The number of plates used in an injection mold depends on the design and complexity of the mold. Typically, molds are designed as either two-plate or three-plate molds. Two-plate molds are simpler and consist of two main plates: one for the core and one for the cavity. These molds are commonly used for straightforward parts and require less setup time. Three-plate molds, on the other hand, include an additional plate, allowing for more complex part designs and automated part ejection. The choice between two-plate and three-plate molds depends on the part geometry, production requirements, and cost considerations.
Key Points Explained:
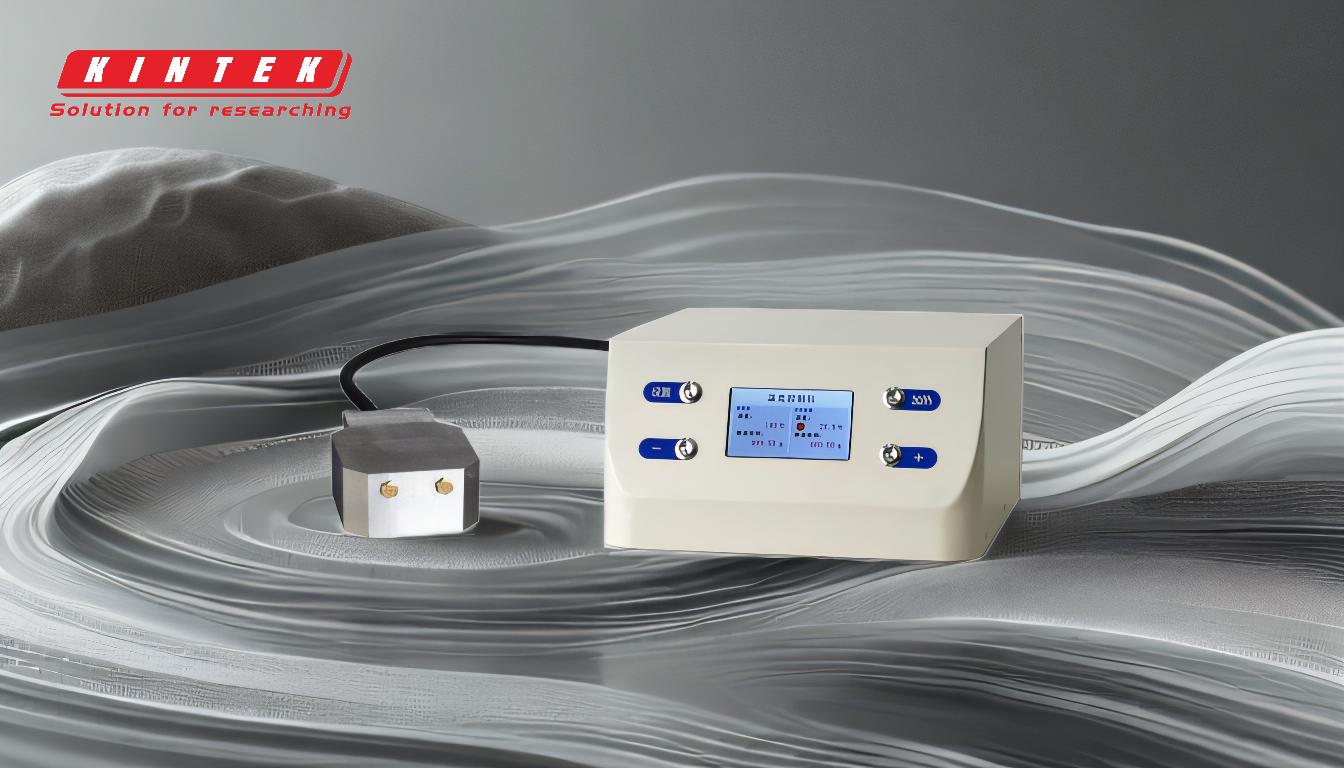
-
Two-Plate Molds:
- Structure: Consists of two main plates: one for the core and one for the cavity.
- Usage: Ideal for simpler parts with straightforward geometries.
-
Advantages:
- Easier to design and manufacture.
- Lower cost due to fewer components.
- Faster setup and shorter production cycles.
- Disadvantages: Limited flexibility for complex part designs or automated ejection systems.
-
Three-Plate Molds:
- Structure: Includes an additional plate, making it a three-plate system.
- Usage: Suitable for more complex parts that require multiple gating or automated ejection.
-
Advantages:
- Greater flexibility in part design.
- Allows for multiple gating points, improving part quality.
- Supports automated part ejection, reducing manual labor.
-
Disadvantages:
- More complex design and manufacturing process.
- Higher cost due to additional components.
- Longer setup time and production cycles.
-
Factors Influencing the Choice:
- Part Complexity: Complex parts with intricate geometries or multiple features may require a three-plate mold.
- Production Volume: High-volume production may benefit from the efficiency of two-plate molds, while low-volume or custom parts may require the flexibility of three-plate molds.
- Cost Considerations: Two-plate molds are generally more cost-effective, but the added functionality of three-plate molds may justify the higher cost for certain applications.
- Cycle Time: Two-plate molds typically have shorter cycle times, making them more suitable for high-speed production.
-
Practical Considerations:
- Tooling and Maintenance: Three-plate molds require more sophisticated tooling and maintenance, which can impact long-term operational costs.
- Material Flow: The design of the mold plates affects the flow of molten plastic, influencing part quality and consistency.
- Ejection Mechanism: Three-plate molds often include automated ejection systems, which can improve production efficiency but add to the complexity of the mold.
By understanding these key points, a purchaser can make an informed decision on whether to opt for a two-plate or three-plate mold based on the specific requirements of their project.
Summary Table:
Feature | Two-Plate Molds | Three-Plate Molds |
---|---|---|
Structure | Two main plates (core and cavity) | Three plates (additional plate included) |
Usage | Simple parts with straightforward designs | Complex parts with multiple gating |
Advantages | Easier design, lower cost, faster setup | Greater flexibility, automated ejection |
Disadvantages | Limited flexibility for complex designs | Higher cost, longer setup time |
Ideal For | High-volume, simple geometries | Low-volume, complex geometries |
Still unsure which mold is right for your project? Contact our experts today for personalized advice!