Plasma-Enhanced Chemical Vapor Deposition (PECVD) differs significantly from traditional Chemical Vapor Deposition (CVD) in terms of process mechanics, temperature requirements, and application suitability. PECVD leverages plasma to enhance the deposition process, enabling faster growth rates, better edge coverage, and more uniform films. Unlike traditional CVD, which relies solely on thermal energy, PECVD operates at much lower temperatures, making it ideal for temperature-sensitive substrates. Additionally, PECVD does not require ion bombardment, ensuring higher reproducibility and suitability for high-quality applications. These differences make PECVD a preferred choice for advanced semiconductor and microelectronics manufacturing.
Key Points Explained:
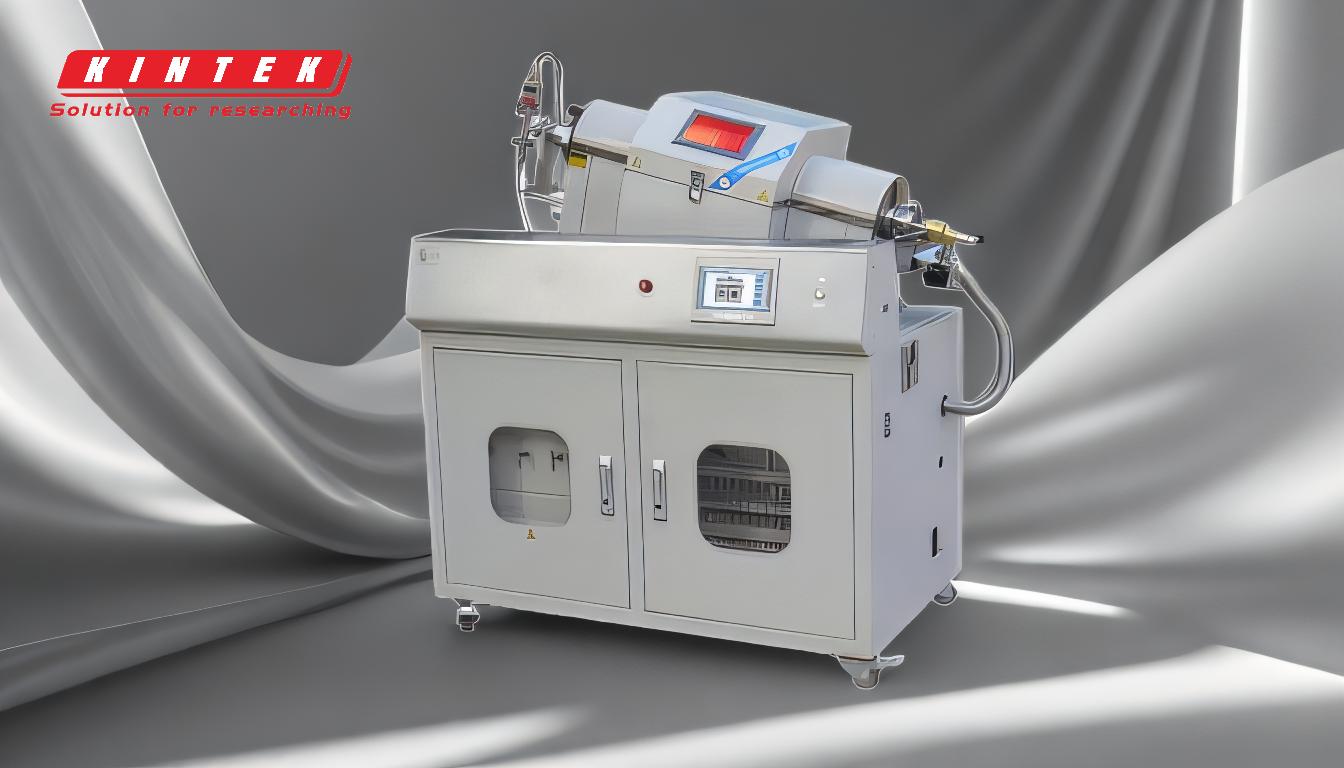
-
Mechanism of Deposition:
- CVD: Traditional CVD relies on thermal energy to drive chemical reactions between gaseous precursors and the substrate, forming a solid film. This process typically requires high temperatures (600°C to 800°C).
- PECVD: PECVD introduces plasma into the process, which provides additional energy to the reactants. This allows the deposition to occur at much lower temperatures (room temperature to 350°C), making it suitable for substrates that cannot withstand high heat.
-
Temperature Requirements:
- CVD: Operates at high temperatures, which can limit its use with temperature-sensitive materials.
- PECVD: Operates at significantly lower temperatures, enabling the coating of delicate substrates such as polymers and certain metals without thermal degradation.
-
Deposition Rate and Uniformity:
- CVD: Generally has slower deposition rates and may struggle with achieving uniform films, especially on complex geometries.
- PECVD: Offers faster deposition rates and superior film uniformity, even on intricate structures, due to the enhanced reactivity provided by the plasma.
-
Edge Coverage and Film Quality:
- CVD: May exhibit challenges in achieving consistent edge coverage and high-quality films, particularly on non-planar surfaces.
- PECVD: Excels in edge coverage and produces films with better uniformity and fewer defects, making it ideal for high-precision applications.
-
Reproducibility and Suitability:
- CVD: While reproducible, the high-temperature requirements can introduce variability in certain applications.
- PECVD: Offers higher reproducibility and is better suited for high-quality applications, such as semiconductor manufacturing, where precision and consistency are critical.
-
Applications:
- CVD: Commonly used in applications requiring high-temperature stability, such as coatings for cutting tools and wear-resistant surfaces.
- PECVD: Preferred for advanced applications in microelectronics, optoelectronics, and coatings on temperature-sensitive materials.
In summary, PECVD's use of plasma and lower operating temperatures provides distinct advantages over traditional CVD, including faster deposition, better uniformity, and compatibility with a wider range of substrates. These characteristics make PECVD a versatile and essential technique in modern manufacturing and research.
Summary Table:
Aspect | CVD | PECVD |
---|---|---|
Mechanism | Relies on thermal energy for deposition. | Uses plasma to enhance deposition at lower temperatures. |
Temperature | High (600°C to 800°C). | Low (room temperature to 350°C). |
Deposition Rate | Slower. | Faster. |
Uniformity | May struggle with complex geometries. | Superior uniformity, even on intricate structures. |
Edge Coverage | Challenges with non-planar surfaces. | Excellent edge coverage and fewer defects. |
Reproducibility | High but variable due to temperature constraints. | Higher reproducibility for precision applications. |
Applications | High-temperature stability (e.g., cutting tools). | Advanced microelectronics, optoelectronics, and temperature-sensitive materials. |
Learn how PECVD can revolutionize your manufacturing process—contact us today for expert guidance!