Torrefaction and pyrolysis biochar are both thermal decomposition processes applied to biomass, but they differ significantly in temperature, process duration, and end-product characteristics. Torrefaction occurs at lower temperatures (200-300°C) over extended periods, retaining most of the biomass's mass and energy while producing a hydrophobic, friable material. Pyrolysis biochar, on the other hand, involves higher temperatures (typically 400-700°C) and faster heating rates, resulting in a more carbon-rich, stable product with higher porosity. While torrefaction focuses on energy retention and storage stability, pyrolysis biochar emphasizes carbon sequestration and soil amendment properties.
Key Points Explained:
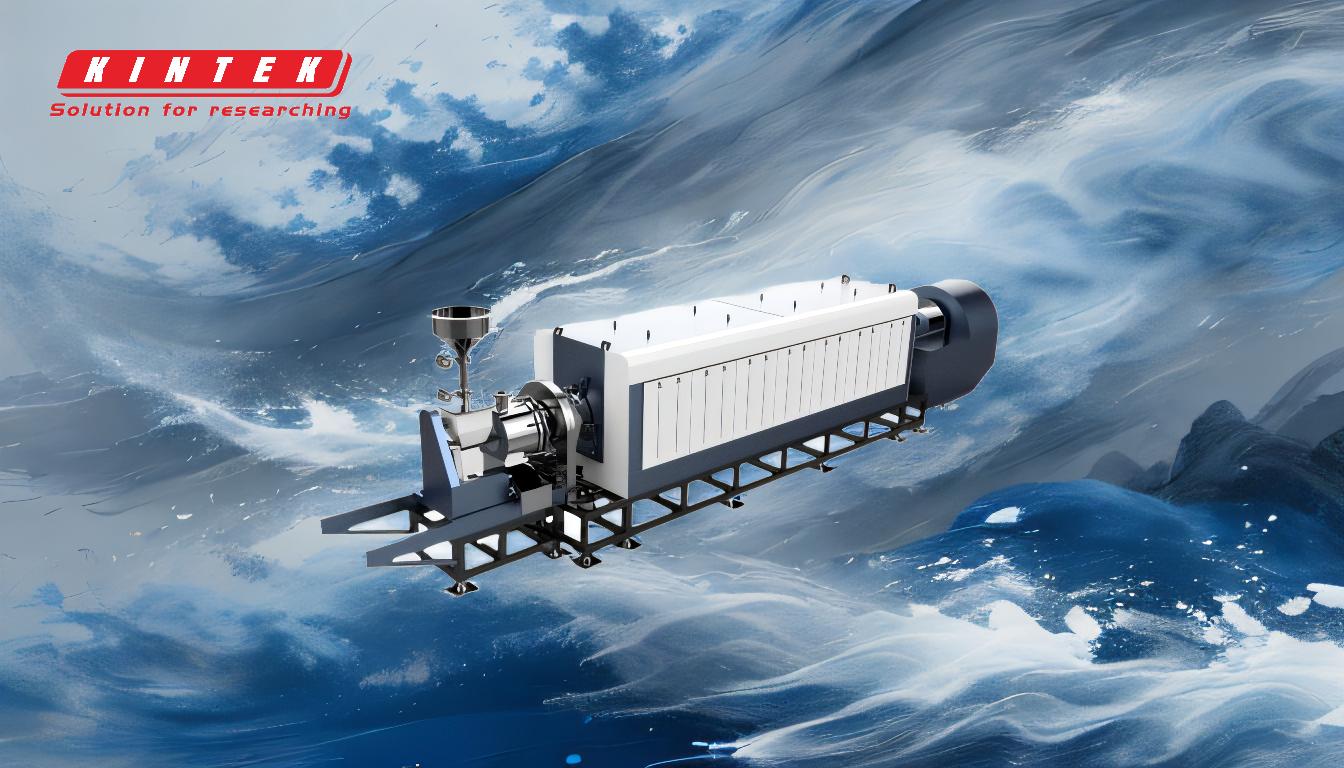
-
Temperature Range:
- Torrefaction: Operates at 200-300°C, ensuring partial decomposition of biomass while retaining a significant portion of its original structure.
- Pyrolysis Biochar: Occurs at higher temperatures, typically 400-700°C, leading to more complete decomposition and a higher carbon content.
-
Process Duration:
- Torrefaction: A slow process, often taking hours to days, with heating rates below 50°C/min. This gradual heating preserves the biomass's rigid carbon structure.
- Pyrolysis Biochar: Faster heating rates and shorter durations, often minutes to hours, resulting in rapid decomposition and a more carbonized product.
-
Mass and Energy Retention:
- Torrefaction: Retains approximately 70% of the mass and 90% of the energy content of the original biomass, making it energy-efficient.
- Pyrolysis Biochar: Yields a lower mass retention (typically 20-50%) but produces a highly stable carbon-rich material suitable for long-term carbon sequestration.
-
End-Product Characteristics:
- Torrefaction: Produces a hydrophobic, friable solid that is easy to store and transport. It is often used as a coal substitute in energy applications.
- Pyrolysis Biochar: Yields a porous, stable carbon material with high surface area, ideal for soil amendment, carbon sequestration, and filtration applications.
-
Volatile Content:
- Torrefaction: Retains a significant amount of volatiles in the product, which can limit its autothermal operation but enhances its energy content.
- Pyrolysis Biochar: Releases most volatiles during the process, resulting in a more stable, carbon-dense product.
-
Applications:
- Torrefaction: Primarily used for producing energy-dense, hydrophobic biomass pellets for co-firing with coal or as a standalone fuel.
- Pyrolysis Biochar: Used in agriculture for soil improvement, carbon sequestration, and as a filtration medium in environmental applications.
By understanding these distinctions, purchasers of equipment or consumables can make informed decisions about which process aligns with their specific needs, whether for energy production, carbon sequestration, or soil enhancement.
Summary Table:
Aspect | Torrefaction | Pyrolysis Biochar |
---|---|---|
Temperature Range | 200-300°C | 400-700°C |
Process Duration | Hours to days | Minutes to hours |
Mass Retention | ~70% | 20-50% |
Energy Retention | ~90% | Lower |
End-Product | Hydrophobic, friable solid | Porous, stable carbon material |
Volatile Content | Retains significant volatiles | Releases most volatiles |
Applications | Energy production, coal substitute | Soil amendment, carbon sequestration |
Need help choosing the right biomass processing method? Contact our experts today for tailored advice!