The cost of biochar pyrolysis varies significantly depending on the scale of the operation, the type of pyrolysis reactor used, feedstock availability, and operational efficiency. Small-scale systems may cost between $10,000 to $50,000, while large-scale industrial setups can range from $100,000 to several million dollars. Key factors influencing costs include the reactor type (e.g., batch, continuous, or semi-continuous), feedstock preprocessing, energy requirements, and labor. Additionally, operational costs such as maintenance, feedstock transportation, and compliance with environmental regulations play a significant role. Understanding these variables is crucial for estimating the total cost of biochar production.
Key Points Explained:
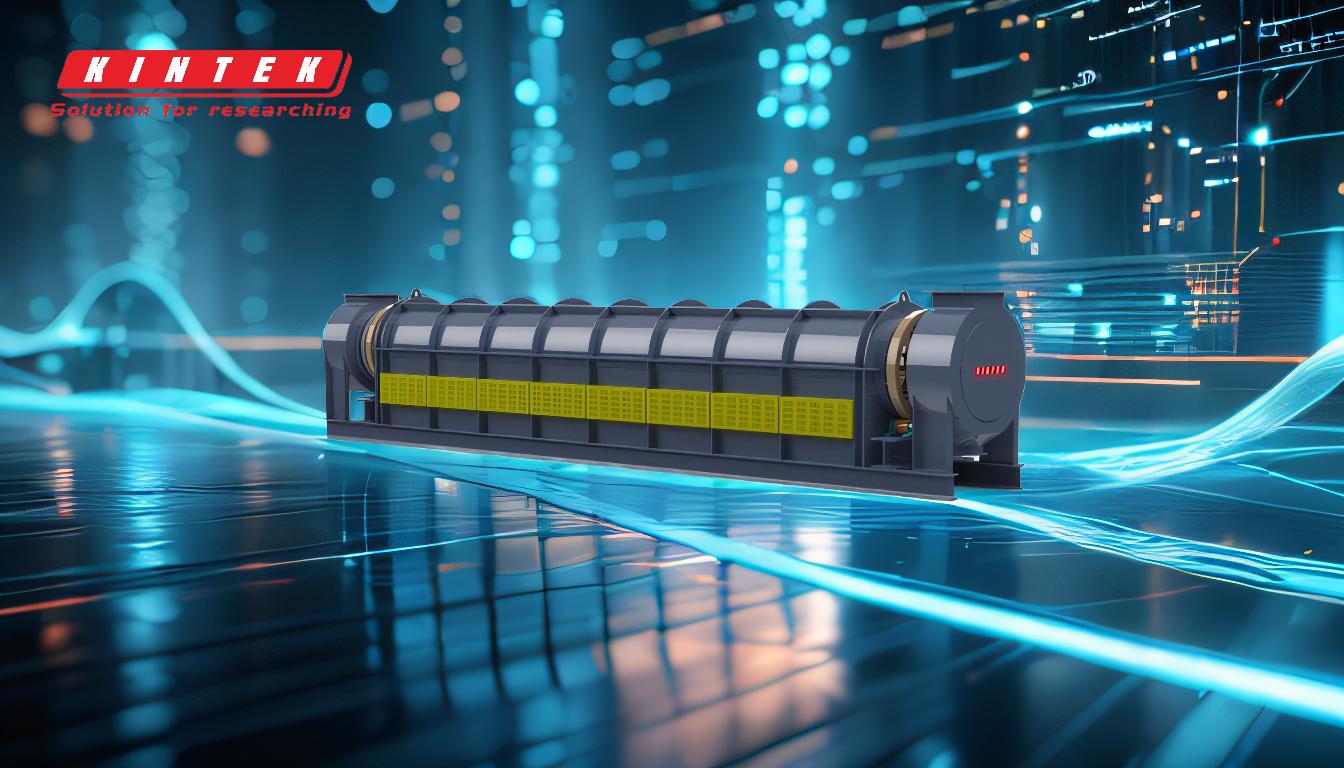
-
Types of Pyrolysis Reactors and Their Costs:
- Batch Reactors: These are typically used for small-scale operations and are less expensive, ranging from $10,000 to $50,000. They are suitable for localized or experimental setups but have lower throughput and higher labor costs.
- Continuous Reactors: Designed for large-scale industrial production, these reactors can cost anywhere from $100,000 to several million dollars. They offer higher efficiency and automation but require significant upfront investment.
- Semi-Continuous Reactors: These fall between batch and continuous systems in terms of cost and throughput, making them a balanced option for medium-scale operations.
The choice of reactor significantly impacts the overall cost, as it determines the scale, efficiency, and labor requirements of the pyrolysis process.
-
Feedstock Costs:
- The type and availability of feedstock directly influence the cost of biochar production. Common feedstocks include agricultural waste, wood chips, and municipal waste.
- Preprocessing costs, such as drying, shredding, and transporting feedstock, can add to the overall expense. For example, wet or bulky feedstocks require more energy and resources to prepare, increasing operational costs.
-
Energy Requirements:
- Pyrolysis is an energy-intensive process, and the cost of energy (electricity, gas, or biomass) is a major factor in the overall expense.
- Efficient reactors, such as those with heat recovery systems, can reduce energy costs by reusing waste heat, but these systems often come with higher initial costs.
-
Labor and Maintenance:
- Labor costs depend on the level of automation. Batch reactors require more manual intervention, while continuous systems are more automated but need skilled technicians for maintenance.
- Regular maintenance of the pyrolysis reactor is essential to ensure optimal performance and longevity, adding to operational expenses.
-
Environmental and Regulatory Compliance:
- Compliance with environmental regulations, such as emissions control and waste management, can increase costs. For instance, installing scrubbers or filters to reduce emissions adds to the capital and operational expenses.
- Certifications and permits may also be required, depending on local regulations, which can involve additional fees and administrative costs.
-
Economies of Scale:
- Larger-scale operations benefit from economies of scale, reducing the per-unit cost of biochar. However, they require higher initial investments and more sophisticated infrastructure.
- Small-scale systems are more affordable upfront but may have higher per-unit costs due to lower efficiency and throughput.
-
Return on Investment (ROI):
- The cost of biochar pyrolysis must be weighed against potential revenue streams, such as selling biochar for agricultural use, carbon credits, or energy production.
- Factors like market demand, feedstock costs, and operational efficiency play a critical role in determining the ROI.
By carefully evaluating these factors, stakeholders can make informed decisions about the feasibility and cost-effectiveness of biochar pyrolysis projects.
Summary Table:
Factor | Cost Range/Impact |
---|---|
Reactor Type | - Batch: $10,000–$50,000 - Continuous: $100,000–$1M+ - Semi-Continuous: Mid-range |
Feedstock | - Agricultural waste, wood chips, municipal waste - Preprocessing adds costs |
Energy Requirements | High energy costs; heat recovery systems reduce expenses but increase upfront costs |
Labor & Maintenance | Batch: Higher labor Continuous: Skilled maintenance |
Environmental Compliance | Emissions control, permits, and certifications add to costs |
Economies of Scale | Larger scales reduce per-unit costs but require higher initial investment |
ROI | Revenue from biochar sales, carbon credits, or energy production affects feasibility |
Ready to explore biochar pyrolysis for your project? Contact our experts today for a tailored solution!