Diamond-like carbon (DLC) coatings are renowned for their exceptional hardness, which is one of their defining characteristics. This hardness, combined with other properties like low friction, chemical inertness, and smooth surface finish, makes DLC coatings highly suitable for wear-protective applications. The hardness of DLC coatings is influenced by the ratio of sp3 (diamond-like) to sp2 (graphite-like) carbon bonds, with higher sp3 content resulting in greater hardness. While DLC coatings are not as hard as pure diamond, they still exhibit hardness values that are significantly higher than many other materials, making them ideal for applications requiring durability and resistance to wear.
Key Points Explained:
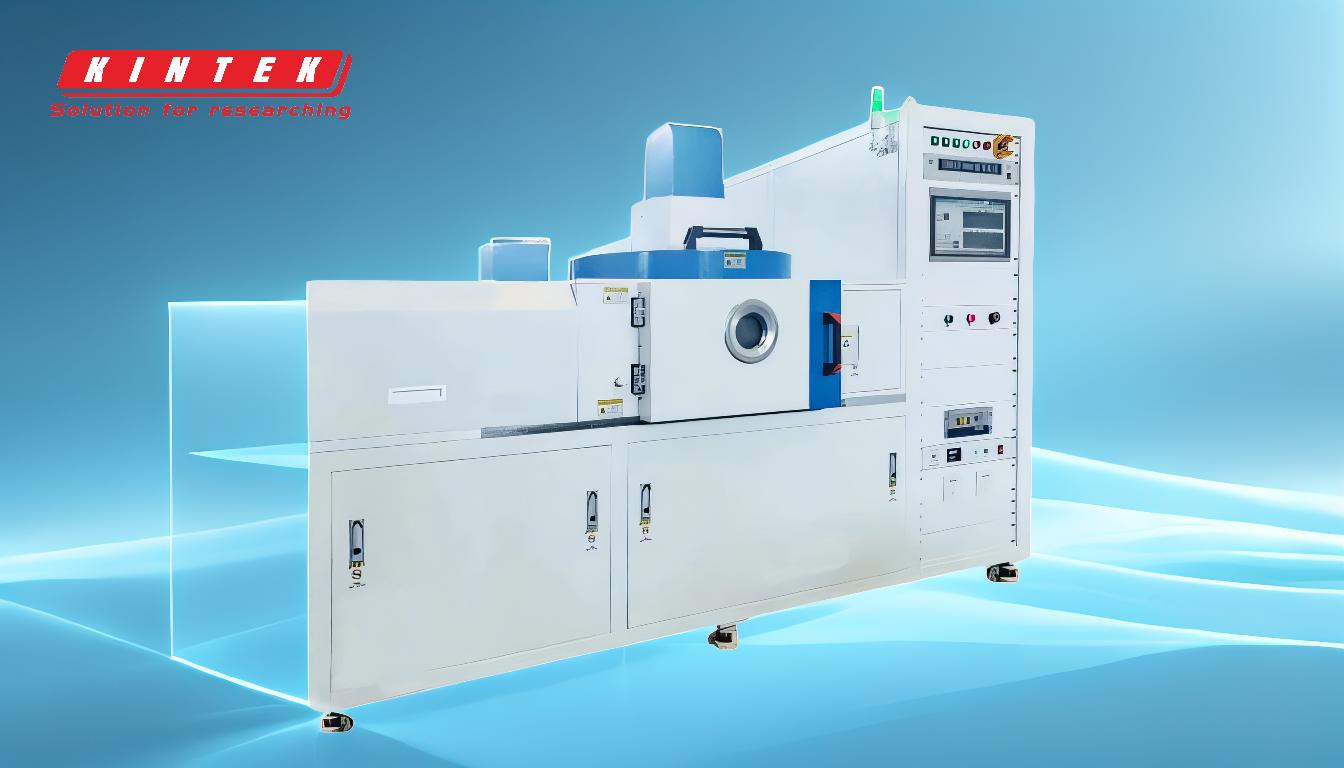
-
Definition and Composition of DLC Coatings:
- DLC coatings are composed of a mixture of sp3 (diamond-like) and sp2 (graphite-like) carbon bonds.
