Plastic pyrolysis efficiency is influenced by multiple factors, including the type and quality of the plastic feedstock, pyrolysis technology, and operational parameters such as temperature, residence time, and pressure. The process aims to convert waste plastic into valuable products like oil, gas, and char, but its efficiency varies depending on these factors. Proper control of operational settings and the use of high-quality feedstock can significantly improve yield and overall efficiency. Below, we explore the key factors and their impact on the efficiency of plastic pyrolysis.
Key Points Explained:
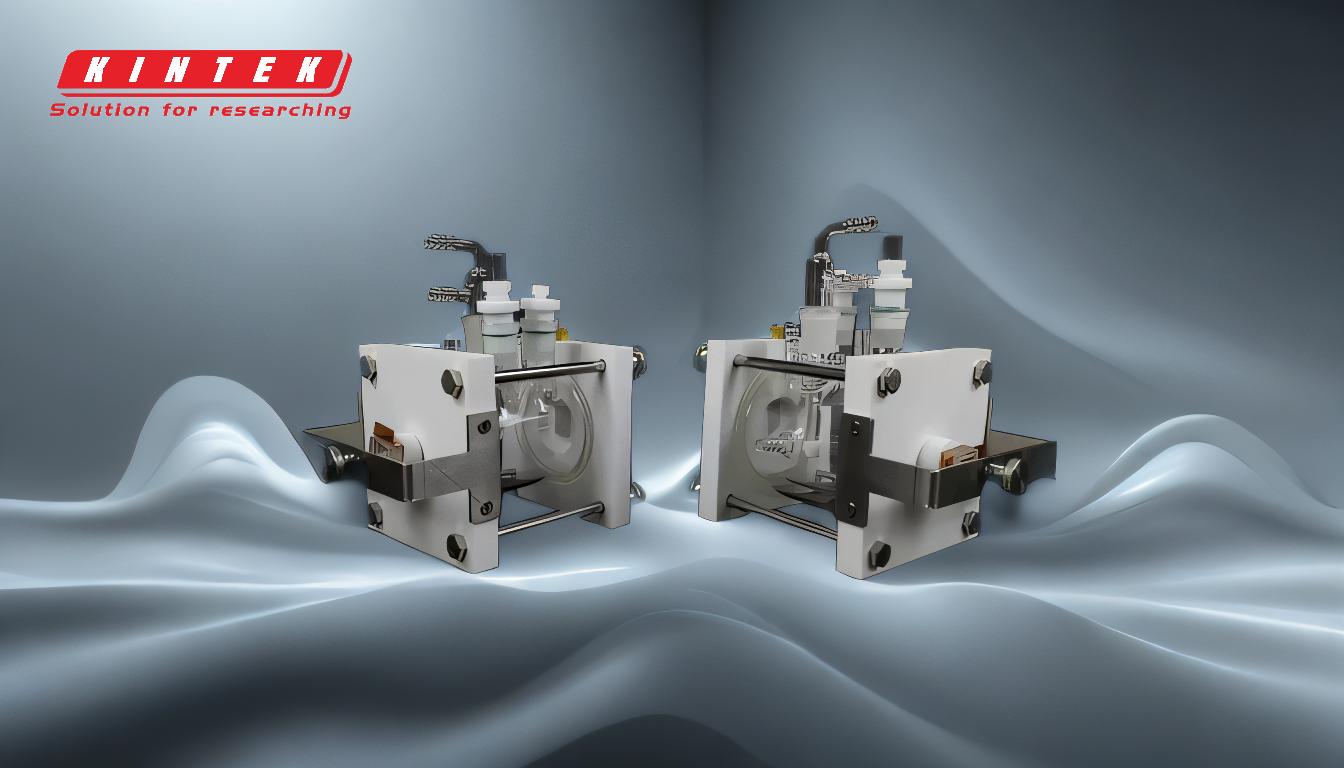
-
Feedstock Quality and Composition
- Type of Plastic: Different plastics (e.g., polyethylene, polypropylene, polystyrene) have varying degradation temperatures and pyrolysis yields. For instance, polyethylene and polypropylene generally yield more oil compared to PVC, which releases harmful gases like HCl.
