Sintering is a critical process in powder metallurgy where metal powders are compacted and heated to just below their melting point to bond particles together, enhancing the material's strength, density, and structural integrity. For copper powder, the sintering process involves heating the compacted powder to a specific temperature (typically around 800°C to 950°C) in a controlled environment. The duration of sintering depends on factors such as the desired density, particle size, and the specific application of the final product. Generally, sintering times for copper powder can range from 30 minutes to several hours, depending on the complexity of the part and the sintering method used. The process is carefully controlled to ensure optimal bonding of particles while minimizing porosity and maintaining the material's beneficial properties.
Key Points Explained:
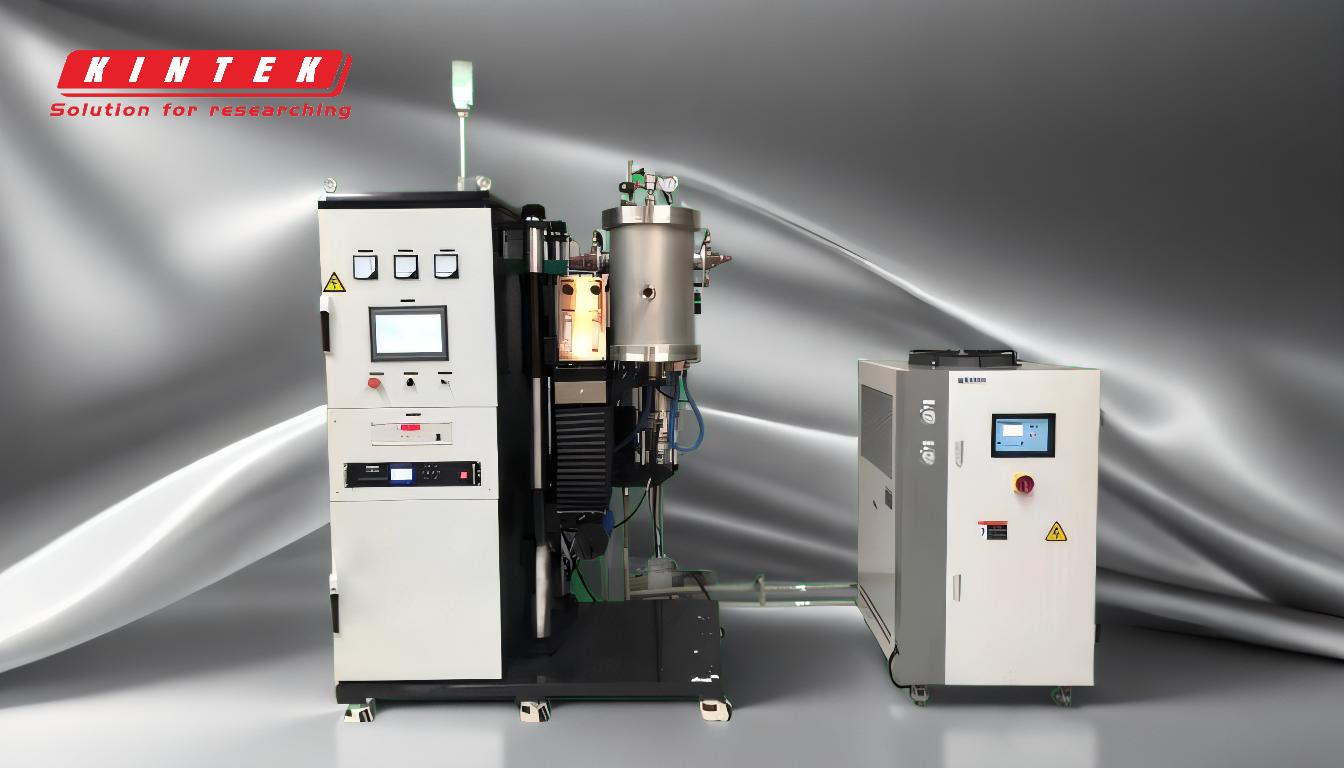
-
Definition of Sintering:
- Sintering is a thermal process used in powder metallurgy to bond metal particles by heating them to just below their melting point. This process enhances the structural integrity, density, and mechanical properties of the final product. For copper powder, sintering is essential to create parts with high strength and durability.
-
Temperature and Environment:
- Copper powder is typically sintered at temperatures ranging from 800°C to 950°C. The process is conducted in a controlled environment, often in a muffle furnace, to prevent oxidation and ensure uniform heating. The temperature must be carefully regulated to avoid melting the powder while achieving sufficient particle bonding.
-
Duration of Sintering:
- The sintering time for copper powder varies based on the desired properties of the final product. For simple shapes and smaller parts, sintering may take around 30 minutes to 1 hour. For more complex parts or higher-density requirements, the process can extend to several hours. The duration is influenced by factors such as particle size, compacted density, and the sintering method.
-
Factors Influencing Sintering Time:
- Particle Size: Smaller particles sinter faster due to their higher surface area-to-volume ratio, which promotes quicker diffusion and bonding.
- Compacted Density: Higher initial density of the compacted powder reduces the sintering time as there is less porosity to eliminate.
- Sintering Method: Different methods, such as conventional sintering, spark plasma sintering, or microwave sintering, can affect the time required. For example, spark plasma sintering significantly reduces sintering time compared to conventional methods.
-
Mechanisms of Sintering:
- Sintering involves several mechanisms, including surface diffusion, bulk diffusion, and grain boundary diffusion. These mechanisms work together to reduce porosity and increase the density of the material. In copper powder, these processes are crucial for achieving a strong, durable final product.
-
Challenges and Limitations:
- One of the main challenges in sintering copper powder is managing porosity. While some porosity may be desirable for specific applications, excessive porosity can weaken the final part. Additionally, the complexity of the part's shape can limit the effectiveness of sintering, as intricate designs may require longer sintering times or specialized techniques.
-
Applications of Sintered Copper Parts:
- Sintered copper parts are used in various industries, including electronics, automotive, and aerospace, due to their excellent thermal and electrical conductivity. The sintering process ensures that these parts meet the required mechanical and functional properties for their intended applications.
By understanding these key points, one can better appreciate the intricacies of the sintering process for copper powder and make informed decisions regarding temperature, duration, and method to achieve the desired results.
Summary Table:
Factor | Impact on Sintering Time |
---|---|
Temperature | Typically 800°C–950°C; higher temperatures may reduce time but risk melting. |
Particle Size | Smaller particles sinter faster due to higher surface area-to-volume ratio. |
Compacted Density | Higher density reduces sintering time by minimizing porosity. |
Sintering Method | Methods like spark plasma sintering significantly reduce time compared to conventional ones. |
Part Complexity | Complex shapes or higher-density requirements may extend sintering time. |
Need help optimizing your sintering process for copper powder? Contact our experts today for tailored solutions!