- The ratio of sp3 to sp2 bonds determines the hardness and other mechanical properties of the coating. Higher sp3 content results in greater hardness, making the coating more diamond-like.
-
Hardness of DLC Coatings:
- DLC coatings are known for their high hardness, which is a key factor in their wear resistance.
- The hardness of DLC coatings typically ranges from 10 to 20 GPa (Gigapascals), depending on the deposition process and the specific composition of the coating.
- While not as hard as pure diamond (which has a hardness of around 100 GPa), DLC coatings are significantly harder than many other materials, such as steel or titanium.
-
Comparison to Other Materials:
- Diamond: Pure diamond is the hardest known material, with a hardness of around 100 GPa. DLC coatings, while not as hard as diamond, still exhibit high hardness values due to their diamond-like sp3 bonds.
- Steel: The hardness of steel typically ranges from 1 to 3 GPa, making DLC coatings significantly harder and more wear-resistant.
- Titanium: Titanium has a hardness of around 3 to 4 GPa, again much lower than that of DLC coatings.
-
Factors Influencing Hardness:
- Deposition Process: The method used to deposit the DLC coating (e.g., PVD, CVD) can influence the hardness. Different processes can result in varying ratios of sp3 to sp2 bonds.
- Gas Phase Composition: The composition of the gas phase during deposition can affect the formation of sp3 bonds, thereby influencing the hardness of the coating.
- Substrate Material: The material on which the DLC coating is applied can also affect the final hardness, as the adhesion and stress distribution between the coating and substrate play a role.
-
Applications Benefiting from DLC Hardness:
- Wear-Protective Coatings: The high hardness of DLC coatings makes them ideal for applications where wear resistance is critical, such as in automotive components, cutting tools, and industrial machinery.
- Low Friction Applications: In addition to hardness, DLC coatings have a low coefficient of friction, making them suitable for sliding and rotating components where reduced friction is desired.
- Corrosion Resistance: The chemical inertness of DLC coatings, combined with their hardness, makes them effective in protecting surfaces from corrosion in harsh environments.
-
Limitations and Considerations:
- Optimum Hardness: While high hardness is desirable, there is an optimum level beyond which further increases in hardness may not improve wear resistance and could lead to brittleness or other issues.
- Adhesion: The adhesion of the DLC coating to the substrate is crucial. Poor adhesion can lead to delamination, reducing the effectiveness of the coating despite its high hardness.
- Thickness and Uniformity: The thickness and uniformity of the DLC coating can affect its performance. Thicker coatings may offer better protection but could also be more prone to cracking if not properly applied.
In summary, DLC coatings are highly valued for their hardness, which is a result of their diamond-like sp3 carbon bonds. While not as hard as pure diamond, DLC coatings are significantly harder than many other materials, making them ideal for wear-protective applications. The hardness of DLC coatings can be influenced by various factors, including the deposition process and the composition of the gas phase during coating. Despite their high hardness, it is important to consider other factors such as adhesion and coating thickness to ensure optimal performance in practical applications.
Summary Table:
Aspect | Details |
---|---|
Hardness Range | 10 to 20 GPa (Gigapascals) |
Comparison to Diamond | Not as hard as diamond (100 GPa), but significantly harder than steel/titanium. |
Key Composition | Mixture of sp3 (diamond-like) and sp2 (graphite-like) carbon bonds. |
Influencing Factors | Deposition process, gas phase composition, and substrate material. |
Applications | Wear protection, low friction, and corrosion resistance in harsh environments. |
Limitations | Adhesion, coating thickness, and brittleness at extreme hardness levels. |
Interested in enhancing your materials with DLC coatings? Contact us today to learn more!