- Cleanliness and Moisture Content: Contaminants and moisture in the plastic reduce efficiency by requiring additional energy to evaporate water and degrade impurities. Pure, dry, and clean plastic feedstock results in higher yields of pyrolysis products.
- Organic Fraction: The proportion of organic material in the feedstock affects the conversion efficiency. Plastics with a higher organic content are more efficiently degraded into gas and oil.
-
Pyrolysis Technology
- Reactor Type: Different reactor designs (e.g., rotary kiln, fluidized bed, fixed bed) have varying efficiencies. For example, rotary kilns rely on heat supply and rotation speed to ensure uniform heating and efficient degradation.
- Heating Mechanism: Direct or indirect heating methods impact energy transfer efficiency. Indirect heating often provides better control over temperature, improving yield and product quality.
- Catalyst Use: Some pyrolysis systems use catalysts to enhance the breakdown of plastics at lower temperatures, improving efficiency and reducing energy consumption.
-
Operational Parameters
- Temperature: Pyrolysis efficiency is highly dependent on temperature. Optimal temperatures for plastic pyrolysis typically range between 400°C and 600°C. Too low temperatures result in incomplete degradation, while excessively high temperatures may lead to excessive gas production or unwanted byproducts.
- Residence Time: The time the plastic spends in the reactor affects the extent of degradation. Longer residence times ensure complete breakdown but may reduce throughput. Shorter times may leave some plastic unprocessed.
- Pressure: Operating pressure influences the distribution of pyrolysis products. Lower pressures often favor the production of liquid oils, while higher pressures may increase gas yields.
-
Energy Efficiency
- Heat Recovery: Efficient heat recovery systems can reduce energy consumption by reusing heat generated during the process. This improves the overall energy efficiency of the pyrolysis system.
- Energy Input vs. Output: The energy required to heat the reactor and maintain operational conditions must be balanced against the energy content of the pyrolysis products (oil, gas, and char). High-quality feedstock and optimized conditions maximize energy output.
-
Product Yield and Quality
- Oil Yield: The primary goal of plastic pyrolysis is to produce high-quality pyrolysis oil, which can be used as fuel or further refined. Efficient systems achieve oil yields of 70-80% from suitable plastics.
- Gas and Char Byproducts: The proportion of gas and char depends on operational conditions. Gas can be used to power the pyrolysis process, while char may have limited applications unless further processed.
- Impurities and Contaminants: Efficient systems minimize impurities in the end products, ensuring they meet quality standards for downstream use.
-
Environmental and Economic Considerations
- Waste Reduction: Pyrolysis reduces plastic waste by converting it into useful products, contributing to circular economy goals.
- Emissions and Byproducts: Proper control of pyrolysis conditions minimizes harmful emissions and ensures safe disposal of byproducts.
- Cost Efficiency: High efficiency translates to lower operational costs and better economic viability, making pyrolysis an attractive option for waste management.
In summary, the efficiency of plastic pyrolysis depends on a combination of feedstock quality, technology, and operational parameters. By optimizing these factors, the process can achieve high yields of valuable products while minimizing energy consumption and environmental impact. Proper design, operation, and maintenance of pyrolysis systems are crucial for maximizing efficiency and ensuring sustainability.
Summary Table:
Factor | Impact on Efficiency |
---|---|
Feedstock Quality | Clean, dry, and high-organic-content plastics yield more oil and gas. |
Pyrolysis Technology | Reactor type, heating mechanism, and catalyst use affect energy transfer and yield. |
Operational Parameters | Temperature (400°C–600°C), residence time, and pressure optimize product distribution. |
Energy Efficiency | Heat recovery systems and balanced energy input/output improve overall efficiency. |
Product Yield | High-quality oil (70-80% yield) and minimal impurities ensure economic viability. |
Environmental Impact | Reduces waste, minimizes emissions, and supports circular economy goals. |
Ready to optimize your plastic pyrolysis process? Contact our experts today for tailored solutions!