PVD (Physical Vapor Deposition) coating is a sophisticated and environmentally friendly process used to apply thin, durable, and high-performance coatings to various substrates. It involves the vaporization of a solid material in a vacuum environment, followed by the deposition of the vaporized material onto a substrate to form a thin film. The process is widely used in industries such as aerospace, automotive, and electronics due to its ability to produce coatings with excellent mechanical, chemical, and optical properties. Below is a detailed explanation of how PVD coating is done, broken down into key steps and considerations.
Key Points Explained:
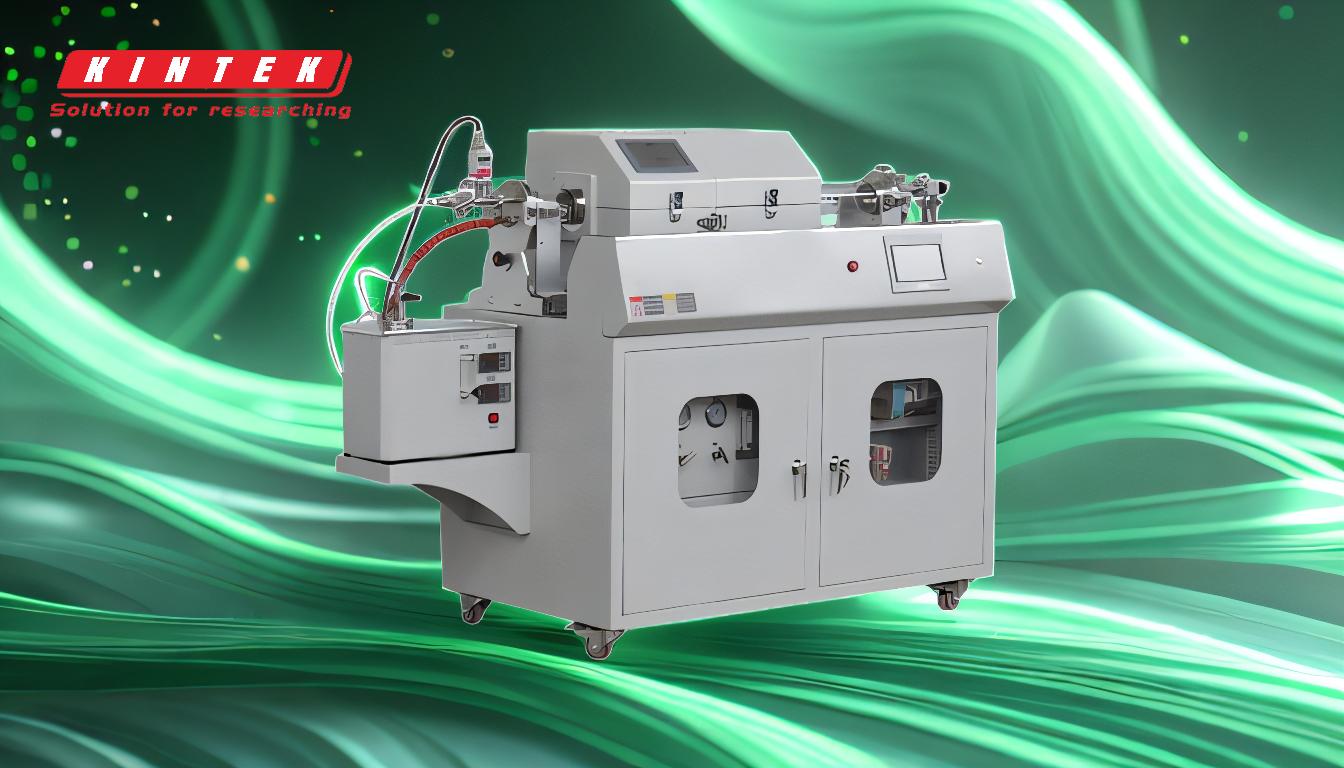
-
Preparation of the Substrate
- Cleaning: The substrate (the material to be coated) must be thoroughly cleaned to remove any contaminants such as oils, dust, or oxides. This ensures proper adhesion of the coating.
- Pretreatment: Surface treatments like polishing, etching, or applying adhesion-promoting layers may be performed to enhance the bonding between the substrate and the coating.
-
Setting Up the Vacuum Chamber
- Loading the Target Material: The material to be vaporized (e.g., titanium, zirconium, or chromium) is placed in the vacuum chamber as the target.
- Evacuating the Chamber: The chamber is evacuated to create a high-vacuum environment, typically using pumps to remove air and other gases. This prevents contamination and allows for precise control of the coating process.
-
Vaporization of the Target Material
- Ablation or Sputtering: The target material is vaporized using high-energy sources such as electron beams, ion bombardment, or arc discharge. This step dislodges atoms from the target, converting them into a vapor phase.
- Transportation: The vaporized atoms are transported through the vacuum chamber toward the substrate. Inert gases like argon may be introduced to facilitate this process.
-
Reaction (Optional)
- Chemical Reaction: If reactive gases like nitrogen or oxygen are introduced into the chamber, the vaporized metal atoms react with these gases to form compounds such as nitrides, oxides, or carbides. This step determines the final properties of the coating, such as hardness, color, and chemical resistance.
-
Deposition of the Coating
- Condensation: The vaporized atoms or compounds condense onto the substrate, forming a thin, uniform layer. The thickness of the coating is typically in the micron range.
- Adhesion: The coating bonds strongly to the substrate, often interpenetrating with the underlying material to prevent flaking or chipping.
-
Post-Processing and Quality Control
- Purging: The chamber is purged with inert gas to remove any residual vapors and ensure a clean environment.
- Finishing: Additional treatments, such as polishing or heat treatment, may be applied to enhance the coating's appearance or performance.
- Inspection: The coated substrate undergoes quality control checks to ensure the coating meets specifications for thickness, adhesion, and other properties.
Additional Considerations:
- Environmental Benefits: PVD coating is considered environmentally friendly because it produces minimal waste and does not involve harmful chemicals.
- Versatility: The process can be tailored to produce coatings with specific properties, such as wear resistance, corrosion resistance, or decorative finishes.
- Applications: PVD coatings are used in a wide range of applications, including cutting tools, medical devices, and consumer electronics.
By following these steps, the PVD coating process creates highly durable and functional coatings that meet the demanding requirements of modern industries.
Summary Table:
Step | Description |
---|---|
1. Substrate Preparation | Clean and pretreat the substrate to ensure proper adhesion of the coating. |
2. Vacuum Chamber Setup | Load the target material and evacuate the chamber to create a high-vacuum environment. |
3. Vaporization | Vaporize the target material using high-energy sources like electron beams. |
4. Reaction (Optional) | Introduce reactive gases to form compounds like nitrides or oxides. |
5. Deposition | Condense vaporized atoms onto the substrate to form a thin, uniform layer. |
6. Post-Processing | Purge the chamber, apply finishing treatments, and inspect the final coating. |
Ready to enhance your products with PVD coatings? Contact our experts today to learn more!