Sintering is a critical process in materials science, where powdered materials are heated to a temperature below their melting point to form a solid mass. The duration of sintering can vary significantly depending on factors such as the material being sintered, the desired properties of the final product, and the specific sintering method used. Typically, sintering can take anywhere from a few minutes to several hours. The process involves three main stages: shaping the powder with a bonding agent, removing the bonding agent through heating, and finally fusing the particles at high temperatures. The sintering furnace plays a crucial role in maintaining the precise temperatures required for each stage, ensuring the material achieves the desired density and strength.
Key Points Explained:
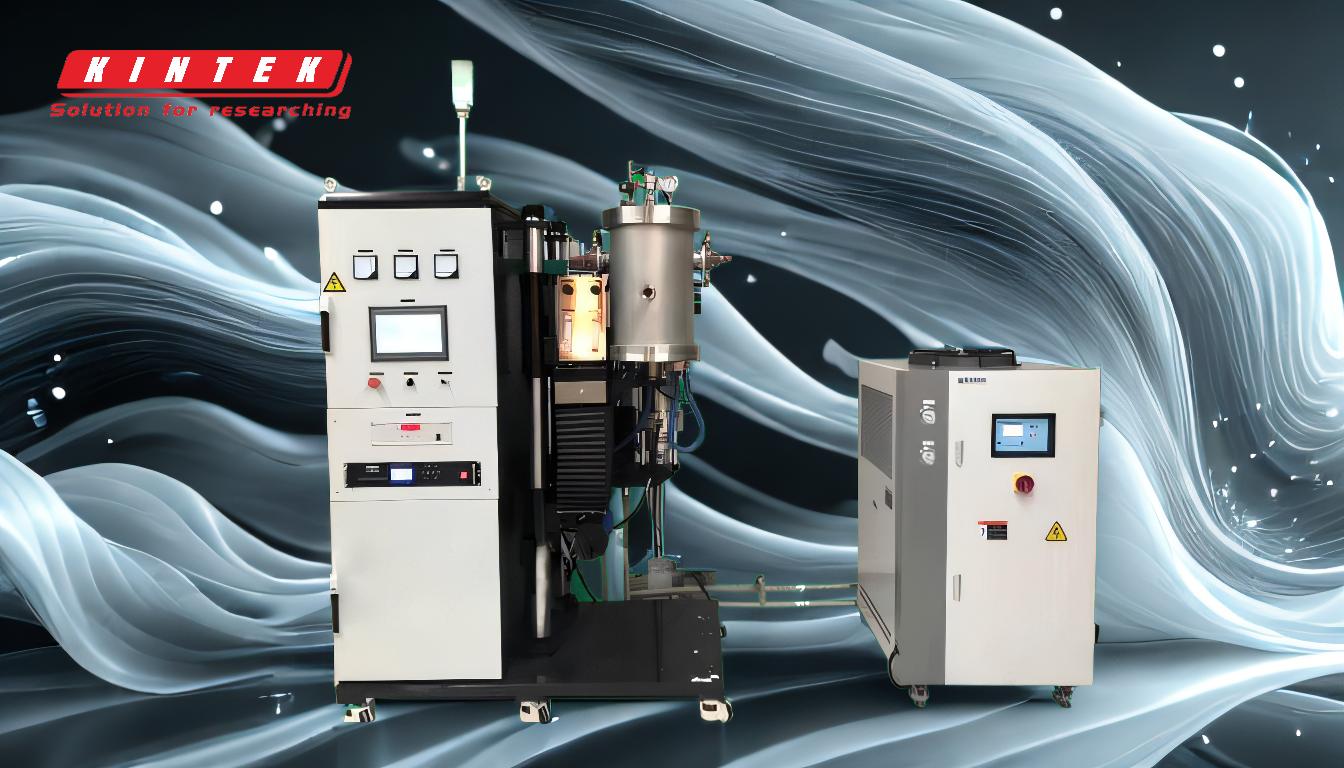
-
Stages of the Sintering Process:
- Initial Shaping: The process begins with the formation of a green part, where a powder blend is mixed with a bonding agent (such as water, wax, or polymer) and shaped into the desired form. This stage sets the foundation for the sintering process.
- Bonding Agent Removal: During heating, the bonding agent evaporates or burns away. This step is crucial as it prepares the material for the actual sintering by removing any temporary binders that were used to shape the powder.
- Particle Fusion: The temperature is then increased to a point where the primary particles begin to melt at their surfaces, causing them to fuse together. In some cases, an intermediate bonding agent like bronze may melt and act as a coupling agent between the particles, leaving the primary component powder unaltered.
-
Role of the Sintering Furnace:
- The sintering furnace is essential for maintaining the precise temperatures required for each stage of the sintering process. It ensures that the material is heated uniformly and consistently, which is critical for achieving the desired material properties.
- The furnace must be capable of reaching and maintaining temperatures just below the melting point of the material, as this is where the sintering process occurs. The controlled environment within the furnace prevents oxidation and other undesirable reactions that could affect the quality of the sintered product.
-
Factors Affecting Sintering Time:
- Material Type: Different materials have different sintering temperatures and times. For example, metals like steel or titanium may require longer sintering times compared to ceramics.
- Desired Properties: The final properties of the sintered product, such as density, strength, and porosity, can influence the sintering time. Higher density and strength typically require longer sintering times.
- Sintering Method: Various sintering methods, such as pressureless sintering, hot pressing, or spark plasma sintering, can affect the duration of the process. Each method has its own set of parameters that influence the time required for sintering.
-
Post-Sintering Processes:
- After sintering, the parts may undergo additional treatments such as calibration or other post-sintering processes to achieve the desired specifications. Calibration involves placing the piece back in the press and adjusting it using a calibration die. This stage ensures that the final product meets the required tolerances and quality standards.
- These post-sintering processes can add to the overall time required to produce the final product, but they are essential for ensuring that the sintered parts meet the necessary performance criteria.
In summary, the duration of the sintering process is influenced by several factors, including the material being sintered, the desired properties of the final product, and the specific sintering method used. The sintering furnace plays a pivotal role in controlling the temperature and environment necessary for successful sintering, while post-sintering processes ensure that the final product meets the required specifications.
Summary Table:
Factor | Impact on Sintering Time |
---|---|
Material Type | Metals (e.g., steel, titanium) take longer than ceramics. |
Desired Properties | Higher density and strength require longer sintering times. |
Sintering Method | Methods like hot pressing or spark plasma sintering vary. |
Post-Sintering | Additional processes like calibration add to total time. |
Need help optimizing your sintering process? Contact our experts today for tailored solutions!