Induction furnaces are highly efficient due to their ability to directly heat metal through electromagnetic induction, minimizing energy loss. They offer precise temperature control, rapid heating, and are environmentally friendly compared to traditional furnaces. Their efficiency depends on factors like design, power supply, and the type of metal being melted. Modern induction furnaces can achieve thermal efficiencies of up to 90%, making them a preferred choice in industries requiring high-quality metal processing.
Key Points Explained:
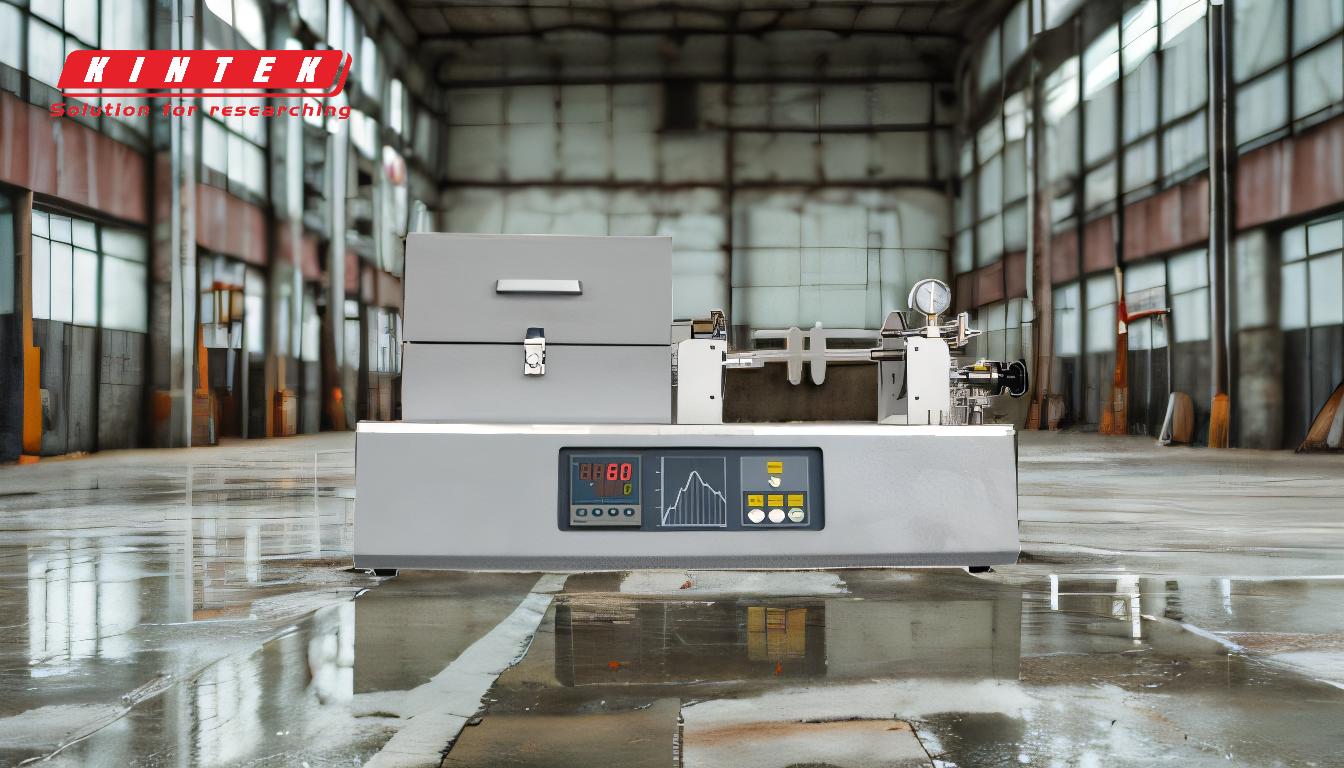
-
Principle of Operation:
- Induction furnaces work on the principle of electromagnetic induction, where an alternating current passes through a coil, generating a magnetic field. This field induces eddy currents in the metal, causing it to heat up due to resistance.
- This method eliminates the need for external heating elements, reducing energy loss and increasing efficiency.
-
Energy Efficiency:
- Induction furnaces are known for their high energy efficiency, often achieving thermal efficiencies of up to 90%. This is significantly higher than traditional furnaces, which typically operate at 40-60% efficiency.
- The direct heating method ensures minimal heat loss, as energy is transferred directly to the metal without heating the surrounding environment.
-
Rapid Heating and Precise Control:
- Induction furnaces can heat metals rapidly, reducing processing time and increasing productivity.
- They offer precise temperature control, which is crucial for maintaining the quality and consistency of the melted metal. This precision minimizes material waste and improves overall efficiency.
-
Environmental Benefits:
- Induction furnaces produce fewer emissions compared to traditional furnaces, making them more environmentally friendly.
- The absence of combustion processes reduces the release of harmful gases and particulate matter, contributing to a cleaner working environment.
-
Versatility and Adaptability:
- Induction furnaces can be used for a wide range of metals, including steel, iron, aluminum, and copper. This versatility makes them suitable for various industrial applications.
- They can be easily adapted to different production requirements, allowing for flexibility in manufacturing processes.
-
Maintenance and Longevity:
- Induction furnaces require less maintenance compared to traditional furnaces, as they have fewer moving parts and no combustion systems.
- The durability and longevity of induction furnaces contribute to their overall efficiency, reducing downtime and maintenance costs.
-
Economic Considerations:
- While the initial investment in induction furnaces may be higher than traditional furnaces, the long-term savings in energy costs and maintenance make them a cost-effective solution.
- The high efficiency and reduced operational costs can lead to significant economic benefits over the lifespan of the furnace.
-
Technological Advancements:
- Continuous advancements in induction furnace technology, such as improved power supplies and control systems, further enhance their efficiency and performance.
- Innovations like variable frequency drives and advanced cooling systems contribute to better energy management and operational efficiency.
In summary, induction furnaces are highly efficient due to their direct heating method, rapid heating capabilities, precise temperature control, and environmental benefits. Their versatility, low maintenance requirements, and economic advantages make them a preferred choice in various industrial applications. Technological advancements continue to improve their efficiency, making them an even more attractive option for metal processing industries.
Summary Table:
Key Feature | Description |
---|---|
Energy Efficiency | Achieves up to 90% thermal efficiency, surpassing traditional furnaces (40-60%). |
Rapid Heating | Heats metals quickly, reducing processing time and boosting productivity. |
Precise Temperature Control | Ensures consistent metal quality and minimizes material waste. |
Environmental Benefits | Produces fewer emissions and reduces harmful gases compared to traditional methods. |
Versatility | Suitable for melting steel, iron, aluminum, copper, and more. |
Low Maintenance | Fewer moving parts and no combustion systems reduce maintenance needs. |
Economic Advantages | Long-term savings in energy and maintenance costs outweigh higher initial investment. |
Technological Advancements | Innovations like variable frequency drives enhance efficiency and performance. |
Ready to boost your metal processing efficiency? Contact us today to explore induction furnace solutions!