The lifespan of PVD (Physical Vapor Deposition) coating on a watch can vary significantly, typically ranging from 10 years to potentially hundreds of years, depending on several key factors. These include the type of substrate, the thickness of the coating, the bond strength between the coating and the substrate, and the conditions to which the watch is exposed. Proper application and maintenance are crucial for maximizing the durability of PVD coatings, which are known for their superior resistance to corrosion, scratches, and wear compared to traditional finishes.
Key Points Explained:
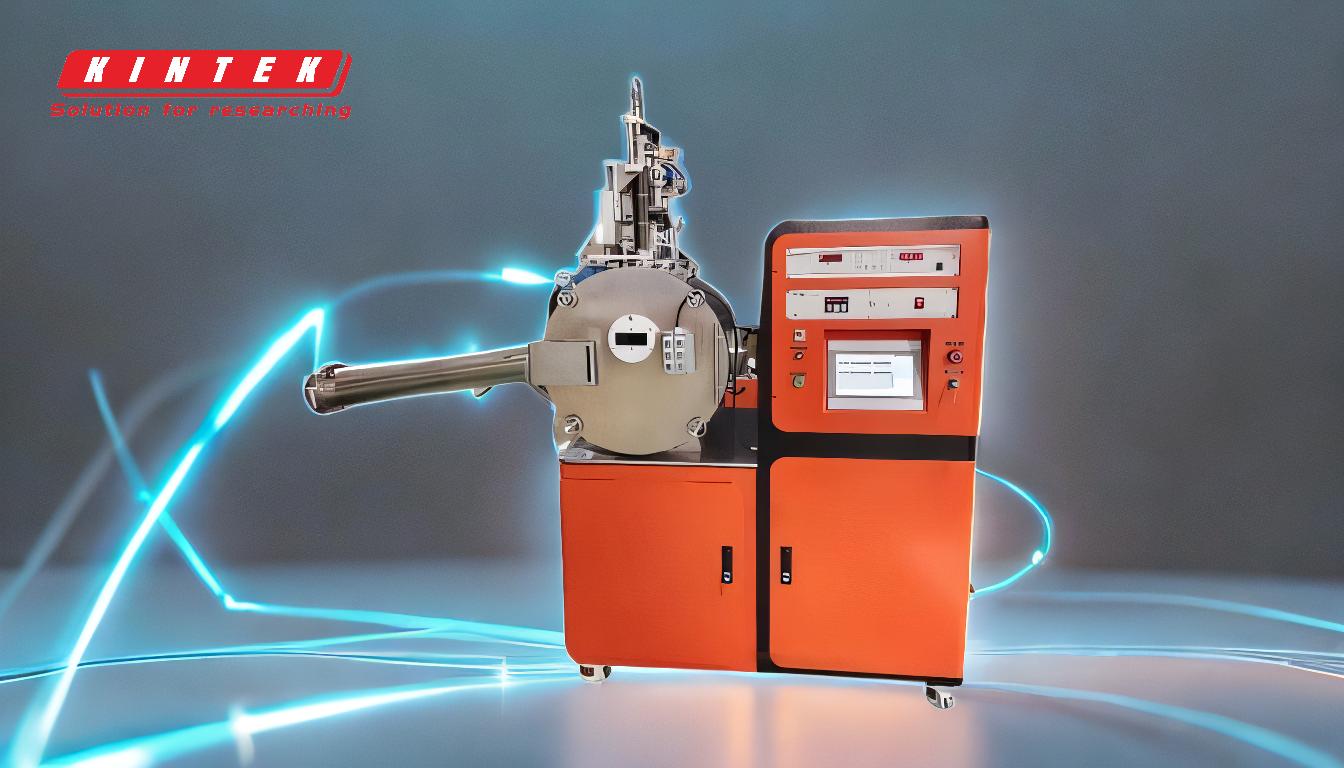
-
General Lifespan of PVD Coating:
- Typical Range: PVD coatings on watches generally last between 10 years to hundreds of years.
- Durability: PVD is considered the most durable coating available, offering superior resistance to corrosion and scratches.
-
Factors Influencing Lifespan:
- Substrate Type: The material of the watch (e.g., stainless steel, titanium) affects how well the PVD coating adheres and lasts.
- Coating Thickness: Thicker coatings tend to last longer as they provide more material to wear down before the substrate is exposed.
- Bond Strength: The strength of the bond between the coating and the substrate is crucial; stronger bonds result in longer-lasting coatings.
- Environmental Exposure: Exposure to high temperatures, chemicals, and physical wear can reduce the lifespan of PVD coatings.
-
Application and Maintenance:
- Proper Application: Correctly applied PVD coatings, following industry standards, ensure maximum durability and longevity.
- Maintenance Practices: Regular cleaning and avoiding harsh chemicals can help maintain the integrity of the PVD coating over time.
-
Comparative Durability:
- Superior to Traditional Finishes: PVD coatings outlast traditional finishes like electroplating due to their hardness and resistance properties.
- Market Position: Recognized as the most durable coating in the market, PVD is preferred for high-end watches and jewelry.
-
Practical Considerations for Watch Owners:
- Usage Patterns: Watches subjected to daily wear and tear may experience faster degradation of the PVD coating.
- Care Instructions: Following manufacturer guidelines for care and maintenance can significantly extend the life of the PVD coating.
Understanding these factors can help watch owners and buyers make informed decisions about the care and selection of PVD-coated watches, ensuring they enjoy the aesthetic and protective benefits of the coating for as long as possible.
Summary Table:
Factor | Impact on PVD Coating Lifespan |
---|---|
Substrate Type | Materials like stainless steel or titanium affect adhesion and durability. |
Coating Thickness | Thicker coatings last longer due to increased wear resistance. |
Bond Strength | Stronger bonds between coating and substrate enhance longevity. |
Environmental Exposure | High temperatures, chemicals, and physical wear can reduce lifespan. |
Maintenance Practices | Regular cleaning and avoiding harsh chemicals help preserve the coating. |
Usage Patterns | Daily wear and tear may accelerate degradation. |
Want to learn more about PVD coatings or need advice on maintaining your watch? Contact our experts today!