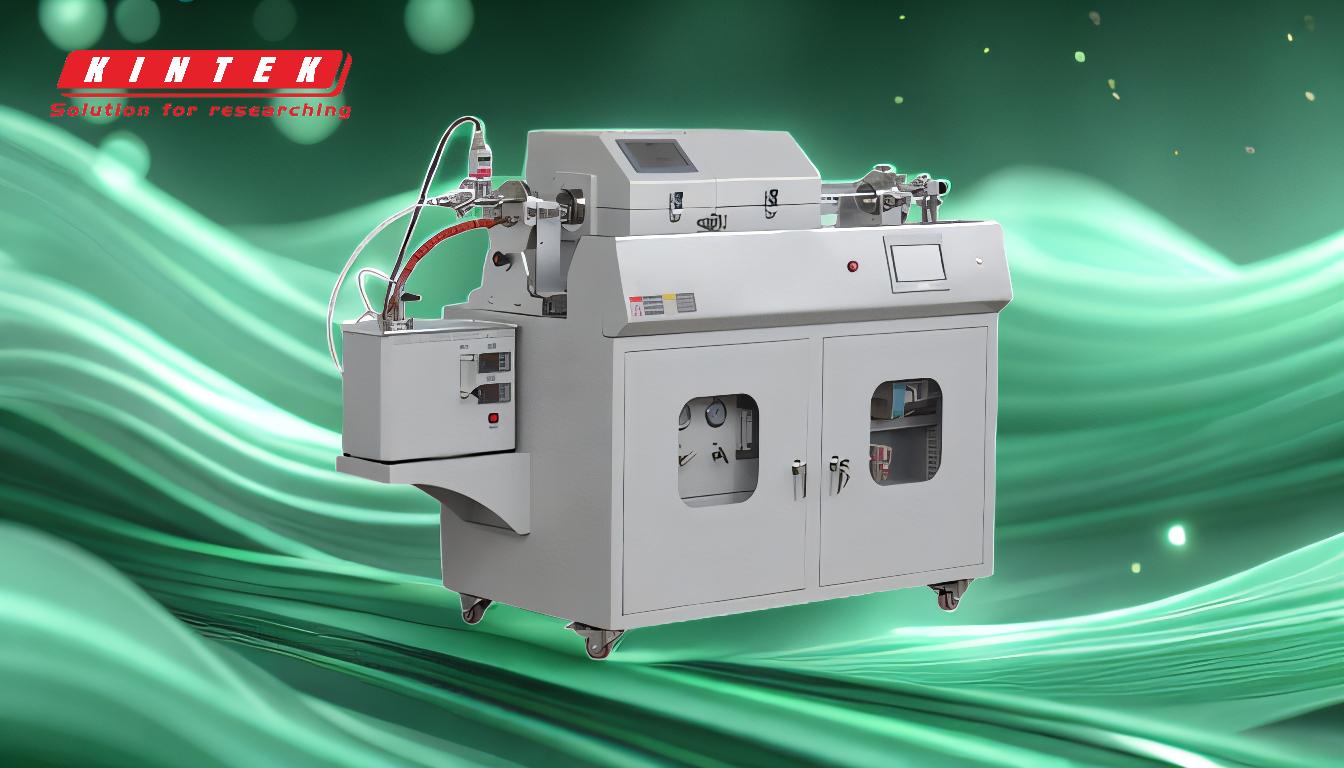
-
Superior Durability Compared to Traditional Finishes:
- PVD plating is considered the most durable coating available today, surpassing traditional finishes like electroplating. Its hardness and resistance to wear make it ideal for applications requiring long-lasting performance.
-
Longevity in Jewelry Applications:
- PVD-coated jewelry can last 3 years or more with everyday wear, significantly outperforming electroplated jewelry, which typically lasts about 1 year. With proper application and maintenance, PVD coatings on jewelry can even last up to 10 years.
-
Robust Resistance to Wear and Corrosion:
- PVD coatings exhibit excellent abrasion and corrosion resistance, making them suitable for harsh environments and demanding applications. This ensures that the coated items remain functional and aesthetically pleasing for extended periods.
-
High Temperature Tolerance and Impact Strength:
- PVD coatings can withstand high temperatures and have strong impact resistance, further enhancing their durability. This makes them ideal for industrial and high-stress applications where other coatings might fail.
-
Factors Affecting PVD Coating Lifespan:
- The durability of PVD coatings depends on several factors, including:
- Substrate Type: The material being coated can influence how well the PVD coating adheres and performs.
- Coating Thickness: Thicker coatings generally provide better durability.
- Bond Strength: A strong bond between the coating and substrate ensures longer-lasting performance.
- Environmental Exposure: High temperatures, wear, and corrosive environments can impact the coating's lifespan.
- The durability of PVD coatings depends on several factors, including:
-
Applications in Demanding Industries:
- Due to its durability, PVD plating is widely used in industries where longevity and performance are critical, such as aerospace, automotive, medical devices, and jewelry. Its ability to withstand harsh conditions makes it a preferred choice for high-performance applications.
In summary, PVD plating is a highly durable and reliable coating solution that offers superior performance compared to traditional finishes. Its longevity, resistance to wear and corrosion, and ability to withstand extreme conditions make it an excellent choice for a wide range of applications.
Summary Table:
Key Feature | Description |
---|---|
Durability | Surpasses traditional finishes like electroplating, offering superior resistance to wear and corrosion. |
Longevity in Jewelry | Lasts 3-10 years with proper care, outperforming electroplated jewelry (1 year). |
Wear & Corrosion Resistance | Excellent resistance to abrasion and corrosion, ideal for harsh environments. |
Temperature Tolerance | Withstands high temperatures and strong impacts, perfect for industrial use. |
Lifespan Factors | Depends on substrate type, coating thickness, bond strength, and environmental exposure. |
Applications | Used in aerospace, automotive, medical devices, and jewelry for high-performance needs. |
Ready to enhance your products with durable PVD coatings? Contact us today to learn more!