Biochar is produced through a process called pyrolysis, where organic biomass is heated in the absence of oxygen at temperatures ranging from 300-900°C. This thermal decomposition breaks down the biomass into its constituent parts, such as cellulose, hemicellulose, and lignin, resulting in the formation of biochar. The process not only produces biochar but also yields other byproducts like syngas and bio-oil. Once produced, biochar is often mixed with fertilizers and returned to the soil, where it serves as a carbon storage medium and improves soil health by enhancing nutrient retention and microbial activity.
Key Points Explained:
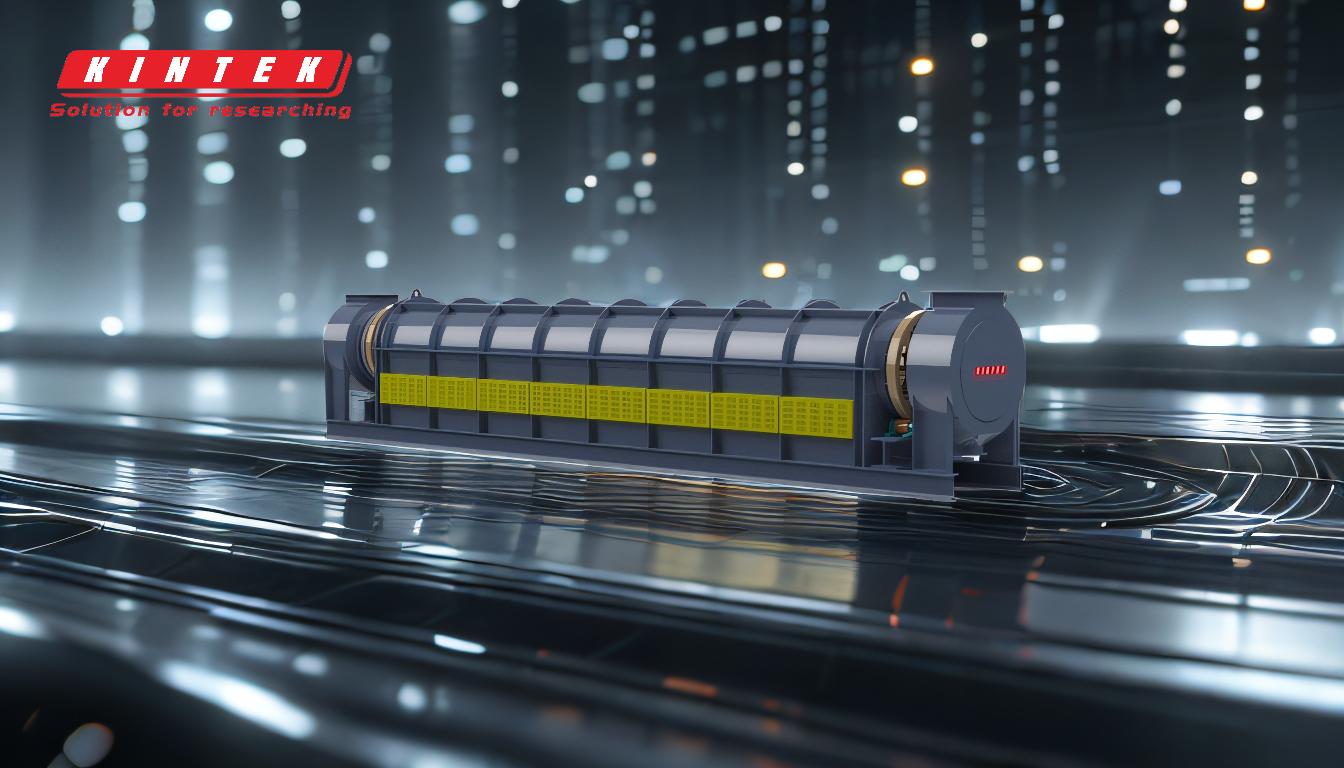
-
Pyrolysis Process:
- Pyrolysis is the core method for producing biochar. It involves heating biomass in an oxygen-free environment to prevent combustion.
- The temperature range for pyrolysis is typically between 300-900°C, depending on the desired properties of the biochar.
- At these high temperatures, the biomass undergoes thermal decomposition, breaking down into simpler compounds.
-
Biomass Decomposition:
- The biomass used in pyrolysis can include agricultural waste, wood chips, or other organic materials.
- During pyrolysis, the biomass decomposes into its main components: cellulose, hemicellulose, and lignin.
- This decomposition results in the formation of biochar, along with other byproducts like syngas and bio-oil.
-
Biochar Characteristics:
- Biochar is a stable, carbon-rich material that can persist in soil for hundreds to thousands of years.
- It has a porous structure, which enhances its ability to retain water and nutrients in the soil.
- The properties of biochar, such as surface area and porosity, can be influenced by the pyrolysis temperature and the type of biomass used.
-
Soil Amendment:
- Once produced, biochar is often mixed with fertilizers and applied to soil.
- It improves soil fertility by increasing nutrient retention and promoting microbial activity.
- Biochar also helps in carbon sequestration, making it a valuable tool in combating climate change.
-
Environmental Benefits:
- The production and use of biochar contribute to reducing greenhouse gas emissions by storing carbon in the soil.
- It helps in recycling agricultural waste, reducing the need for landfill space and minimizing pollution.
- Biochar can also improve soil health, leading to increased crop yields and reduced need for chemical fertilizers.
By understanding the pyrolysis process and the benefits of biochar, we can appreciate its role in sustainable agriculture and environmental conservation.
Summary Table:
Aspect | Details |
---|---|
Pyrolysis Process | Heating biomass at 300-900°C in an oxygen-free environment. |
Biomass Decomposition | Breaks down into cellulose, hemicellulose, and lignin, producing biochar. |
Biochar Characteristics | Stable, carbon-rich, porous structure; enhances soil water and nutrient retention. |
Soil Amendment | Mixed with fertilizers; improves nutrient retention and microbial activity. |
Environmental Benefits | Reduces greenhouse gas emissions, recycles waste, and boosts crop yields. |
Discover how biochar can transform your agricultural practices—contact our experts today!