Diamond-like coatings (DLC) are applied using advanced deposition techniques, primarily Chemical Vapor Deposition (CVD) and Physical Vapor Deposition (PVD). CVD methods, such as microwave plasma CVD (MPCVD), DC arc plasma spray CVD (DAPCVD), and hot wire CVD (HFCVD), involve breaking down gas molecules (e.g., hydrogen and methane) in a chamber to deposit a pure diamond film on the tool surface. PVD, on the other hand, involves evaporating a source material and condensing it onto the tool to form a thin DLC layer. These processes require precise control of temperature, gas composition, and energy sources to achieve high-quality coatings.
Key Points Explained:
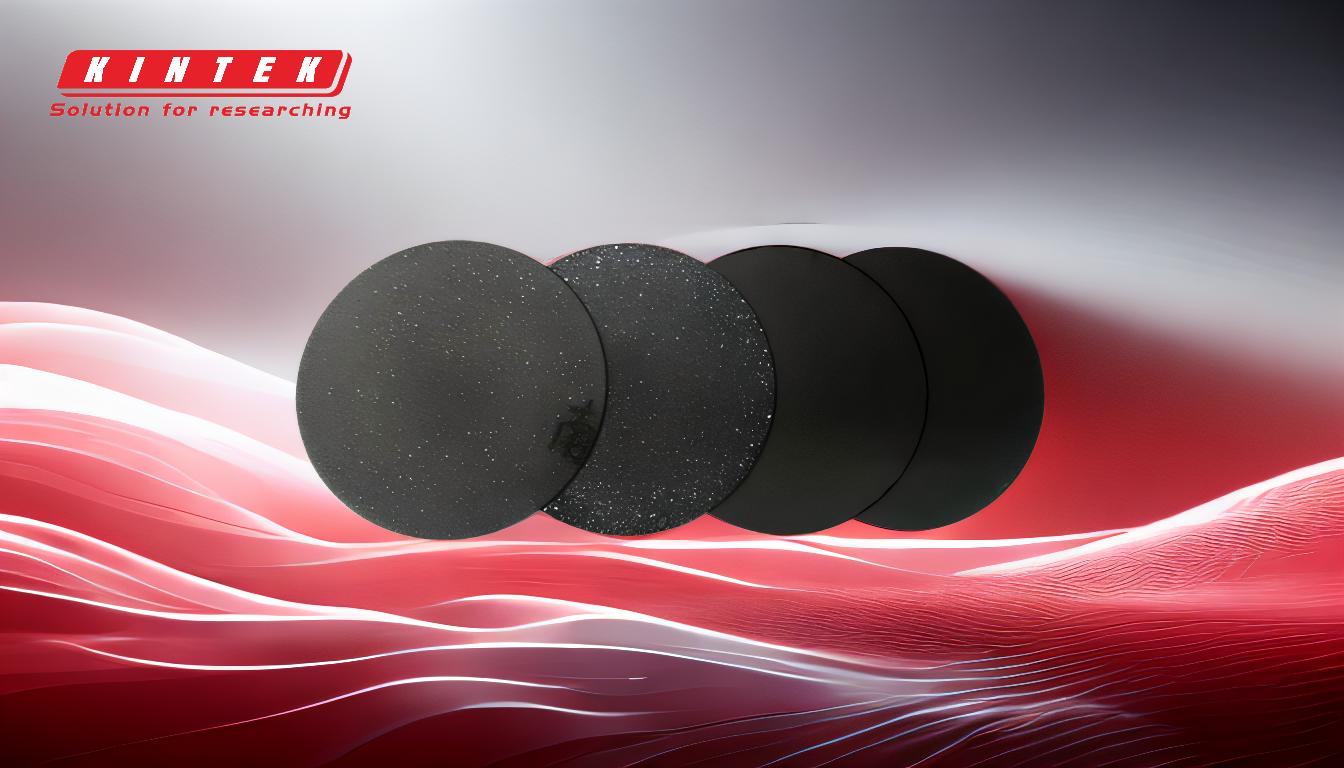
-
Chemical Vapor Deposition (CVD) Methods:
- Microwave Plasma CVD (MPCVD): This technique uses microwave energy to generate a plasma that breaks down gas molecules, such as hydrogen and methane, into reactive carbon atoms. These atoms deposit onto the substrate, forming a diamond-like coating. MPCVD is known for producing high-quality, uniform coatings.
- DC Arc Plasma Spray CVD (DAPCVD): In this method, a direct current arc is used to create a high-energy plasma. The plasma decomposes the gas mixture, and the resulting carbon atoms deposit onto the tool surface. DAPCVD is effective for coating complex geometries and large surfaces.
- Hot Wire CVD (HFCVD): This process involves heating tungsten wires to over 2,300°C to decompose the gas mixture. The activated carbon atoms then deposit onto the substrate, forming a diamond film. HFCVD is suitable for high-temperature applications and provides excellent adhesion.
-
Physical Vapor Deposition (PVD) Method:
- PVD for DLC Coatings: PVD involves evaporating a source material in a vacuum chamber and allowing it to condense onto the tool surface. This method is used to deposit Diamond-Like Carbon (DLC) coatings, which are amorphous and contain a mix of sp2 and sp3 carbon bonds. PVD is ideal for creating thin, hard coatings (0.5 to 2.5 microns thick) with low friction and high wear resistance.
-
Process Parameters and Conditions:
- Gas Composition: The choice of gases, typically hydrogen and methane, is critical for achieving the desired carbon deposition. The ratio of these gases affects the quality and properties of the coating.
- Temperature Control: High temperatures (over 750°C) are required to activate the gas molecules and ensure proper deposition. Precise temperature control is essential to prevent defects and ensure uniform coating.
- Energy Sources: Different energy sources, such as microwaves, DC arcs, or heated filaments, are used to generate the plasma or heat required for the deposition process. The choice of energy source depends on the specific CVD method and the desired coating properties.
-
Applications and Benefits:
- Tool Coating: Diamond-like coatings are widely used to enhance the performance of cutting tools, such as drills and end mills, by providing superior hardness, wear resistance, and low friction.
- Industrial Applications: These coatings are also used in various industrial applications, including automotive components, medical devices, and electronics, where durability and performance are critical.
By understanding these key points, purchasers of equipment and consumables can make informed decisions about the appropriate coating method for their specific needs, ensuring optimal performance and longevity of their tools and components.
Summary Table:
Method | Key Features | Applications |
---|---|---|
MPCVD | Uses microwave energy for uniform, high-quality coatings | Cutting tools, electronics, and high-precision components |
DAPCVD | DC arc plasma for coating complex geometries and large surfaces | Automotive components, industrial tools, and large-scale applications |
HFCVD | Heated tungsten wires for high-temperature applications and excellent adhesion | High-temperature tools, medical devices, and durable coatings |
PVD | Evaporates and condenses source material for thin, hard, low-friction coatings | Tools requiring wear resistance, low friction, and thin coatings (0.5-2.5 µm) |
Discover the best DLC coating solution for your needs—contact our experts today!