Rolling mills are essential equipment in metalworking, designed to shape and process metals into various forms such as bars, rods, plates, and more. They are categorized based on their design, functionality, and application. The primary types of rolling mills include two-high, three-high, four-high, cluster, continuous, and planetary rolling mills. Each type serves specific purposes, ranging from small-scale laboratory work to large-scale industrial production. Additionally, rolling mills can be classified as hot or cold, depending on the temperature at which the metal is processed. Understanding these variations helps in selecting the right rolling mill for specific metalworking needs.
Key Points Explained:
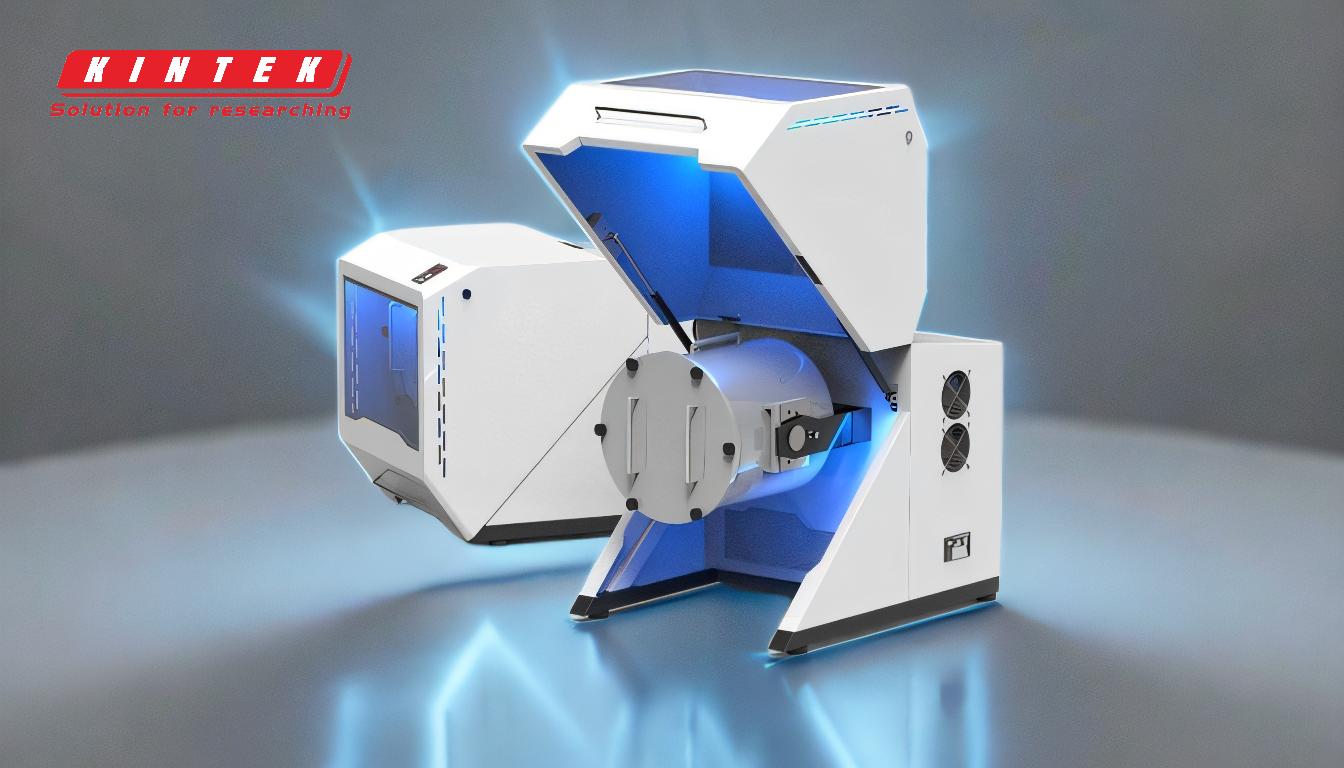
-
Two-High Rolling Mills:
- Description: These are the simplest and most common type of rolling mills, consisting of two rolls that rotate in opposite directions.
- Applications: Used for both hot and cold rolling processes, suitable for producing bars, rods, and plates.
- Variants: Can be reversible (rolls can change direction) or non-reversible (rolls move in one direction only).
-
Three-High Rolling Mills:
- Description: Equipped with three rolls, where the metal passes through the upper and middle rolls in one direction and then through the middle and lower rolls in the opposite direction.
- Applications: Ideal for continuous rolling processes, often used in high-volume production.
- Variants: Includes electric heating, steam-heating, granite rollers, ceramic rollers, and rust-free rollers.
-
Four-High Rolling Mills:
- Description: Features four rolls, with two smaller work rolls supported by two larger backup rolls. This design reduces roll deflection and allows for higher precision.
- Applications: Commonly used for rolling thin sheets and strips, especially in cold rolling processes.
- Advantages: Provides better control over thickness and surface finish.
-
Cluster Rolling Mills:
- Description: Consists of multiple rolls arranged in a cluster, typically with one or two work rolls supported by several backup rolls.
- Applications: Used for rolling very thin materials, such as foil, where high precision and minimal deflection are required.
- Advantages: Offers superior roll support, enabling the production of ultra-thin materials.
-
Continuous Rolling Mills:
- Description: Comprises multiple stands of rolls arranged in a sequence, allowing the metal to pass through several rolling stages in a continuous process.
- Applications: Suitable for high-volume production of long products like bars, rods, and wire rods.
- Advantages: Increases production efficiency and consistency by reducing the need for manual intervention.
-
Planetary Rolling Mills:
- Description: Features a central roll surrounded by multiple smaller rolls, which rotate around the central roll. This design allows for high reduction ratios in a single pass.
- Applications: Used for rolling thick slabs into thinner sheets or plates.
- Advantages: Capable of achieving significant thickness reduction in a single pass, making it efficient for large-scale production.
-
Hot vs. Cold Rolling Mills:
- Hot Rolling Mills: Operate at high temperatures, typically above the metal's recrystallization temperature. This process is used for shaping large metal pieces and improving material properties.
- Cold Rolling Mills: Operate at or near room temperature, used for finishing processes to achieve precise dimensions, smooth surfaces, and improved mechanical properties.
-
Specialized Rolling Mills:
- Small Bench Models: Designed for low-volume production, laboratory work, and bench-top development. These are manually operated and ideal for small-scale applications.
- Large Industrial Models: Powered machines designed for high-volume manufacturing, capable of handling large-scale production needs.
By understanding these types of rolling mills, purchasers can make informed decisions based on the specific requirements of their metalworking processes, whether they need precision, high-volume production, or specialized applications.
Summary Table:
Type of Rolling Mill | Description | Applications | Advantages |
---|---|---|---|
Two-High | Two rolls rotating in opposite directions | Bars, rods, plates | Simple, versatile |
Three-High | Three rolls for continuous rolling | High-volume production | Efficient, reversible |
Four-High | Four rolls with backup support | Thin sheets, strips | Precise, better surface finish |
Cluster | Multiple rolls in a cluster | Ultra-thin materials (e.g., foil) | High precision, minimal deflection |
Continuous | Multiple stands in sequence | Bars, rods, wire rods | High efficiency, consistent output |
Planetary | Central roll with surrounding rolls | Thick slabs to thin sheets | High reduction in a single pass |
Hot Rolling | High-temperature processing | Shaping large metal pieces | Improved material properties |
Cold Rolling | Room-temperature processing | Precise dimensions, smooth surfaces | Enhanced mechanical properties |
Need help choosing the right rolling mill for your metalworking needs? Contact our experts today for personalized advice!