The cost of PVD coating varies significantly depending on factors such as the type of material being coated, the desired coating thickness, the complexity of the part, and the specific PVD process used. Generally, PVD coating costs can range from a few dollars per square inch for simple applications to hundreds or even thousands of dollars for specialized or large-scale projects. The process involves high-vacuum environments, specialized equipment, and precise control of parameters, which contribute to the overall cost. Additionally, surface preparation, coating composition, and post-treatment requirements can further influence the price. For accurate pricing, it is recommended to consult with a PVD coating service provider, as they can offer tailored quotes based on specific project needs.
Key Points Explained:
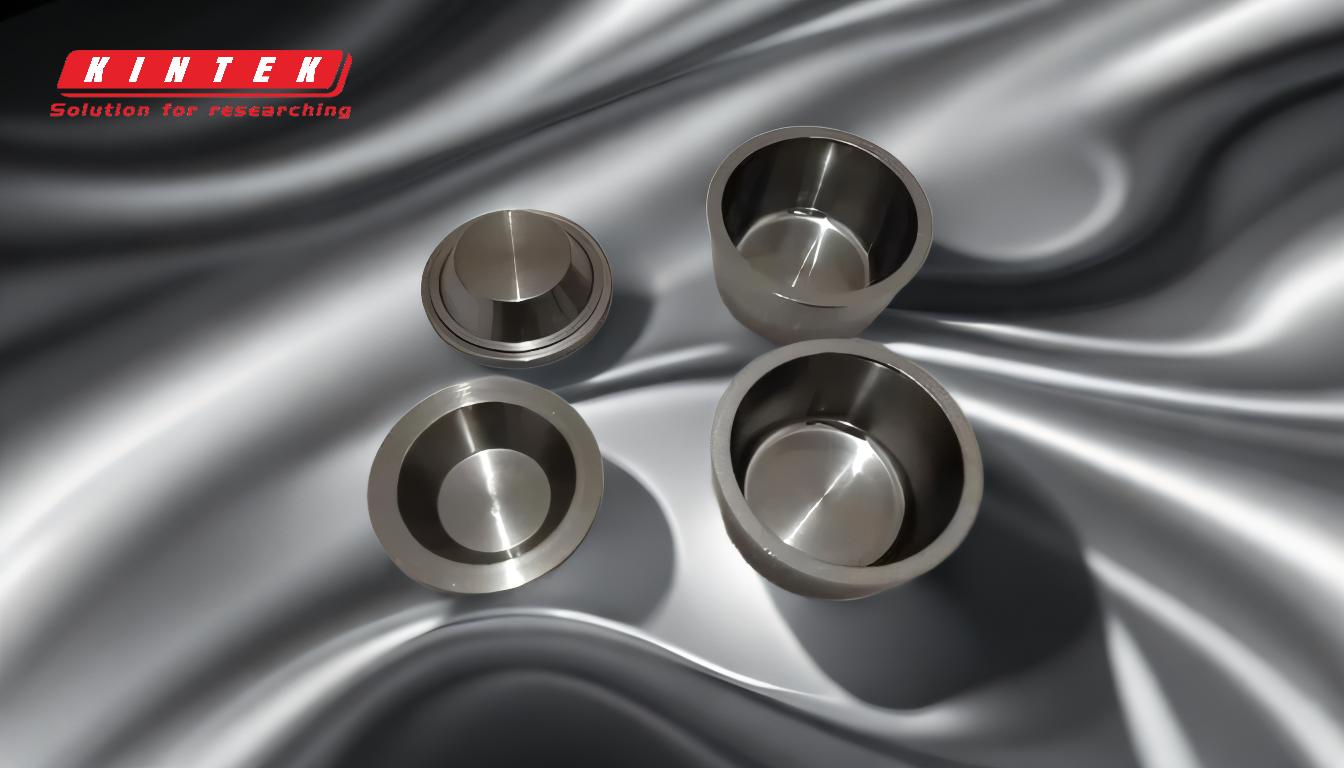
-
Factors Influencing PVD Coating Costs
- Material Type: The substrate material (e.g., metal, ceramic, polymer) and the target material used for coating (e.g., titanium, chromium, aluminum) affect the cost. Exotic materials or rare metals may increase expenses.
