Test sieve calibration is a critical process to ensure the accuracy and reliability of sieves used in particle size analysis. It involves verifying the size of the sieve openings and ensuring compliance with industry standards such as ISO 3310-1 and ASTM E11. Calibration is essential for both new and used sieves, as it confirms that the sieve performs at the required level of accuracy. The process includes visual inspection, statistical analysis of aperture sizes, and documentation to provide proof of compliance. Proper maintenance and periodic re-verification are also necessary to maintain sieve performance and ensure consistent quality control in material testing.
Key Points Explained:
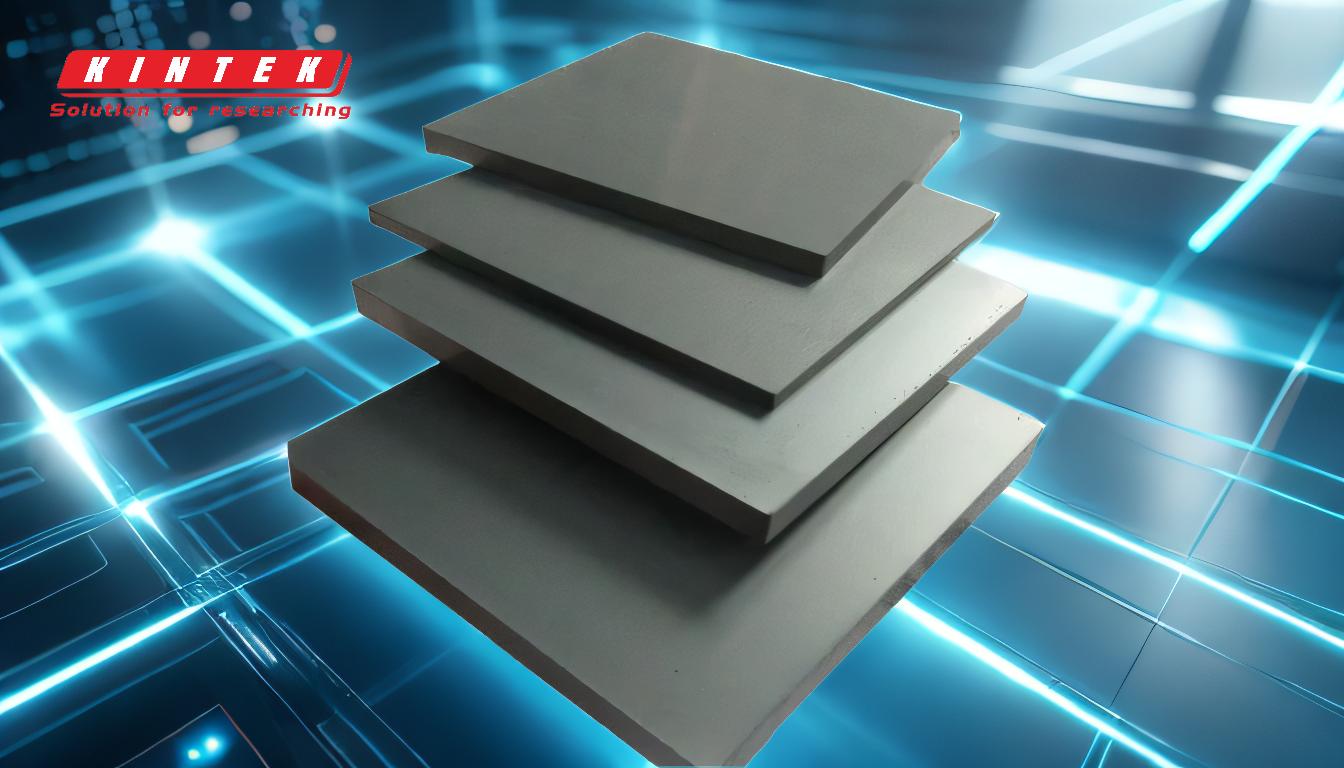
-
Purpose of Test Sieve Calibration:
- Ensures accuracy and reliability of particle size analysis.
- Confirms that sieves meet or exceed industry standards (ISO 3310-1 and ASTM E11).
- Essential for maintaining quality control in material testing.
-
Steps in Test Sieve Calibration:
- Visual Inspection: The first step involves examining the sieve for physical damage such as tears, wavy mesh, or cracked epoxy. This ensures the sieve is in good condition before further testing.
- Aperture Measurement: The size of the sieve openings is measured using precise tools. This step is crucial for determining the sieve's accuracy.
- Statistical Analysis: A certain number of apertures are measured, and statistical forecasting is used to predict overall conformance. This method ensures the sieve meets the required accuracy levels.
- Documentation: The results of the calibration process are documented to provide proof of compliance with industry standards.
-
Certification and Recertification:
- Certification: New sieves must be certified to ensure they meet ISO and ASTM specifications. This involves verifying the size of the sieve openings and providing documented proof of compliance.
- Recertification: Used sieves require periodic recertification to maintain accuracy. This process is similar to the initial certification and is part of an internal quality control/quality assurance program.
-
Importance of Proper Maintenance:
- Ensures sieves remain in top condition for accurate testing.
- Prevents issues such as clogging or damage, which can lead to inaccurate test results.
- Regular maintenance and re-verification are necessary to maintain sieve performance and ensure consistent quality control.
-
Role in Quality Control:
- Test sieves are crucial for ensuring materials meet specific size and quality specifications.
- They help verify that the material's particle size distribution aligns with required standards, which is essential for consistent product quality.
- Accurate sieves ensure that the final product performs as expected in its intended application.
-
Standards and Classifications:
- ASTM E11 and ISO 3310-1 classify test sieves into three levels of accuracy based on the statistical analysis of aperture sizes.
- These standards provide guidelines for the calibration and certification of test sieves, ensuring they meet the required performance levels.
By following these steps and maintaining proper calibration and certification, test sieves can provide accurate and reliable results, ensuring high-quality material testing and consistent product performance.
Summary Table:
Key Aspect | Details |
---|---|
Purpose | Ensures accuracy, reliability, and compliance with ISO 3310-1 and ASTM E11. |
Steps | Visual inspection, aperture measurement, statistical analysis, documentation. |
Certification | Required for new sieves; recertification for used sieves to maintain accuracy. |
Maintenance | Regular upkeep prevents clogging, damage, and ensures consistent performance. |
Role in Quality Control | Verifies particle size distribution, ensuring material meets specifications. |
Standards | ASTM E11 and ISO 3310-1 define accuracy levels for test sieves. |
Ensure your test sieves meet industry standards—contact us today for expert calibration services!