E-beam evaporators operate at extremely high temperatures, primarily due to the electron beam used to heat and evaporate the target material. The electron beam itself can reach temperatures of around 3000 °C, which is sufficient to vaporize even high-melting-point materials. This process occurs in a high vacuum environment, ensuring minimal contamination and high-purity thin film deposition. The high temperature and vacuum conditions are critical for achieving rapid deposition rates, excellent adhesion, and uniform coatings. E-beam evaporation is widely used in industries requiring precise and high-quality thin films, such as optics, solar panels, and electronics.
Key Points Explained:
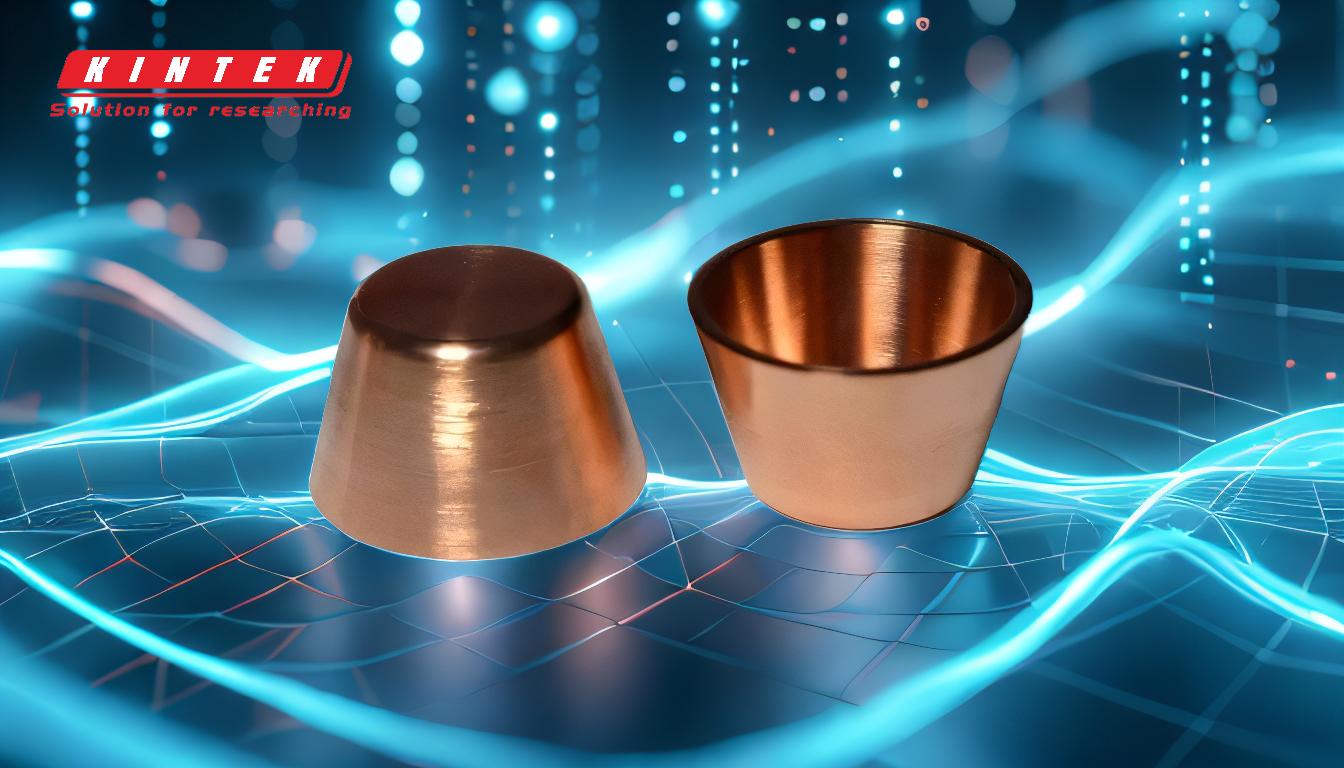
-
Temperature of the Electron Beam:
- The electron beam in an e-beam evaporator typically reaches temperatures of around 3000 °C. This extreme heat is necessary to vaporize the target material, especially for metals and metal oxides with high melting points.
- The high temperature ensures that the material transitions from a solid to a gaseous state, allowing it to be deposited onto the substrate.
-
High Vacuum Environment:
- E-beam evaporation occurs in a high vacuum chamber, which prevents contamination and ensures the purity of the deposited film.
- The vacuum environment also minimizes the interaction between the evaporated material and air molecules, leading to high-quality, dense coatings.
-
Material Compatibility:
- E-beam evaporation is compatible with a wide range of materials, including high-temperature metals (e.g., tungsten, tantalum) and metal oxides (e.g., aluminum oxide, silicon dioxide).
- The process is particularly suitable for materials that require high temperatures to evaporate, making it versatile for various applications.
-
Deposition Rates:
- The deposition rates in e-beam evaporation can range from 0.1 μm/min to 100 μm/min, depending on the material and system configuration.
- These rapid deposition rates make e-beam evaporation highly efficient for industrial applications requiring thick or multi-layer coatings.
-
Advantages of E-Beam Evaporation:
- High-Purity Films: The vacuum environment and precise control of the electron beam minimize contamination, resulting in high-purity films.
- Excellent Adhesion: The high-energy deposition process ensures strong adhesion between the coating and the substrate.
- Uniformity: The use of planetary rotation systems and masks ensures excellent uniformity in the deposited films.
- Material Utilization Efficiency: The process is highly efficient, with minimal material waste.
-
Applications:
- E-beam evaporation is widely used in industries requiring precise and high-quality thin films, such as:
- Optical Coatings: For lenses, mirrors, and filters.
- Solar Panels: For anti-reflective and protective coatings.
- Architectural Glass: For energy-efficient and decorative coatings.
- Electronics: For semiconductor devices and conductive layers.
- E-beam evaporation is widely used in industries requiring precise and high-quality thin films, such as:
-
Process Control:
- The process is controlled using quartz crystal microbalances to monitor and regulate the deposition rate and thickness of the film.
- This ensures that the desired film properties, such as thickness and uniformity, are achieved consistently.
-
Directionality and Throughput:
- The electron beam provides good directionality, allowing for precise control over where the material is deposited.
- High throughput is achieved due to the rapid deposition rates and efficient material utilization, making it suitable for large-scale production.
In summary, the high temperature of the electron beam (around 3000 °C) is a critical factor in the e-beam evaporation process, enabling the vaporization of high-melting-point materials and the deposition of high-quality thin films. The combination of high temperature, vacuum environment, and precise control mechanisms makes e-beam evaporation a versatile and efficient technique for a wide range of industrial applications.
Summary Table:
Key Aspect | Details |
---|---|
Electron Beam Temperature | Reaches up to 3000 °C, enabling vaporization of high-melting-point materials. |
Vacuum Environment | High vacuum ensures minimal contamination and high-purity film deposition. |
Material Compatibility | Works with metals (e.g., tungsten) and metal oxides (e.g., aluminum oxide). |
Deposition Rates | Ranges from 0.1 μm/min to 100 μm/min, ideal for industrial applications. |
Applications | Optics, solar panels, architectural glass, and electronics. |
Ready to achieve high-purity thin films for your applications? Contact us today to learn more about e-beam evaporators!