- Coating Thickness: Thicker coatings require more time and material, leading to higher costs. The reference mentions that PVD coatings are typically 0.5–5 μm thick, and achieving thicker layers can extend processing time and resource usage.
- Part Complexity: Complex geometries or parts with intricate details may require specialized fixtures or multiple coating cycles, increasing labor and equipment costs.
- Surface Preparation: Proper surface pretreatment, such as cleaning and polishing, is crucial for achieving high-quality coatings. Poor surface preparation can lead to defects, requiring rework and additional expenses.
- Coating Composition: The introduction of reactive gases (e.g., nitrogen, acetylene) to create compound coatings can add to the cost due to the need for precise control and additional materials.
-
PVD Coating Processes and Their Cost Implications
- Evaporation vs. Sputtering: The reference highlights two common PVD processes—evaporation (using cathodic arc or electron beam sources) and sputtering (using magnetrons or hollow cathode sources). Sputtering is generally more expensive due to its higher energy requirements and slower deposition rates, but it offers better uniformity and adhesion.
- Vacuum Environment: PVD processes occur in a high-vacuum environment (10⁻² to 10⁻⁴ mbar), which requires specialized equipment and energy consumption, contributing to the overall cost.
-
Equipment and Operational Costs
- Vacuum Coating Machines: The reference mentions that companies provide vacuum coating machines and turnkey projects. The cost of purchasing or renting such equipment can be substantial, especially for high-end or customized systems.
- Labor and Expertise: Skilled technicians are required to operate PVD coating equipment and ensure quality control. Labor costs can vary depending on the complexity of the project and the expertise needed.
- Maintenance and Consumables: Regular maintenance of vacuum chambers, targets, and other components, as well as the replacement of consumables like sputtering targets, add to the operational costs.
-
Customization and Turnkey Solutions
- Tailored Solutions: The reference notes that companies offer customized coating solutions to meet specific customer requirements. Customization often involves additional research, development, and testing, which can increase costs.
- Turnkey Projects: For large-scale or complex projects, turnkey solutions that include design, equipment, and implementation may be more cost-effective in the long run but require a higher upfront investment.
-
Surface Treatment and Quality Requirements
- Surface Cleanliness: The reference emphasizes that even small particles can affect coating quality. Ensuring surface cleanliness may involve additional cleaning steps or specialized equipment, adding to the cost.
- Coating Uniformity and Adhesion: Achieving a uniform coating with strong adhesion may require multiple coating cycles or post-treatment processes, increasing time and resource usage.
-
Volume and Economies of Scale
- Small vs. Large Batches: Small batches or one-off projects tend to have higher per-unit costs due to setup and calibration requirements. Larger volumes benefit from economies of scale, reducing the per-unit cost.
- Production Efficiency: The reference mentions that companies combine full-set production techniques to ensure high efficiency. Efficient production processes can help reduce costs for high-volume orders.
-
Additional Considerations
- Post-Coating Treatments: Some applications may require additional treatments, such as polishing or heat treatment, to enhance coating properties. These steps add to the overall cost.
- Environmental and Safety Compliance: Adhering to environmental regulations and ensuring workplace safety during PVD coating processes may involve additional expenses for equipment, training, and certifications.
In conclusion, the cost of PVD coating is influenced by a wide range of factors, including material choices, process complexity, equipment requirements, and customization needs. For an accurate cost estimate, it is essential to consult with a PVD coating service provider who can assess the specific requirements of your project and provide a detailed quote.
Summary Table:
Factor | Impact on Cost |
---|---|
Material Type | Exotic or rare materials increase costs. |
Coating Thickness | Thicker coatings require more time and resources, raising costs. |
Part Complexity | Complex geometries or intricate details increase labor and equipment costs. |
Surface Preparation | Additional cleaning or polishing steps add to expenses. |
Coating Composition | Reactive gases and precise control increase material and operational costs. |
PVD Process | Sputtering is more expensive than evaporation due to higher energy requirements. |
Volume | Small batches have higher per-unit costs; larger volumes benefit from economies of scale. |
Need a precise cost estimate for your PVD coating project? Contact us today for a tailored quote!