The duration of fast pyrolysis is relatively short, typically ranging from a few seconds to a few minutes. This process involves heating biomass at high rates (10–200°C/s) and moderate temperatures (400–600°C) in an inert atmosphere, with a short residence time of approximately 0.5–10 seconds. The primary goal of fast pyrolysis is to produce bio-oil, with yields as high as 50–70 wt% on a dry biomass basis. The exact duration can vary depending on factors such as the type of biomass, desired end products, and specific process conditions. In contrast, slow pyrolysis, which is designed for producing biochar, can take several hours to complete.
Key Points Explained:
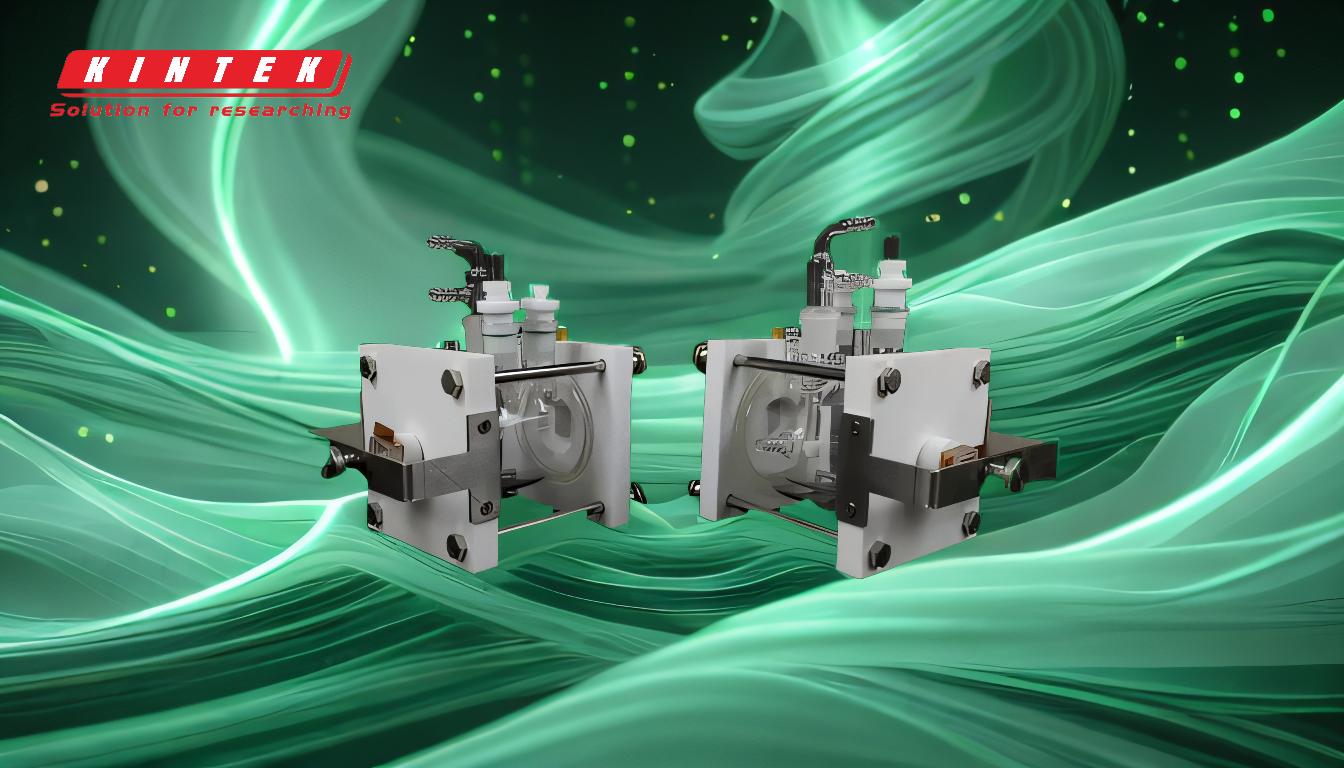
-
Definition of Fast Pyrolysis:
- Fast pyrolysis is a thermal decomposition process that occurs in the absence of oxygen.
- It is characterized by high heating rates (10–200°C/s) and moderate temperatures (400–600°C).
- The process is designed to maximize the production of bio-oil, with yields typically ranging from 50–70 wt% on a dry biomass basis.
-
Residence Time:
- The residence time for fast pyrolysis is very short, typically ranging from 0.5 to 10 seconds.
- This short duration is crucial for achieving high bio-oil yields, as it minimizes the time for secondary reactions that could lead to the formation of unwanted by-products.
-
Factors Influencing Duration:
- Type of Biomass: Different biomass materials have varying thermal properties and compositions, which can affect the duration and efficiency of the pyrolysis process.
- Desired End Products: The specific products desired (e.g., bio-oil, biogas, biochar) can influence the duration and conditions of the pyrolysis process.
- Process Conditions: Parameters such as temperature, heating rate, and reactor design can significantly impact the duration and outcome of the pyrolysis process.
-
Comparison with Slow Pyrolysis:
- Duration: Slow pyrolysis takes significantly longer, often several hours, compared to the seconds or minutes required for fast pyrolysis.
- End Products: Slow pyrolysis is typically aimed at producing biochar, whereas fast pyrolysis focuses on maximizing bio-oil production.
- Heating Rates: Slow pyrolysis involves much lower heating rates compared to the rapid heating rates used in fast pyrolysis.
-
Practical Considerations:
- Reactor Design: The design of the pyrolysis reactor plays a critical role in achieving the desired short residence times and high heating rates.
- Cooling and Discharge: While the pyrolysis reaction itself is brief, additional time is required for cooling and discharging the products, especially in batch processes. For example, a small pyrolysis machine may take about 10 hours for the reaction, followed by 7 hours of cooling and 2 hours for discharging, totaling approximately 19 hours for a complete batch.
-
Applications and Implications:
- Bio-oil Production: Fast pyrolysis is considered the most promising method for generating liquid fuels like bio-oil, which can be used as a renewable energy source.
- Economic Viability: The short duration of fast pyrolysis makes it more economically viable for large-scale bio-oil production, as it allows for continuous processing and higher throughput.
In summary, fast pyrolysis is a rapid process that typically takes only a few seconds to a few minutes, depending on the specific conditions and desired outcomes. The short residence time and high heating rates are key to maximizing bio-oil production, making fast pyrolysis a highly efficient method for converting biomass into valuable liquid fuels.
Summary Table:
Aspect | Details |
---|---|
Duration | A few seconds to a few minutes |
Heating Rate | 10–200°C/s |
Temperature Range | 400–600°C |
Residence Time | 0.5–10 seconds |
Primary Product | Bio-oil (50–70 wt% yield) |
Key Influencing Factors | Biomass type, desired end products, process conditions |
Comparison with Slow Pyrolysis | Shorter duration, higher heating rates, and focus on bio-oil production |
Interested in optimizing your biomass conversion process? Contact our experts today for tailored solutions!