Pyrolysis oil, also known as bio-crude or bio-oil, is produced through the thermal decomposition of biomass or plastic waste in the absence of oxygen. The process involves heating the feedstock at high temperatures (typically 450°C to 900°C) in a reactor, followed by rapid cooling to condense the vapors into a liquid form. This liquid, pyrolysis oil, is distinct from petroleum due to its high oxygen content and tar-like consistency. The process also yields by-products such as biochar, syngas, and non-condensable gases, which can be recycled or utilized for energy. The production of pyrolysis oil is a multi-step process that includes feedstock preparation, pyrolysis, condensation, and sometimes further refining through distillation to improve the quality of the oil.
Key Points Explained:
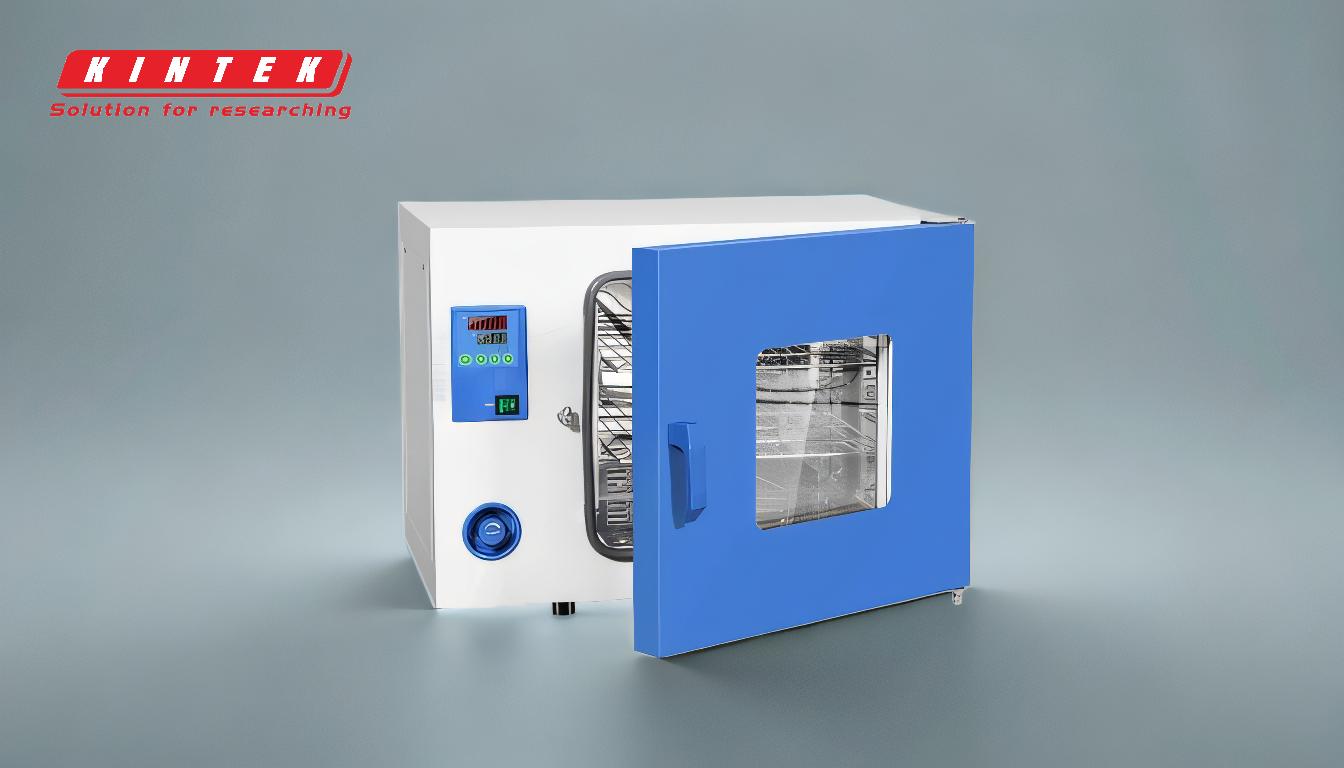
-
Feedstock Preparation:
- Biomass or Plastic Waste: The process begins with the collection and preparation of the feedstock, which can be dry biomass (e.g., wood, agricultural residues) or plastic waste.
- Pre-Treatment: The feedstock is dried to remove moisture and may be ground to a specific size to ensure uniform heating during pyrolysis. Impurities are removed to prevent contamination of the final product.
-
Pyrolysis Process:
- Heating in the Absence of Oxygen: The prepared feedstock is fed into a pyrolysis reactor, where it is heated to temperatures ranging from 450°C to 900°C. The absence of oxygen prevents combustion, allowing thermal decomposition (pyrolysis) to occur.
- Decomposition: At these high temperatures, the feedstock breaks down into smaller molecules, producing a mixture of gases, vapors, and solid residues.
-
Condensation and Separation:
- Rapid Cooling: The hot vapors produced during pyrolysis are rapidly cooled in a condenser, causing them to liquefy into pyrolysis oil.
- Separation of By-Products: The process also yields biochar (a solid residue that settles at the bottom of the reactor) and non-condensable gases (syngas), which can be recycled back into the system to provide heat for the pyrolysis process.
-
Refining and Distillation:
- Distillation: Pyrolysis oil can be further refined through distillation, where it is heated to separate its components based on their boiling points. This process involves vaporizing the oil and then condensing the vapors to produce a cleaner, more stable fuel.
- Purification: The distilled oil undergoes additional steps such as degreasing, bleaching, and purification to remove impurities and improve its quality, resulting in a product that resembles non-standard diesel.
-
Recycling and Environmental Considerations:
- Recycling of Non-Condensable Gases: Gases like methane, ethane, propane, and butane that do not condense are recycled back into the combustion chamber to provide heat, making the process more energy-efficient.
- Emission Control: The process includes systems for treating smoke and exhaust gases to minimize environmental pollution, ensuring that the production of pyrolysis oil is as eco-friendly as possible.
-
Applications of Pyrolysis Oil:
- Fuel Source: Pyrolysis oil can be used as a substitute for petroleum in various applications, including heating, electricity generation, and as a feedstock for further chemical processing.
- Chemical Feedstock: Due to its high oxygen content, pyrolysis oil can be chemically modified to produce a range of valuable chemicals and fuels.
In summary, pyrolysis oil production is a complex but efficient process that converts biomass or plastic waste into a valuable liquid fuel. The process involves careful preparation of the feedstock, controlled thermal decomposition, rapid condensation, and optional refining to produce a high-quality product. By-products such as biochar and syngas are also utilized, making the process sustainable and environmentally friendly.
Summary Table:
Step | Description |
---|---|
Feedstock Preparation | Biomass or plastic waste is dried, ground, and purified to ensure uniform heating. |
Pyrolysis Process | Feedstock is heated at 450°C–900°C in the absence of oxygen for thermal decomposition. |
Condensation | Vapors are rapidly cooled to produce pyrolysis oil, separating biochar and syngas. |
Refining | Oil is distilled and purified to improve quality, resembling non-standard diesel. |
Recycling | Non-condensable gases are recycled to provide heat, enhancing energy efficiency. |
Applications | Used as fuel for heating, electricity, and chemical feedstock for further processing. |
Discover how pyrolysis oil can revolutionize your energy solutions—contact us today to learn more!